THIS ARTICLE/PRESS RELEASE IS PAID FOR AND PRESENTED BY SINTEF - read more
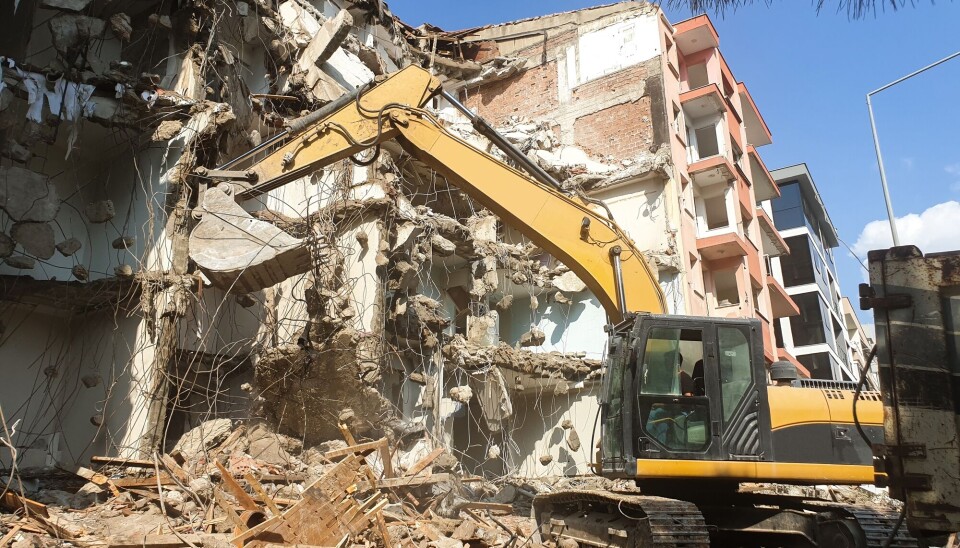
Old buildings become new concrete
Christian John Engelsen is teaching the world to recycle demolition rubble to make new concrete. Anything and everything can be recycled, he says. What takes time is getting people on board.
Engelsen is a chief research scientist looking into making concrete more sustainable, and buildings more eco-friendly. He is currently coordinating research projects focusing on recycled construction aggregates.
In the building sector, the term construction aggregates refers to the sand, gravel and crushed rock that we mix together to make concrete and asphalt.
These aggregates make up about two-thirds of the volume of concrete. In other words, the cement and water that we also mix in forms a relatively small proportion of finished concrete. However, it is this fraction that enables the concrete to harden, giving us the basis for robust and resilient buildings.
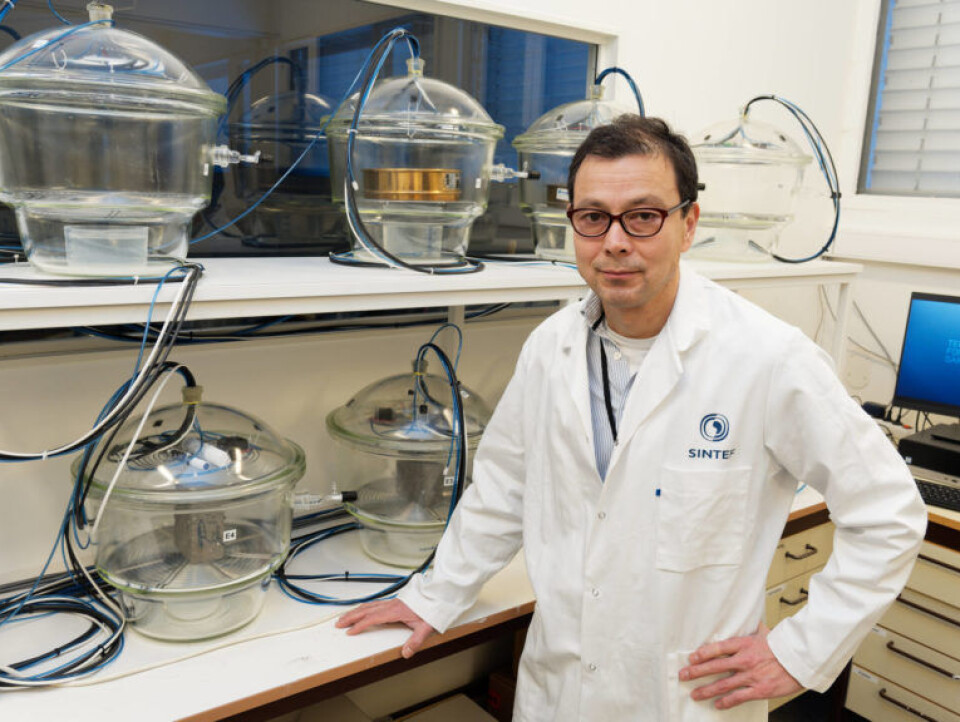
Crushed and sorted
“In Norway, we started looking into this at the end of the 1990s with the idea of recycling bricks and concrete," Engelsen says.
