THIS CONTENT IS BROUGHT TO YOU BY SINTEF - read more
Dynamic cables – the umbilical cord of ocean installations
Powering offshore structures means handling not just electricity and weather, but also saltwater, ocean currents, temperature shifts, and constant movement.
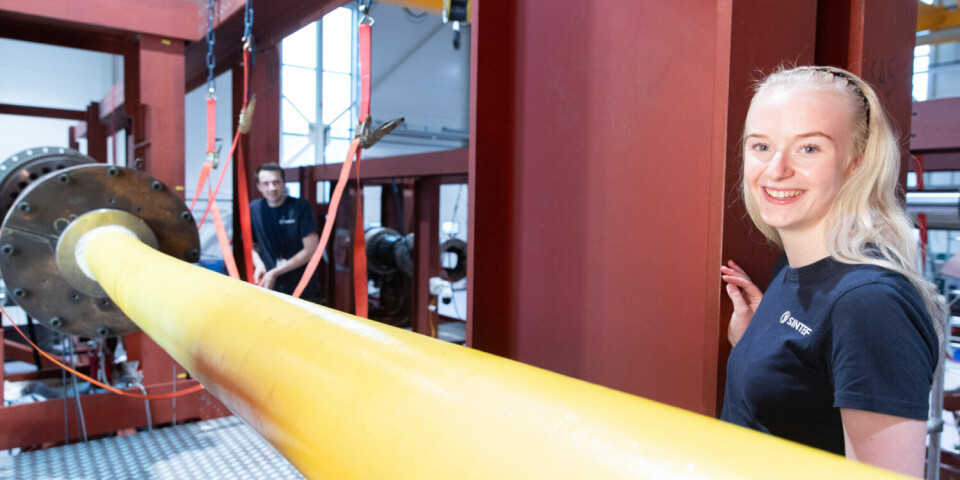
Dynamic underwater cables are built for these harsh conditions. They are large, robust, and flexible – designed to withstand the forces found of the ocean and the demands of floating solar power plants, offshore fish cages, oil and gas platforms, and offshore wind turbines.
These dynamic cables act like an umbilical cord, linking static underwater cables to floating structures.
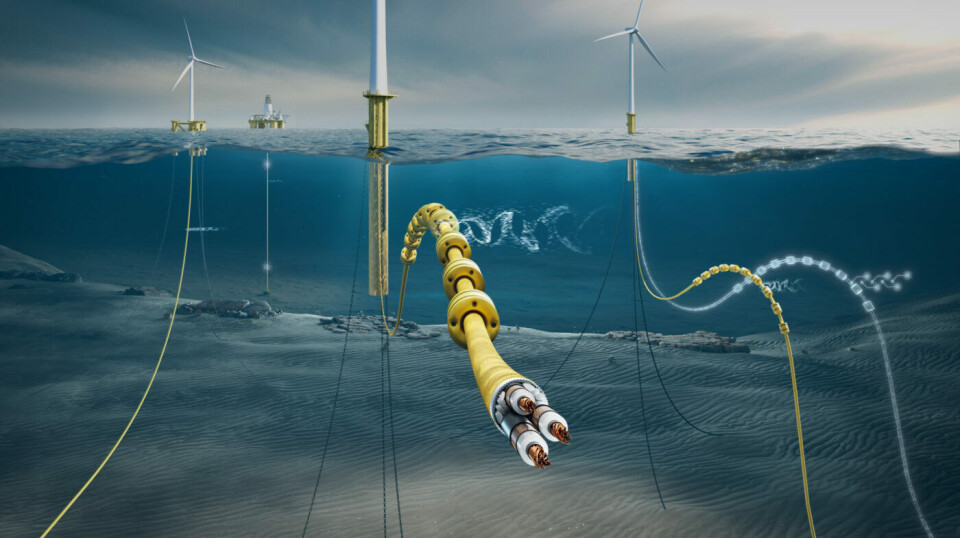
“They’re a bit like the power cables we have for all the electrical gadgets that we connect via a plug to the fixed cables in the wall,” says Naiquan Ye, a SINTEF research manager.
Ye works to make these cables more robust, a key factor in reducing project costs.
“According to the current plans, Europe will need 6,000 kilometres of underwater power cables annually. That’s as far as the distance from Norway to Bermuda,” he says.
