THIS ARTICLE/PRESS RELEASE IS PAID FOR AND PRESENTED BY the Norwegian University of Life Sciences (NMBU) - read more
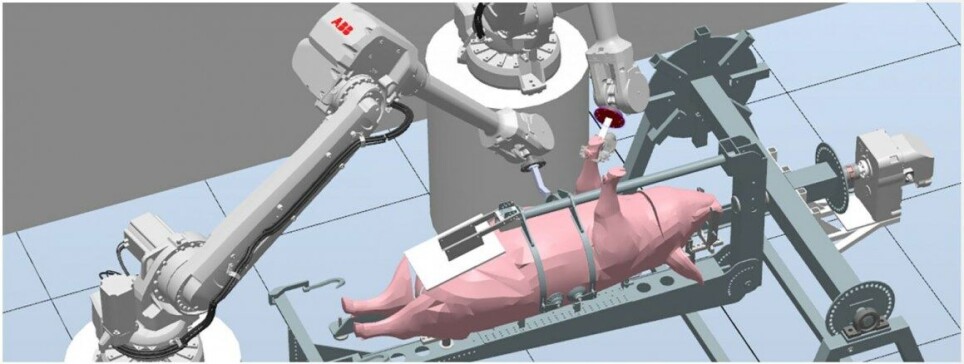
Can a robotic butcher make the meat industry more sustainable?
Can automation make the meat industry more sustainable? The answer is yes if you ask Alex Mason. He is working on developing a butcher robot for pigs.
The goal is that the robot will improve working conditions in the meat industry by reducing the number of dangerous and repetitive tasks. It will also contribute to increased safety and equal treatment for employees, better food hygiene and less waste.
The EU-funded project is called RoBUTCHER and builds on the so-called Meat Factory Cell system. The system differs from traditional slaughterhouses because it uses cells, where several tasks are performed within a cell. This is instead of line production, where different tasks are distributed in stages along a production line.
The goal is to develop an automated cell using robot technology based on artificial intelligence and cognition. In other words: To make an intelligent robot that can learn to lift, hold, and cut the carcass the same way a butcher does.
It's not an easy task, because meat is soft and flexible and so its shape changes when handled. Therefore, meat products are some of the most difficult to understand and handle for robotic systems.
Better working conditions and food hygiene
While there are big differences between countries, there’s room for improvement of working conditions in slaughterhouses to make work safer and less strenuous. The tasks at the slaughter lines are heavy and repetitive, the environment is often cold and noisy, and the work leads to stress injuries and early retirement.
The researchers expect that health and safety at work will be better with automated workstations than they are at the slaughter line.
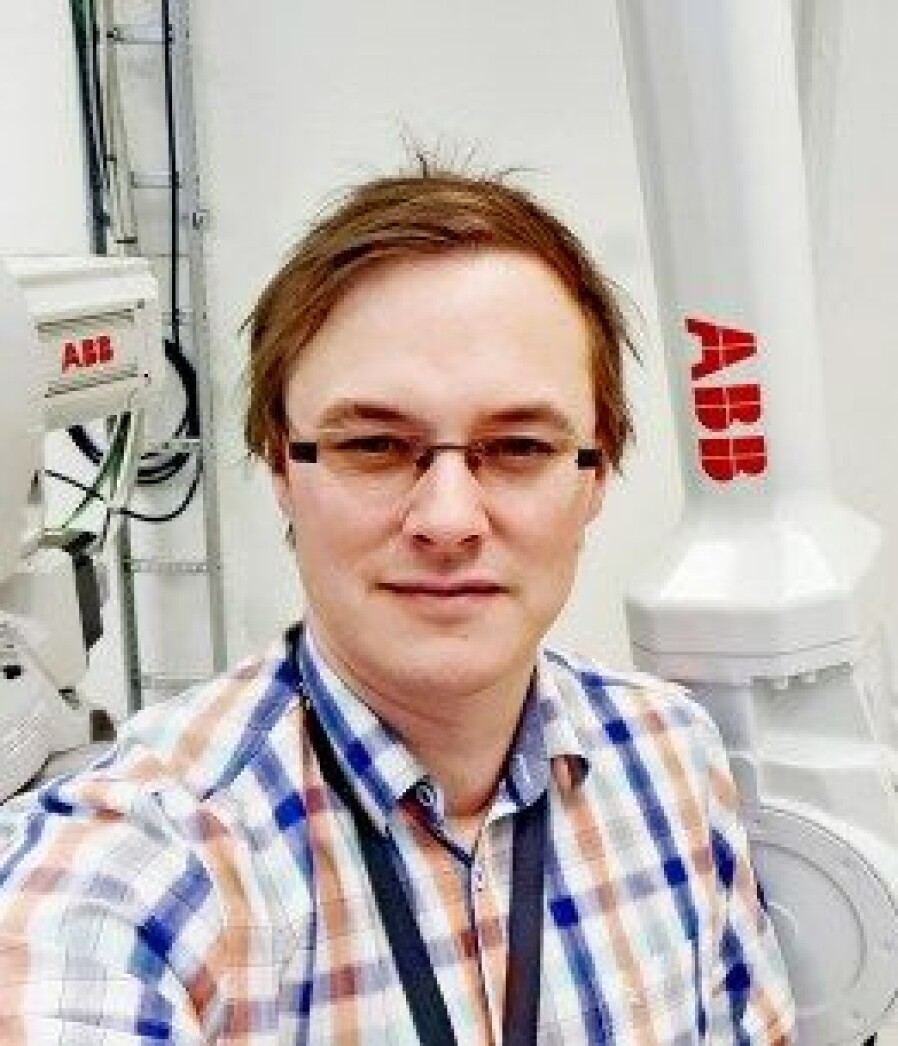
“With a workstation like RoBUTCHER, the robot can do much of the heavy lifting and repetitive tasks, so that the work becomes less physically demanding for the workers,” says Alex Mason.
