THIS ARTICLE/PRESS RELEASE IS PAID FOR AND PRESENTED BY SINTEF - read more
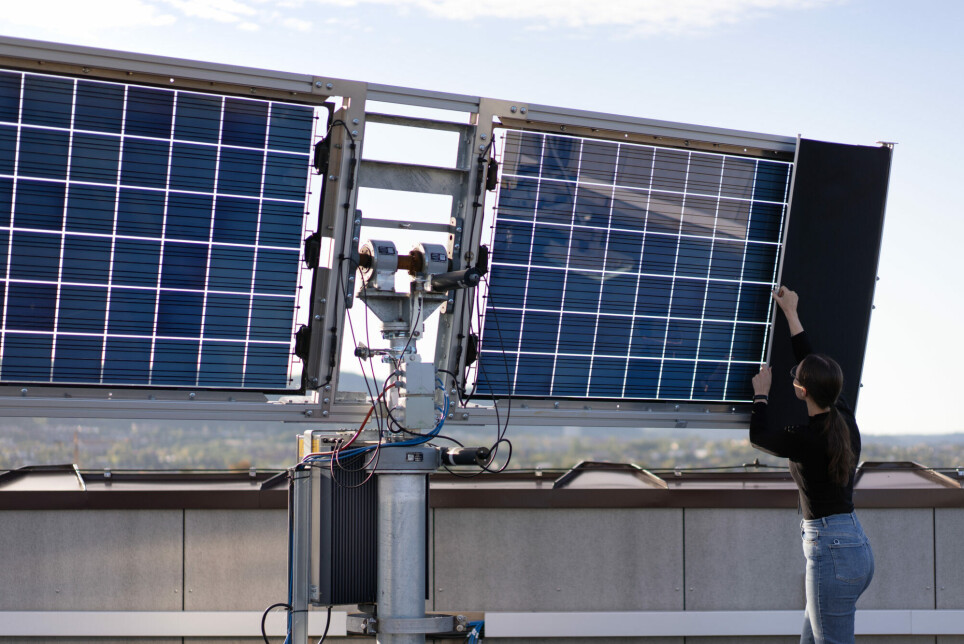
New solar panels from solar panel waste
Solar energy is good news for planet Earth – but solar panels are not as climate-friendly as they should be. Researcher Martin Bellmann is using what he calls the ‘black gold’ waste materials from solar panel manufacture to make new panels.
Solar energy is clean energy. Pure and simple.
But things start to get complicated when it comes to obtaining the raw materials we need to make solar panels. Not only do most of these raw materials come from China, but as much as a third of the material is lost during the manufacturing process.
“But it’s possible to recover this material as part of the production process,” Martin Bellmann says. He is a senior Business Developer at SINTEF Industry and is heading the international EU-funded solar panel project called Icarus.
“And maybe this will enable us to establish a new solar-based industry in Europe,” he says.
Solar panels currently represent 60 per cent of global growth in renewable energy.
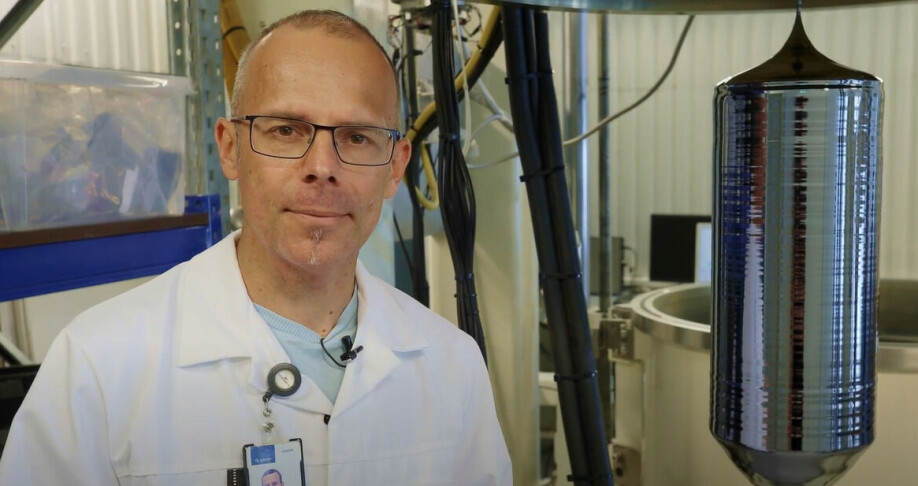
From quartz to crystalline silicon
Bellmann explains how solar panels begin with the mineral quartz, which is used to make super-pure silicon. First, the silicon is melted in a crucible and a silicon crystal, or ingot, is pulled out.