Under extreme stress
Cables in our walls rarely break – but how often have we had to replace charging cables or extension cords because they have been bent too many times?
According to Lloyd Warwick, a company that specialises in claim settlements for the insurance industry, 83 per cent of offshore wind insurance claims are due to cable faults.
The cables heat up from the electric current and are constantly moved by waves, currents, and the shifting position of floating structures.
These cables have multiple layers to ensure reliable power flow. Each layer needs to be waterproof, carry control signals, be unaffected by magnetism, not leak electricity, and also withstand the stresses of constant movement in both icy and warm seawater.
Lowering costs
It's no surprise that these cables are expensive to produce. Until now, demand has been low and mostly come from oil and gas companies with the budget to pay a little extra for safety.
This is changing with the transition to renewable energy.
Renewables often operate with tighter budgets. Unlike oil platforms that may just need one cable, each wind turbine in an offshore wind farm needs its own dynamic underwater cable.
So, the challenge is to design cables that are cost-effective but still durable.
This is where Ye’s team comes in. Through many years of simulating and testing cables, the group has learned a lot about how the different components of these cables behave and how they handle internal and external stresses.
“Since the 1980s, SINTEF researchers have developed advanced models to simulate the properties of cables in complex marine environments. These numerical tools are world-leading, and the industry uses them to ensure safe and sustainable production of ocean-based energy, both in the oil and gas and offshore wind industries,” says Ye.
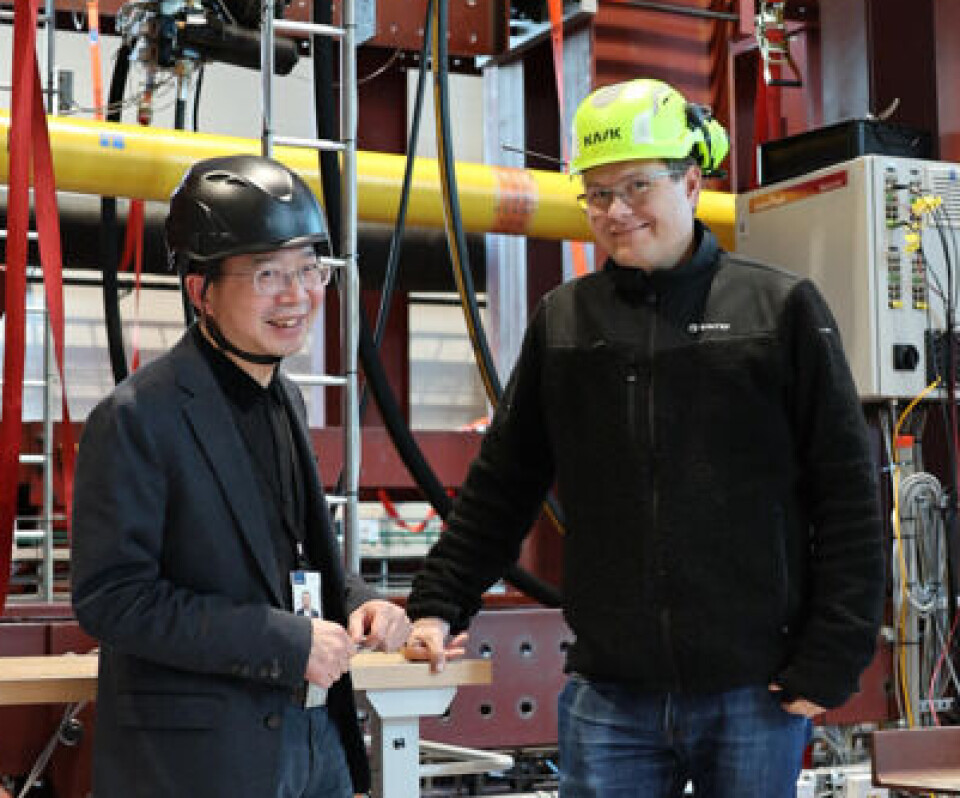
Fighting fatigue
The biggest threat to a cable’s lifespan is fatigue. Simply put, the materials wear out. When electricity flows through, the cable bends and moves, like a garden hose when you turn on the water.
