THIS ARTICLE/PRESS RELEASE IS PAID FOR AND PRESENTED BY SINTEF - read more
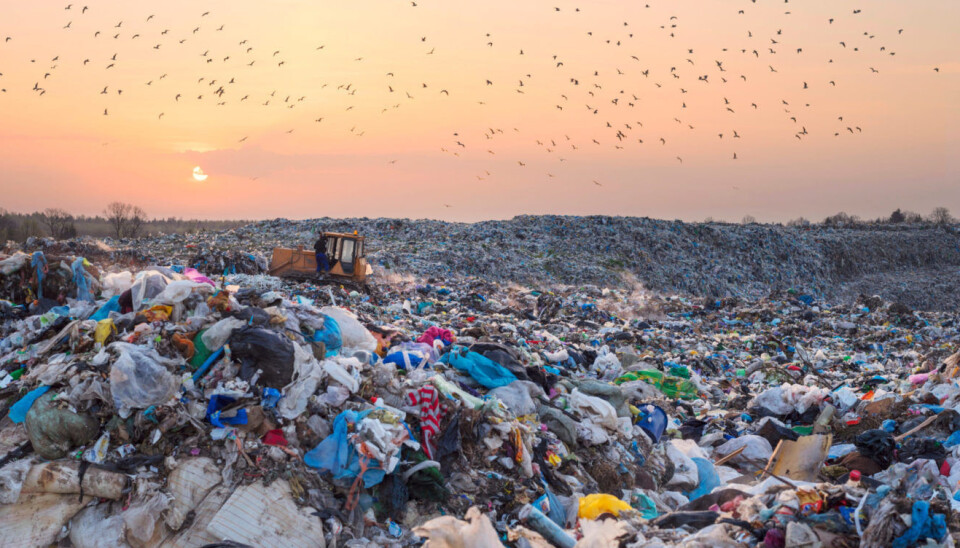
Plastic waste is a resource that doesn’t have to end up in the oceans
Using non-recyclable plastic waste as an alternative to coal may prevent huge volumes of plastic from being discarded into the oceans – and will also reduce CO2 emissions.
Since the 1950s, human beings have generated at least 6.3 billion tonnes of plastic waste. However, only nine per cent of this waste has been recycled and only 12 per cent utilised as fuel. The remaining 79 per cent has been dumped, and much of it has ended up in the oceans.
Most of the plastic that reaches the oceans is non-recyclable and, according to recent studies, even if we continue to develop effective waste collection and recycling systems, there will still be large volumes of plastics that cannot be recycled.
Multiple benefits of local waste management
A pilot project recently completed by SINTEF in Vietnam has concluded that the local incineration of non-recyclable plastic waste as a fuel in cement kilns is a feasible alternative, both on technical and environmental grounds.
The tests carried out to demonstrate that not only are the emissions of the environmental toxins called dioxins not increased if plastic waste is used as a supplementary fuel, but that they also meet the strictest international limiting values for pollutant emissions.
“An approach such as this will significantly boost plastic waste management capacities at local level,” senior research scientist Kåre Helge Karstensen at SINTEF says. “It will also save on large volumes of coal and reduce the volumes of plastics and microplastics being discharged into the East and South China Seas.”
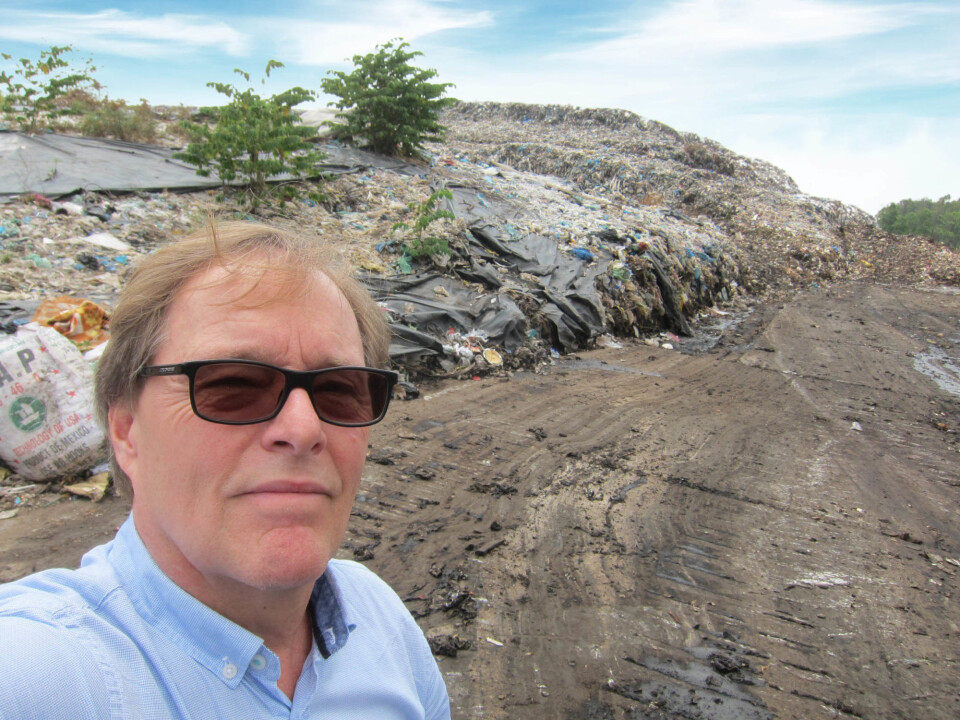
Breaking the cycle
According to international studies, Vietnam is responsible for some of the highest levels of plastic discharge to the world’s oceans. The combination of an elongated coastline, a growing use of plastics, and an inadequate waste management infrastructure all mean that the country discharges between 0.28 and 0.73 million tonnes of plastic waste into the oceans every year.