When you demolish a building made of bricks or concrete, you crush the demolition waste and sort the rock from the sand in order to reuse the materials to make new concrete.
"These recycled construction aggregates all have potential applications where you might otherwise use natural raw materials. Such an approach could be more widely applied than it is today,” he insists.
Engelsen is referring to both road construction and new buildings.
A trend is now developing towards the more commercial application of these recycled materials. The problem is that they are physically very heavy, and access is widely dispersed. For this reason, you want to organise a construction project so that the recycled aggregates can be crushed on site, but then it may be difficult to establish to how suitable the suitable material is.
The alternative involves long-distance and environmentally-damaging transport, or the use of centralised facilities that can recycle mixed and contaminated demolition waste.
“Here it is also possible to achieve stable production even if the quality of the construction aggregates that we want to recycle is variable,” Engelsen says.
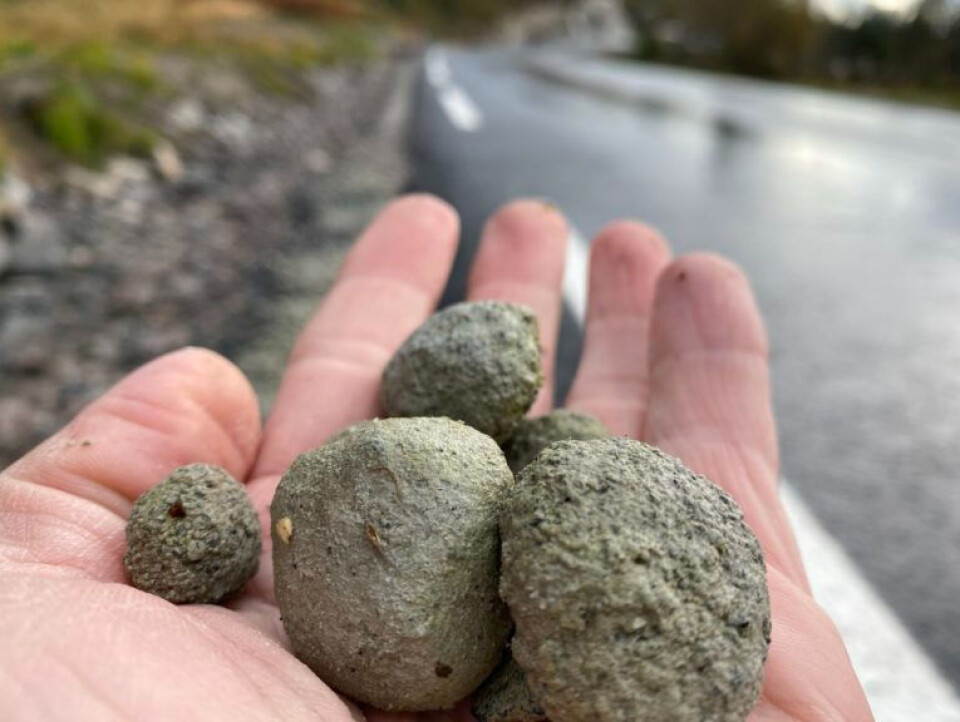
Concrete slurry
“It isn’t only the aggregate component that can be recycled. We’re also looking into how we can exploit the old cement paste contained in demolition waste. We can separate this out and use it as a bonding agent in new concrete. Exploitation of the fine fraction in crushed concrete is the latest trend in our field of research,” Engelsen says.
