An article from Norwegian SciTech News at SINTEF
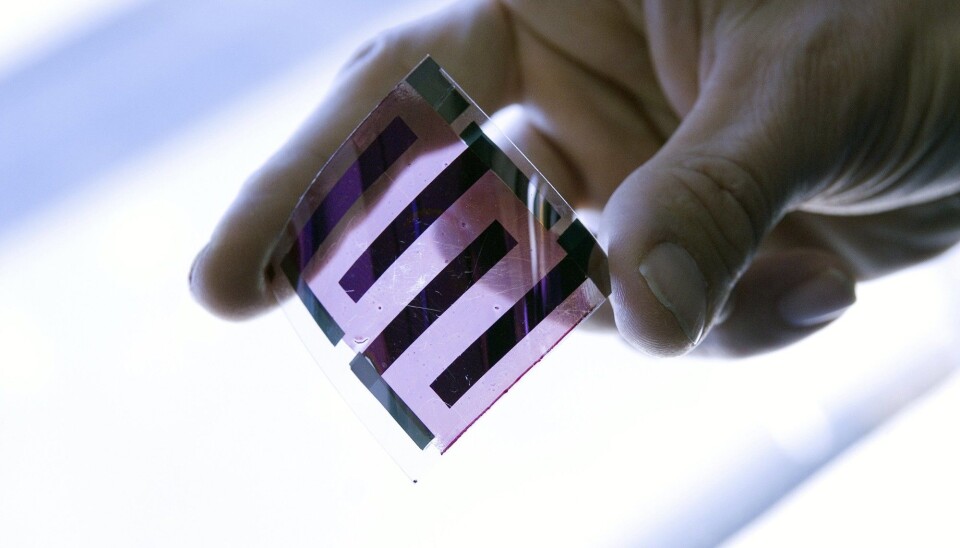
Plastic solar cells see the light of day
In the future, you may be able to buy solar cells for your roof from a roll, by the metre.
Denne artikkelen er over ti år gammel og kan inneholde utdatert informasjon.
You may also be able to put on leisure-wear with a plastic coating that charges your mobile phone with solar energy while you are on the hills.
According to SINTEF scientist Espen Sagvolden, these are perfectly possible scenarios for everyday life in the future. For the first plastic-based solar cells are already in production. According to Sagvolden, they represent a technology which initially can bring solar energy into new areas of utilisation, and eventually can lower the price of photovoltaics. However, these early versions are not very efficient compared to current solar cells made of silicon.
With the aid of numerical models that simulate materials at atomic level, Sagvolden is on the hunt for the building blocks of materials that will be able to utilise sunlight more efficiently.
Niche markets
“If plastic turns out to have a future in the solar power market, the world will get cheap, thin and flexible solar cells. However, the first versions have a lifetime of only two or three years, so it will probably be some time until plastic solar cells appear on our roofs,” says Sagvolden.
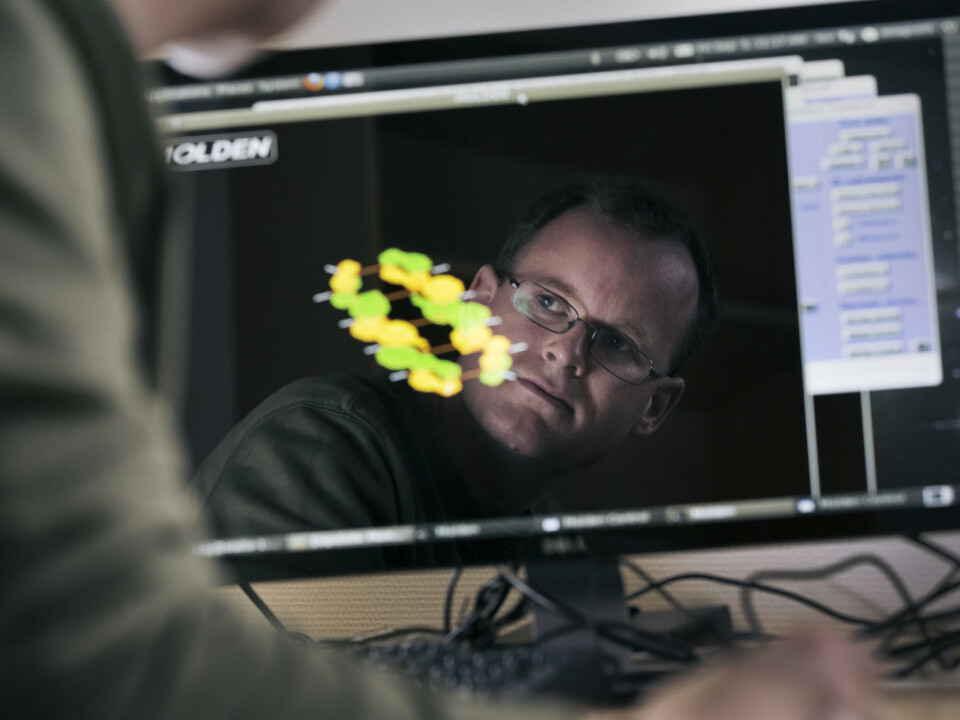
On the other hand, he expects that they could quite soon be incorporated into tent fabrics and leisure-wear. Meanwhile, several companies are working on integrating semi-transparent plastic solar cells into house and car windows.