“The ingot forms a kind of cylinder that grows and grows by slowly pulling the silicon from the crucible,” says Bellmann. “It is then cut to form a square-sided block which is sawn into thin slices, or wafers, as we researchers call them."
A typical wafer is just 0.13 millimetres (13 micrometres) thick, and it is these wafers that are used to make solar panels.
But all this sawing results in a great deal of ‘sawdust’ powder. It’s just like sawing a timber plank – some of the timber is lost in the form of sawdust. The same thing happens when you saw through a silicon ingot, even if you use thin diamond wires. Some material will always be lost as ‘silicon powder’.
Sawing wastes 35 per cent
“We lose 35 per cent of the silicon in the form of a black powder,” Bellmann says.
It is this powder, which he calls the new black gold, that the researchers are aiming to exploit.
“Today, we simply throw this powder away. What the Icarus project is doing, first and foremost, is looking into ways to return the powder to the value chain and use it to make silicon crystals and solar panels,” he says.
The powder is collected in a liquid sludge mixture that also contains contaminants from the sawing process such as oxygen, carbon, nickel, iron and aluminium.
“Silicon contaminated by these metals is not good for solar panel manufacture,” Bellman says.
This is why he is working together with Icarus project partners to find ways of decontaminating the silicon powder so that it can be recycled as a raw material for new solar panels.
What we today regard as waste can be used in other products such as electric vehicle batteries. A number of partners are testing different ways of separating silicon from the contaminated mixture.
A Europe-wide project
Naturally, the aim is to better exploit the raw material, which in turn will be good for the environment and the climate. But it is also a stated aim that Europe should achieve greater self-sufficiency.