Lee & Man is the largest paper manufacturer in Vietnam, generating about 150 tonnes of waste every day, most of which is plastic. This waste is regarded as non-recyclable and is currently sent to landfills.
However, the plastic waste dumped in landfill sites will gradually break down and be released into groundwater systems and rivers, providing a continuous source of microplastics to the oceans.
In order to break this cycle, researchers working on the OPTOCE project (Ocean Plastic Turned into an Opportunity in Circular Economy) are conducting a full-scale pilot study. Their aim is to explore the possibility of recovering energy and resources from plastic waste for use in a local cement factory, and in doing so replacing the need to use coal and other raw materials.
“More than 200 tonnes of plastic waste were transported to the cement factory, where they were sun-dried, homogenised and fed into a calcination plant as an alternative fuel,” says Karstensen. “We also tested footwear waste from a local shoe factory."
No increase in emissions
The four-day test involves sampling of emissions by an independent company in order to find out whether the co-processing of plastic waste has a negative impact on emissions, the production process, or product quality.
Co-processing involves the use of waste as a raw material or energy source in industrial processes as a substitute for natural mineral resources and fossil fuels, such as coal.
Gas emissions were analysed at an accredited laboratory for normal emissions to the atmosphere, trace organics such as dioxins, acidic exhaust gases and trace metals.
“All emission measurements were in compliance with existing Vietnamese limiting values. Emissions were not increased, nor were other negative effects identified as a result of co-processing of the plastic waste,” says Karstensen.
A single factory can save a minimum of 10,000 tonnes of coal every year
The first day of the pilot involved a baseline study in which only coal was used as a fuel. During the next three days a mixture of alternative fuel, plastics and coal were fed into the incinerator in varying proportions. On the final day, only plastic waste and coal were used.
A total of 225 tonnes of plastic waste was co-processed during the pilot study in December 2021, saving about 165 tonnes of coal and reducing CO2 emissions by about. 400 tonnes (assuming that the combustion of 1 kg coal produces about 2.42 kg of carbon dioxide).
These results indicate that we can expect the cement factory in Hon Chong alone to incinerate about 17,000 tonnes of paper recycling waste and about 50,000 tonnes of footwear waste annually. This means that from just one factory it will be possible to dispose of about 10,000 tonnes of non-recyclable plastic waste, and save about 10,000 tonnes of coal every year.
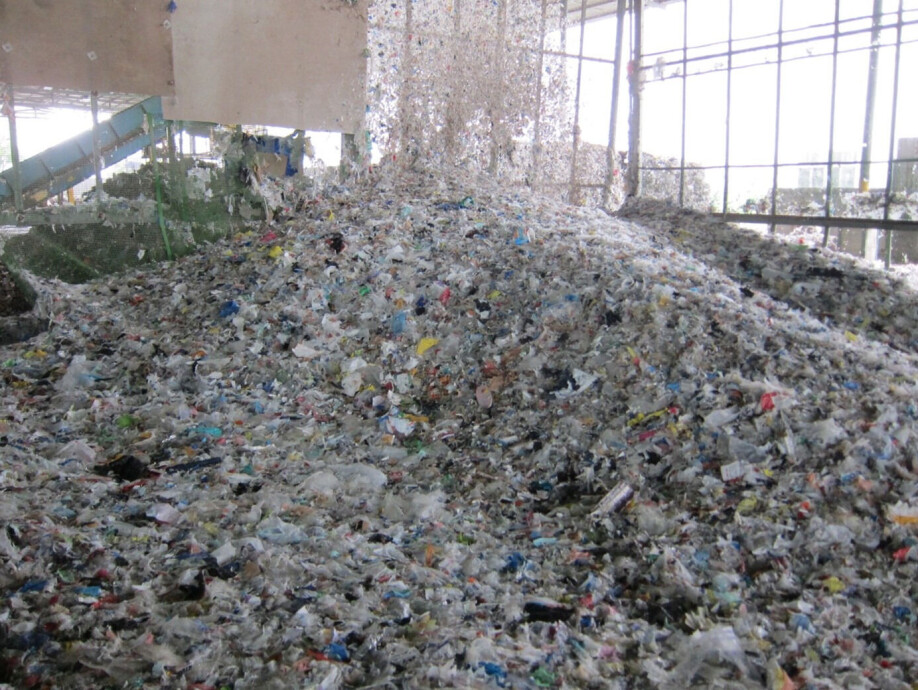
“We’ve been monitoring the project for some time and it clearly demonstrates the enormous potential that Vietnam has to reduce its plastic waste discharge to rivers and the oceans, and to cut its greenhouse gas emissions from energy-intensive industries,” says counsellor Jan W. Grythe at the Norwegian Embassy in Vietnam.
