THIS ARTICLE/PRESS RELEASE IS PAID FOR AND PRESENTED BY SINTEF - read more
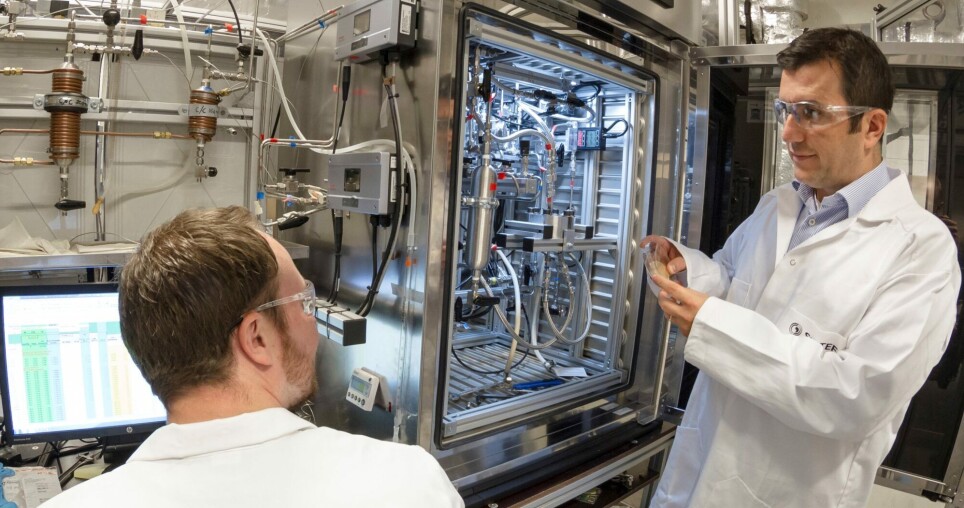
Capturing CO2 from flue gases using a super membrane
As part of a six-year research project, researchers have succeeded in developing a membrane that captures CO2 in an entirely innovative way.
The research idea was born in the SINTEF Industry laboratory in Trondheim.
CO2 separation membranes do not represent a novelty in itself. However, the new membrane separates CO2 faster and much more selectively than those currently on the market – thanks to an entirely innovative approach to membrane fabrication. This means in practice that the membrane is able to separate and concentrate CO2 gas mixtures much more efficient.
The technique involves combining nanotechnology and UV light, and the research team was rewarded with international attention and publishing in the prestigious peer-reviewed periodical Science magazine.
High permability and accuracy rewarded
But what makes this membrane so special?
It’s the combination of working quickly and selectively at the same time. The membrane only allows to pass through exactly what it is supposed to.
The CO2 separation membranes work by allowing CO2 to pass through faster than other gases from flue gases, which always consist of gas mixtures. However, up until now, a recurring dilemma faced by scientists has been how to balance the high permeability requirement of the membrane (Ed. note; its ability to allow gas to pass) with its selectivity, i.e., the concentration of the CO2 in the gas after it has passed through the membrane.
“Normally, high permeability membranes have poor selectivity,” explains SINTEF researcher Marius Sandru. "This means low CO2 concentrations in permeate because other gases are permitted to sneak through – just like a sieve that lets through sand grains that are too big. If, on the other hand, the membrane is not permeable enough, too little CO2 will pass through and, to continue our analogy, we won’t capture the smaller sand grains that we’re looking for,” he says.
This is the problem that the research team has succeeded in solving with the help of a combination of nanotechnology and an inexpensive plastic membrane.
“Our membrane increases selectivity without affecting its efficiency,” explains Sandru.
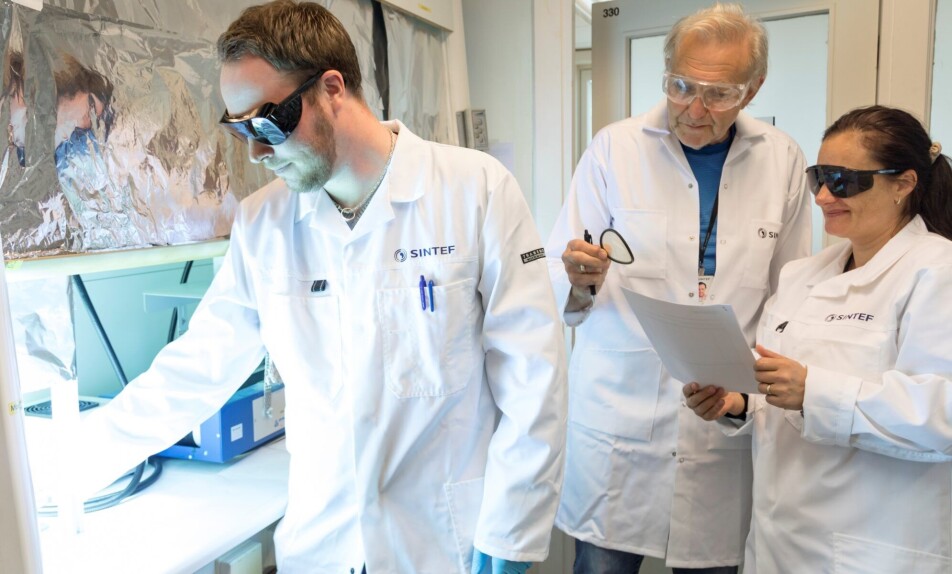
Made of materials found in most homes
“We’ve been basing our research on easily available and inexpensive plastic membranes,” says Sandru. “They are made for example of the same polymer (PDMS) used to make contact lenses, and of another polymer that is similar to Teflon, which we are familiar with from our household saucepans. This is a great advantage when it comes to materials availability."
