THIS ARTICLE/PRESS RELEASE IS PAID FOR AND PRESENTED BY Nofima The Norwegian Institute of Food, Fisheries and Aquaculture Research - read more
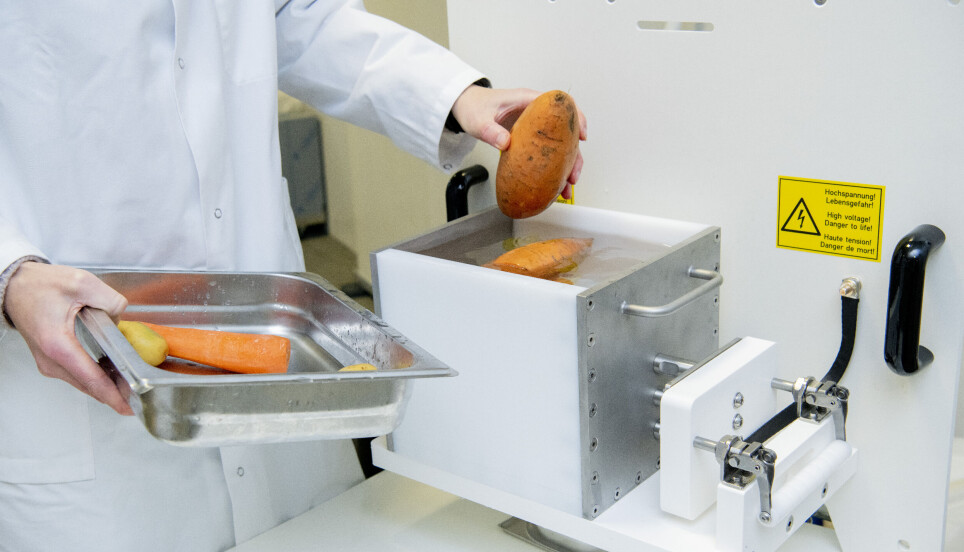
High pressure, ultrasound and UV light can keep food fresh and tasty for much longer
If we are to slow down climate change, food production must be made more sustainable.
One third of man-made global greenhouse gas emissions are due to food production. However, everyone needs food, and it is therefore urgent that we find new ways of producing food that have less of an impact on the environment whilst also being profitable for the producer.
Additionally, we know that food should be processed as quickly and as gently as possible to preserve quality and nutrition.
Fast, gentle and energy-saving ways of producing and preserving food have been the focus of the four-year international research project iNOBox. The project investigates six innovative processing technologies: high pressure, microwaves, pulsed electric fields, ultrasound, UV light and plasma-activated water.
Scientists, food manufacturers and equipment suppliers have collaborated in order to document the effects these technologies have on food and food production.
Increase shelf life to reduce food waste
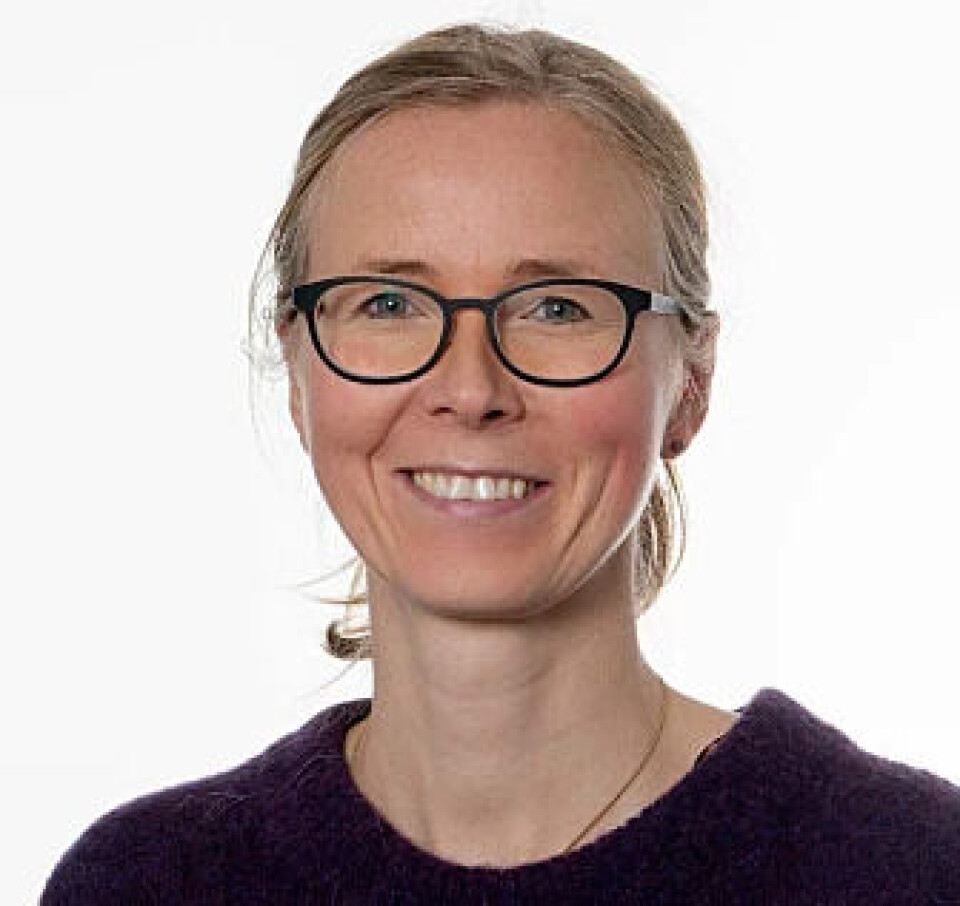
One of the most important ways to save the environment is to stop throwing food away. In Norway, we throw away over 450,000 tons of food every year, often because it has passed its expiry date.