“It is also important, not least because of the country’s ambitious commitments made during COP26 to achieve zero emissions by 2050 and to phase-out coal from the energy mix,” he emphasises.
A win-win opportunity
Sadly, more than five billion tonnes of plastic are currently sitting in landfill and other disposal sites or polluting natural habitats across the world. This is because only a small proportion of our plastics can be recycled and may be because some of the plastic has already been recycled several times, or because it contains additives that make it unsuitable for recycling.
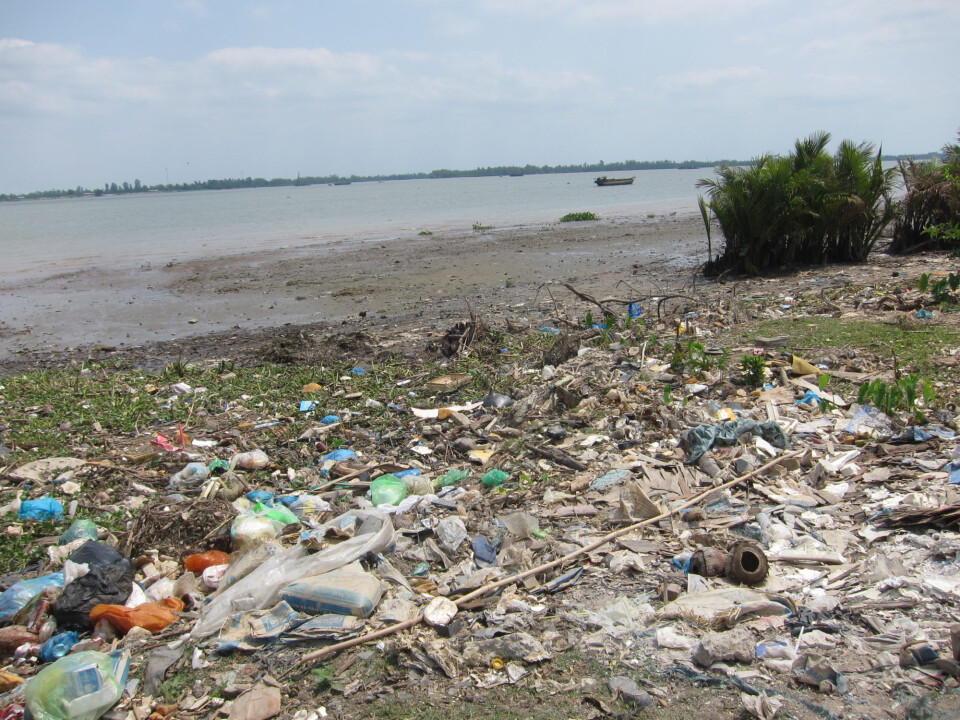
“This non-recyclable plastic waste will gradually break down and be released into our groundwater systems and rivers,” Karstensen says. “In this way, it accumulates and constitutes a continuous supply of microplastics to the oceans for the foreseeable future."
The countries participating in the OPTOCE project have a combined population of three billion people, half of whom live along the coastlines. They produce about 64 million tonnes of plastic waste annually and are among the biggest consumers of plastics in the world. As a result, they exhibit some of the highest levels of discharge to the oceans.
These countries all have one thing in common – inadequate plastic waste management capacities.
On the other hand, they also produce about three quarters of the world’s cement, steel and electrical power, all of which takes place in tens of thousands of plants that burn massive volumes of coal and thus contribute to a major proportion of the world’s CO2 emissions.
“The replacement of some of this coal with non-recyclable plastics offers a win-win opportunity. It will prevent the plastics from ending up in the oceans, reduce the need for large volumes of coal, and will indirectly cut greenhouse gas emissions because there will be less need to construct new incineration plants and open new landfill sites,” Karstersen says.
Cost-effective, resource-effective and the most environmentally friendly
Cement production requires massive volumes of coal and other raw materials. However, all of these components can be substituted, either entirely or in part, by waste that contains energy and/or inorganic components. The substitution process is normally called co-processing.
This approach has been shown to be cost-effective, resource-effective and environmentally friendly when compared to combustion in an incinerator. The energy exploitation efficiency is much higher than in modern incinerators that generate energy from waste. Nor are any residual products generated, compared with about 30 per cent by volume in a traditional incinerator.
As well as waste from paper manufacturing plants, the researchers are looking into the feasibility of exploiting non-recyclable plastics taken from large rivers, landfill sites, industrial plants and cities in local cement factories.
See more content from SINTEF:
-
Testing a giant ship: May take five kilometres to stop
-
A robot is helping researchers hunt for the best cancer warriors
-
Locomotives that run on diesel can be electrified
-
Where kelp is being turned into lab-grown meat
-
Immediate action is a key factor for successful restoration of marine habitats
-
Dynamic cables – the umbilical cord of ocean installations