Commercial European companies are also looking into these recycled fine-fraction cement replacements.
In Norway, research is also being carried out into how concrete slurries derived from the dry washing of truck mixers can be recycled as useful aggregates. This has the potential to reduce the volume of slurry waste sent to landfill, and the consumption of washing water by between 80 - 90 per cent.
“The potential for recycling all the components in old concrete certainly exists, but nothing is being done about this at present. Three things have to be in place before this can happen," Engelsen says. “The first is to establish reliable levels of quality, which then have to be documented. The second is accessibility. The construction sector must have access to recycled aggregates when and where it needs them. The third is cost-effectiveness."
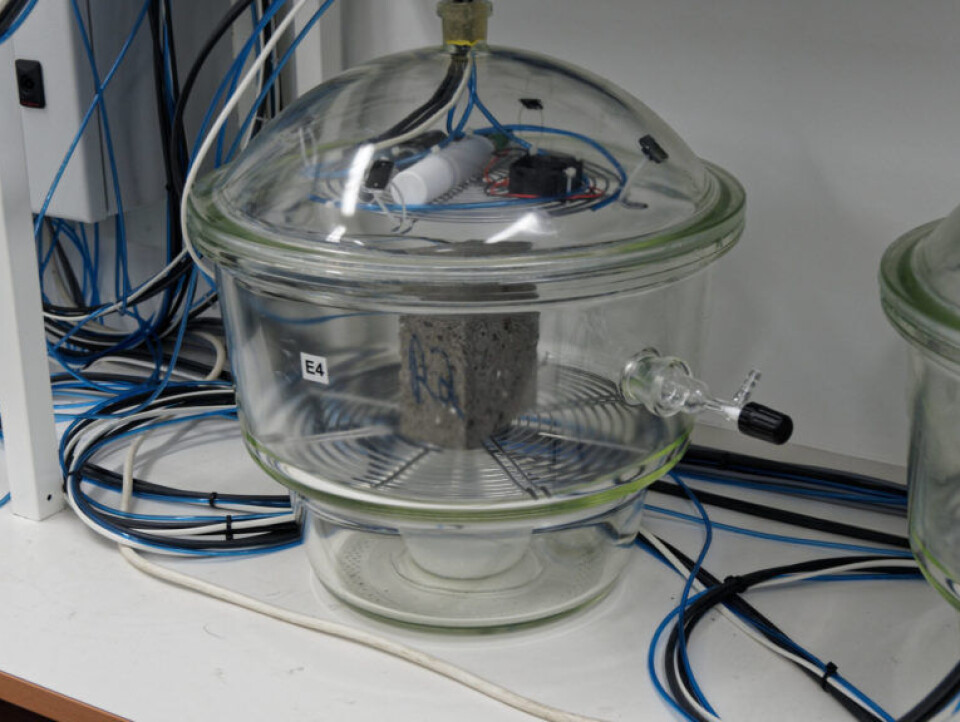
Trials in India
As part of a joint Indian-Norwegian research project, Engelsen is currently in the process of teaching the Indian construction sector how to recycle its concrete. Naturally enough, in a country that is ten times the size of Norway, and with 250 times the population, the need and the opportunities are much greater.
“It’s potentially possible to recycle everything, but it takes a while to get everyone in the right mindset," Engelsen argues.
In his laboratory in Oslo, Engelsen keeps glass jars, each containing its own block of concrete made of a different recycled aggregate. He uses these to find out how much CO2 the various aggregate mixtures can absorb.
Concrete, of course, contributes to greenhouse gas emissions, and manufacture of the cement binding agent makes the greatest contribution. However, concrete buildings also absorb CO2 during their lifetimes, and researchers are working to find out how the absorption process can be optimised.