Moreover, the price of this solution will never be higher than that for membranes that already exist. Membranes that can capture effectively CO2 represent an attractive technology. They occupy little space and can be adapted for use in many applications, from air cleansing in spaceships to the removal of CO2 from biogas, natural gas, and flue gas. Membranes are also easy to replace.
Magic on the surface
However, the standard polymer that Sandru is referring to is only used as a base for the active membrane. The magic happens on the membrane surface, where a new, nanometer-thin polymer layer developed by the research team is located. With the help of its specific chemical structure, the membrane is able to separate and concentrate CO2 from any type of flue gas, especially gas mixtures where the CO2 concentration is very low.
The uppermost layer is integrated with the rest of the membrane as part of a concept called ‘hybrid-integrated membrane technology,’ which has recently attracted international attention for the research team made up of scientists from SINTEF, NTNU and North Carolina State University. SINTEF has secured the patent rights.
Numerous tests and multiple combinations
Multiple combinations of different chemicals, amines and procedures for so-called ‘grafting’ were also tested before the researchers achieved the results they were looking for.
Sandru goes on to explain:
“In this context, the grafting process involves the creation of short polymer chains on the membrane that raise from its surface like nanometer-scale hair strands. These hair strands have reactive groups situated along the polymer chain, such as epoxy groups that bond with amines, which themselves constitute the key active component of the membrane. Amines represent a group of chemicals that are commonly used in a variety of carbon capture technologies because they have the ability to react or bond with acidic gases such as CO2,” he says.
“The grafting process is carried out by supplying energy to the polymer membrane. In this project, we found that the best approach was to use UV irradiation,” explains Per Stenstad, Sandru’s colleague at SINTEF.
Eugenia Sandru goes on to add: “This causes so-called radicals to be formed on the membrane surface. These radicals are highly reactive, and when we add certain monomers (chemical building blocks), they react with the active points causing the ‘hair’ to grow out from the membrane surface."
All this takes place in a closed and controlled environment.
Once the hair strands have captured and concentrated the CO2 with the help of the amines in presence of water vapour, the pressure in the flue gas or vacuum on the other side of the membrane will force the gases across it. In this way the CO2 is separated from the rest of the gases and is ready for sequestration as part of a CCS (Carbon Capture and Sequestration) system, or for re-use in another chemical process (Carbon Capture and Utilisation/CCU).
The researchers have now tested the membrane using a flue gas mixture containing 10 percent CO2 and 90 percent nitrogen. This mixture is representative of flue gases composition produced in many industrial processes that burn fossil fuels. The result was that the membrane succeeded in achieving extremely high CO2 permeability, as well as high CO2 selectivity relative to nitrogen, with values of up to 1000 depending on the test conditions.
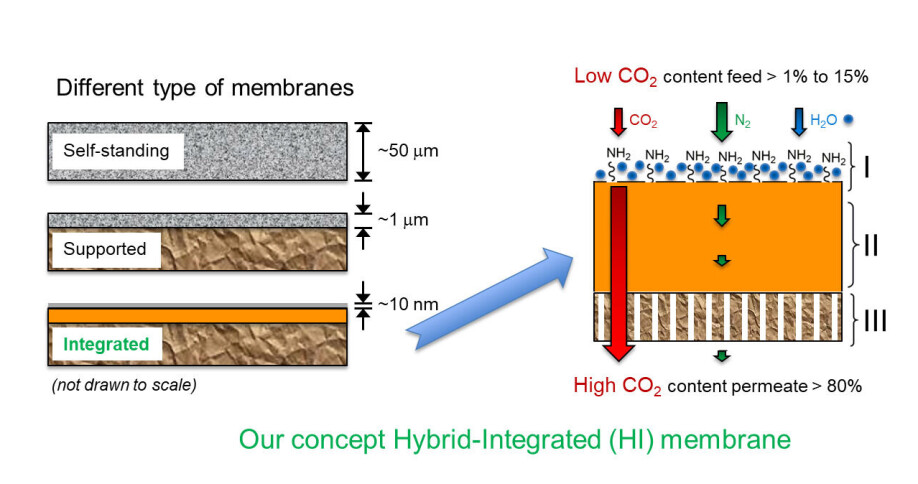
Multiple applications
However, a membrane must also be sufficiently robust to function effectively in industrial settings. For this reason, the researchers have been testing its effectiveness over thousands of hours using a variety of gas pressures, temperatures and water vapour contents. The membrane remained intact and performed well.
“But, of course, it remains to be seen if the membrane is equally robust in industrial settings outside the lab,” says Marius Sandru.
“Can this technology be used to separate gases other than CO2 from exhaust and flue gases?”
“We started by focusing on CO2 capture from flue gas,” says Sandru. “But we’ve also obtained some promising data on removing CO2 from biogas and natural gas and have achieved CO2/methane selectivity of up to 500. We also think that a similar membrane will enable us to separate CO2 from gas mixtures containing hydrogen and given the current interest in hydrogen, this is an idea that we want to pursue. We also envisage other interesting applications, such as the removal of CO2 from fermentation processes, gasification and perhaps also direct CO2 capture from the air,” he says. The project is being funded as part of the Research Council of Norway’s CLIMIT program.
The project is being funded as part of the Research Council of Norway’s CLIMIT programme.
———
Read the Norwegian version of this article on forskning.no
See more content from SINTEF:
-
A robot is helping researchers hunt for the best cancer warriors
-
Locomotives that run on diesel can be electrified
-
Where kelp is being turned into lab-grown meat
-
Immediate action is a key factor for successful restoration of marine habitats
-
Dynamic cables – the umbilical cord of ocean installations
-
School buildings affect students and teachers