“The European solar panel sector was once bigger than it is now, but everything has been moved to China,” Bellmann says. “Today, we’re heavily reliant on raw materials from Asia, and silicon is no exception. We’re planning to use the silicon powder to help reduce our dependency on China."
Bellmann is hoping that the Icarus research project will form the basis for a new industry, perhaps also in Norway. Norwegian energy is clean, and this is a major advantage in this context.
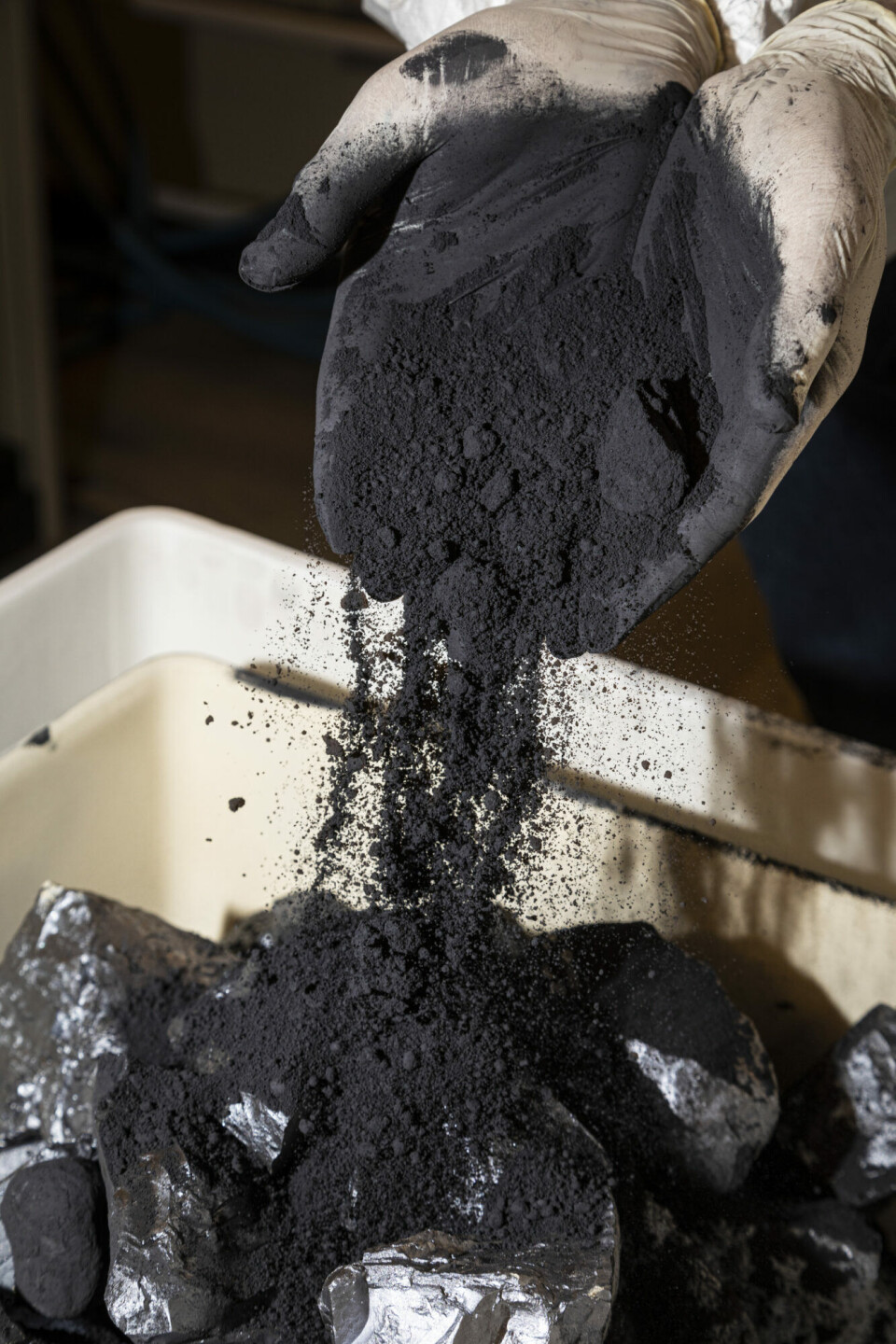
Recycling silicon – and more
A bonus resulting from the Icarus project is that researchers are planning to recycle the quartz crucibles that are used to smelt the silicon before it is pulled into crystals.
“The crucibles fracture when they cool down in the smelting oven. Every time you smelt some quartz you have to get a new crucible and throw the old one away. Our aim is to use this as a raw material for making silicon carbide,” Bellmann says.
Silicon carbide is used in the electronics industry, among others, and electric vehicles are just one of many products that contain the material.
“Normally, we use so-called high-purity quartz to make silicon carbide, but this is very expensive,” Bellmann says. “Our idea is that it might be possible to replace high-purity quartz with crucible waste, which is also in essence quartz of very high purity."
The Icarus project is also looking into recycling graphite waste as a raw material for use in batteries, among others.
“High-purity graphite is also discarded. It is used in the ovens where the silicon crystals are pulled out but has to be replaced from time to time because it loses its properties. The Icarus project is currently working with graphite waste, with the aim of recycling it,” Bellmann says.
See more content from SINTEF:
-
Testing a giant ship: May take five kilometres to stop
-
A robot is helping researchers hunt for the best cancer warriors
-
Locomotives that run on diesel can be electrified
-
Where kelp is being turned into lab-grown meat
-
Immediate action is a key factor for successful restoration of marine habitats
-
Dynamic cables – the umbilical cord of ocean installations