“Applications are limited only by our imagination, if they make their breakthrough. We may not have to wait so very long for them to offer us living images on posters, in addition to current to run other devices that have a short life-cycle. In fact, the single-use solar cell may be just round the corner.
Conductive plastic
The investigations being led by Sagvolden are part of an international technology race that is under way in the field of plastic solar cells.
Depending on how they are produced, currently available silicon-based solar cells utilise some 16 – 20 percent of the energy in the sun’s rays, while the first generation of plastic solar cells have an efficiency of only 10 percent. This means that if you wanted to use these early versions to generate a given amount of electric power, you would have to cover a larger area of your roof than if you used silicon cells.
Ordinary plastics don’t conduct electricity. But there are also conductive plastic materials.
Round each and every atomic nucleus in all molecules is a cloud of electrons. For molecules to be conductive, the electron clouds need to overlap – and the electrons must not be strongly bound to any individual molecule. These conditions are not met in ordinary plastics, but they are in conductive plastics, where the electron clouds are so large that they overlap each other more than enough.
Pioneers broke their necks
The first pioneering companies in plastic solar cell technology have been active for several years, and an American company has already gone so far as to attempt commercial production. It went bankrupt.
Sagvolden explains that the idea of plastic solar cells has valuable positive aspects, but that the first versions suffer from a number of weaknesses.
His “balance sheet” looks as follows:
Pluses:
Low manufacturing costs expected: The plastic materials in use today are not cheap, but with mass production, their prices are likely to fall. Moreover, we need only a very thin layer of plastic material. The German company Heliatek, which is currently building a factory for mass production of solar cells in a plastic-like material, reports that it can come down to a thickness of only half a micrometre – 0.5 thousandths of a millimetre – which would mean as little as one gram of material per square metre.
Maintain efficiency: Silicon-based solar cells lose efficiency when they heat up and when light levels are low. Plastic solar cells are better at staying efficient.
Minuses:
Short lifetime. The manufacturers of today’s silicon-based solar cells guarantee a useful life of at least 20 years. The first plastic solar cells only last for two to three years because the oxygen in the atmosphere degrades them when they are exposed to ultraviolet radiation.
Sagvolden points out that plastic solar cells need to be encapsulated to survive.
“Without a protective covering, they will last only a few days. We hope that improvements in production technology and encapsulation will lead to gradual improvements in useful life. Glass is one promising material that is currently being trialled. The problem of useful life will have to be solved, because it is unlikely that electricity consumers in high-cost countries will want to have installers on their roofs replacing solar cells every three years.”
Livelier cells
Sagvolden says that there is a great deal of room for improvements in the energy efficiency of plastic solar cells. The theoretical limit of efficiency of solar cells laid in a single layer is more than 30 percent. But even though energy efficiency is precisely what he is studying, he emphasises that it is still too early to predict how efficient plastic solar cells will be in practice.
“Only time will tell what will be possible,” says Sagvolden.