Robots are more hygienic than people. Since they do not bring infection into the production premises, the use of robots will mean fewer bacteria and less risk of spreading food-borne diseases. In addition, robots will be able to help ensure food production in situations where humans are prevented from doing their job.
Alex Mason believes that the COVID-19 pandemic has shown us just how big the need for automation is in industries that depend on human resources.
“In line production everyone works closely, so disease is easily transmitted. In the event of COVID-19 outbreaks, entire shifts had to be quarantined, and several factories across the globe had to stop production to comply with infection control measures. With automated workstations, outbreaks of infection can be limited,” he explains.
Will require other qualifications from workers
The RoBUTCHER system also turns the slaughter process around. Today, the stomach and intestines are removed from the carcass first, but RoBUTCHER cuts the meat first. This can improve hygiene because the meat is removed before it is exposed to the risk of contamination from the stomach and intestines. This method can also reduce food waste. However, since current legislation for slaughter states that the stomach and intestines must be removed first, the regulations in both Norway and the EU must be changed before the method can be used.
Automation is often met with concerns that robots will replace jobs. That can be true to a certain extent, but not entirely, says Alex Mason. He points out that robots will require other qualifications from workers, such as technical or engineering competence. We will still also need the expertise of butchers, but perhaps in more creative roles to train robots to repeatably produce new products for global markets.
“It’s difficult to recruit to the slaughter lines. With better working conditions there is a greater chance of stable jobs, more equality and the opportunity to stay longer in the job,” he says.
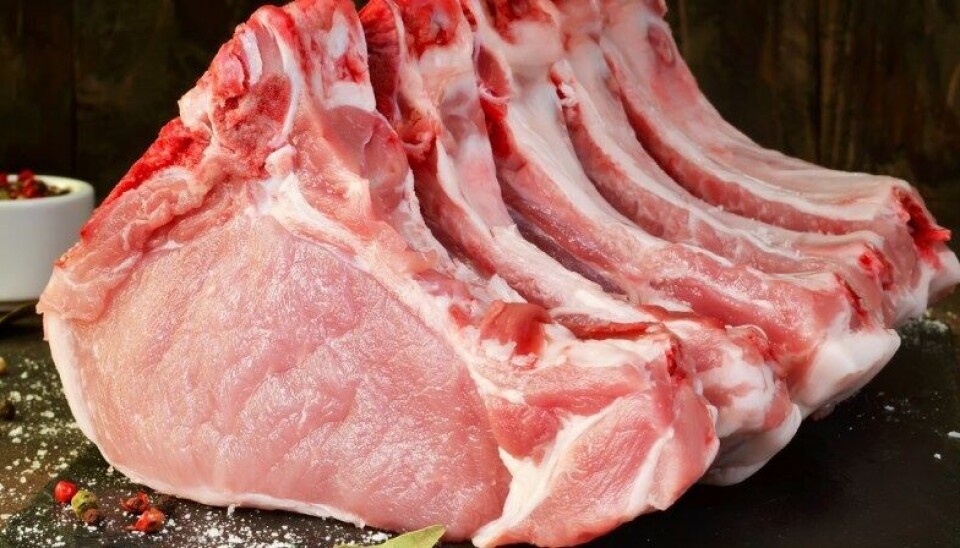
Scalable solution adapted to Norwegian conditions
Automation in the meat sector is not new, but it’s so expensive that it’s only profitable for the largest producers, who often centralise operations around large slaughterhouses.
In Norway, there is still little automation compared with large slaughterhouses abroad. Automation of the traditional production line involves replacing individual steps in the production line with robots. For this investment to pay off, the factories must have a steady and high influx of pigs, around 600 per hour, depending on other factors such as salary.
Even in the largest Norwegian slaughterhouses, the number of pigs is approximately half of this. In addition, salaries are high and production volume varies due to seasonal fluctuations. If it gets too cold, it’s not possible to transport pigs, for instance.
Automation also for smaller slaughterhouses
The researchers behind RoBUTCHER hope that using cells instead of production lines will help solve this challenge. When the number of cells can be adjusted to production level, automation will also be available for smaller slaughterhouses. Say, for example, that a slaughterhouse has invested in two automated cells. If they get fewer pigs for a while, they can choose to have just one cell in operation until production increases again. It also makes it easier to scale the business up if production increases over time by investing in more cells.
“The goal is to create a system that is robust, flexible and scalable, regardless of production volume,” says Alex Mason.
He believes that RoBUTCHER can be an alternative to today's centralized meat production because it can make automation profitable for smaller slaughterhouses.
“There are many advantages to the old way of producing meat – with several smaller farms that deliver to one, small slaughterhouse. It offers more local, short-distance production, less transport and perhaps also better animal welfare. It spreads jobs and it spreads the carbon footprint,” he explains.
See more content from NMBU:
-
Do young people with immigrant parents have better health?
-
Who’s picking your strawberries this summer?
-
Can coffee grounds and eggshells be turned into fuel?
-
Rising housing costs fuel inequality in Norway
-
Researchers warn: Climate change in African mountains has a greater impact than previously thought
-
Algae turns wastewater into resources