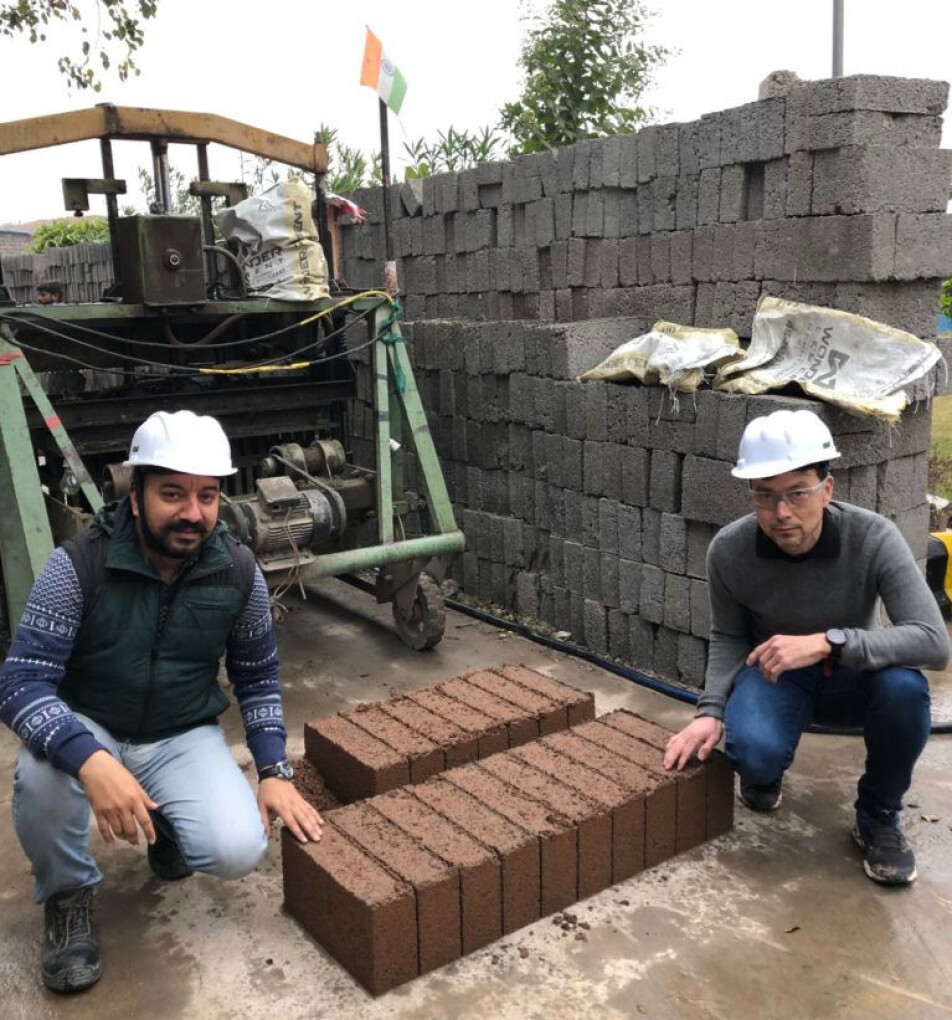
Transport and natural resources
“The recycling and reuse of demolition waste can help a great deal towards reducing transport to landfill sites that are usually located at some distance from the towns and cities. This enables us not only to reduce the over-extraction of natural resources, but also to limit the danger of demolition waste being dumped only to become a source of pollution," Engelsen says. “This is a crucial initiative in Norway, but in a country such as India, where many hundreds of millions of tonnes of demolition waste are generated every year, it’s even more important to have a sustainable pollution prevention strategy in place."
See more content from SINTEF:
-
Testing a giant ship: May take five kilometres to stop
-
A robot is helping researchers hunt for the best cancer warriors
-
Locomotives that run on diesel can be electrified
-
Where kelp is being turned into lab-grown meat
-
Immediate action is a key factor for successful restoration of marine habitats
-
Dynamic cables – the umbilical cord of ocean installations