For a hose, this is not a problem. But in an electric cable, there are multiple metal wires. If you twist and turn them too much, they will eventually crack and then break.
Then there are the insulating materials, like a data cable that transmits control signals, and the cable itself. All of them consist of different materials that can withstand different amounts of movement over time.
Every part moves in its own way. Just like the outer layer of a household cable moves more freely once the inside is removed.
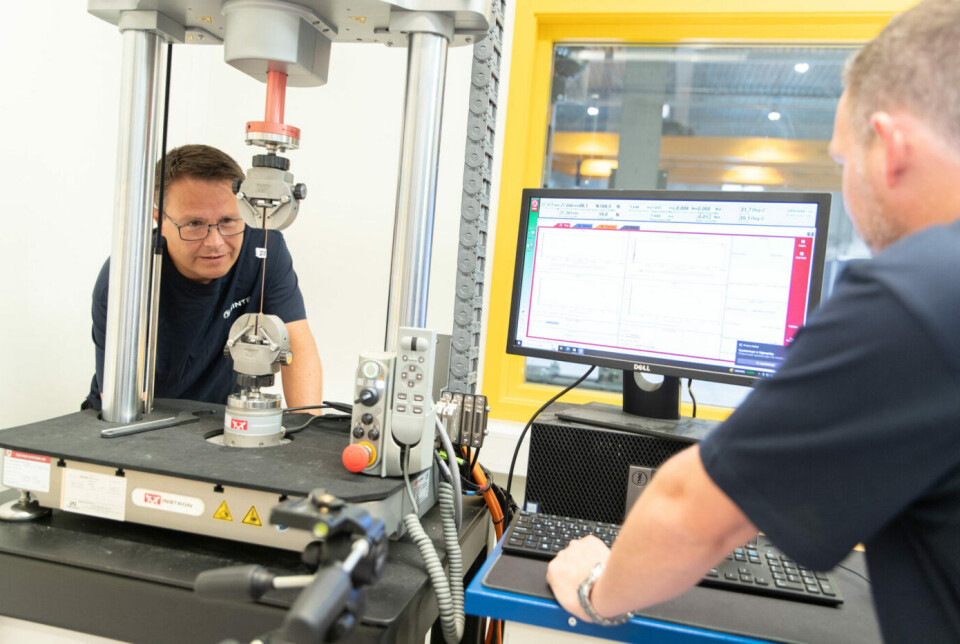
Numerical calculations fall short
“However, the properties and movements of cables are much more complicated than numerical models can predict. Impurities in the material, production, installation, and the environment they are in, like temperature, can affect the lifespan of cables,” says Ye.
This is why laboratory testing is essential. In the lab, researchers monitor how the cables behave in real life. The results are fed back into the numerical tools to find more precise methods for estimating the service life of the cables.
“If lab testing is done early in an offshore wind project, it can significantly reduce the cost of the power cables while optimising the design,” says Ye.
By twisting and bending the cable in a test rig, researchers can see how the different components of the cable move relative to each other. Often, parts slide against each other, and these movements are non-linear – friction makes them unpredictable.
That is why it is so difficult to calculate how a cable and its contents move.
Full-scale testing shows how much strain a cable can handle, how strong it is, and what will ultimately be the weak point that causes a cable to break.
From land to water
Working on land is one thing. Add water and waves, and the complexity multiplies.
Currents change with depth, location, and temperature. Wind and waves affect everything – including how a wind turbine moves, and in turn, how the cable moves. Cable design and materials also vary.
By pulling up to 30 metres of cable through an ocean basin, researchers can mimic many of these conditions and collect data. That data is compared to lab tests and fed into computer models that are becoming more and more accurate.
Every cable and ocean site is different, but simulation tools are evolving. Each test generates data that helps refine the design process.
The goal is for the cable design to be done so well from the start that the cables pass all tests with flying colours, without being oversized or unnecessarily expensive.
More content from SINTEF:
-
Testing a giant ship: May take five kilometres to stop
-
A robot is helping researchers hunt for the best cancer warriors
-
Locomotives that run on diesel can be electrified
-
Where kelp is being turned into lab-grown meat
-
Immediate action is a key factor for successful restoration of marine habitats
-
School buildings affect students and teachers