“We know that there are major differences between different raw materials and products when it comes to environmental emissions. Despite the fact that fruits and vegetables produce low levels of emissions, these foods have a short shelf life. Therefore, it is really important to give them a longer shelf life and avoid having them end up in the rubbish,” project manager Tone Mari Rode says.
How sustainable is food processing?
When sustainability is calculated, greenhouse gas emissions and shelf life are often studied. However, emissions associated with things such as the production of equipment and transportation must also be taken into account.
In order to get the whole picture and have the opportunity to compare products, scientists use ‘life cycle assessments’ – a systematic review of the environmental impact in all processes related to the type of food, from when the seed is sown in the soil or an animal is bred, all the way up until the food is consumed.
Norsus has investigated a number of products using this method in order to find out the role that food processing itself plays in the emission accounts. Among other things, they compared the CO2 emissions produced by a smoothie, a sandwich and a beef dish.
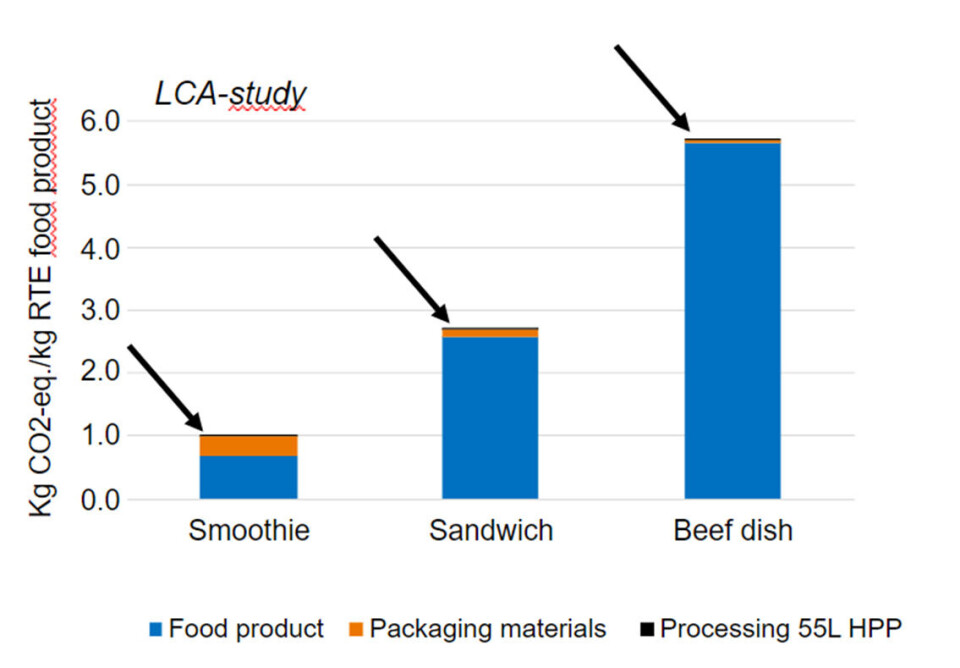
The studies show that emissions from most processing technologies make up only a very small part of the entire life cycle accounts of the food product.
“If processing can extend the shelf life of a product, it can reduce the environmental impact of the product, but only if the benefit of this is greater than the environmental impact associated with the processing," Rode says.
Life cycle assessments are complex analyses in which many factors come into play. Studies carried out by Norsus in this project have provided information on energy savings, reduction of food waste, increased shelf life and working conditions.
Processing to improve food
Many consumers are sceptical about raw materials undergoing treatment in order to improve them. Many believe that the least amount of processing is the best, but this is not always the case.
For example, some people who suffer from allergies can eat nuts that have been treated with heat, but not raw. The allergens associated with allergies are destroyed when the nuts are roasted, while other proteins are not affected.
Can processing with the use of new technologies remove specific proteins from foods that cause allergic reactions?
These types of analyses have been carried out by the Norwegian Veterinary Institute and the Dutch partner TNO. They have investigated the extent to which the new processing technologies can remove specific proteins that can cause allergic reactions.
Unfortunately, people who are allergic to eggs are going to be disappointed – the egg analyses showed no differences between raw and processed eggs in terms of allergenic proteins.
Processing can affect the body’s ability to absorb nutrients from food. Nofima has simulated digestion in the laboratory, and specifically investigated the protein digestion of foods that have been processed using the new technologies.
The results showed that treatment with the different technologies does not affect the protein digestion of any of the foods, except in a ‘smart yoghurt’ – a yoghurt that was made using combinations of technologies. The protein digestion was better in this yoghurt than in traditional processing.
Great potential for sustainable processing
As new technologies become available, it may take time for them to become known and adopted. In the food industry, there are several factors that determine whether a technology is interesting to invest in.
Firstly, it must be known and accessible, and interesting to use as part of or a replacement for processes that are already in use. It must also be an affordable investment, and if the technology is to improve a product, the customer must feel that the new changes in the product are for the better.
Food products that have never been made before, or that have been made in new ways, must have EU ‘novel food’ approval in order to enter the European food market.
A similar ‘new food’ regulation can be found in Norway that has common rules and approvals with the EU. Previously, this has entailed a long and demanding process for food manufacturers, but has now been revised and made somewhat smoother.
Nofima has studied these regulations and encourages food manufacturers to seek help from the Norwegian Food Safety Authority and other producers. Nofima’s research shows that transparency between manufacturers is important for the industry to succeed when it comes to innovations.
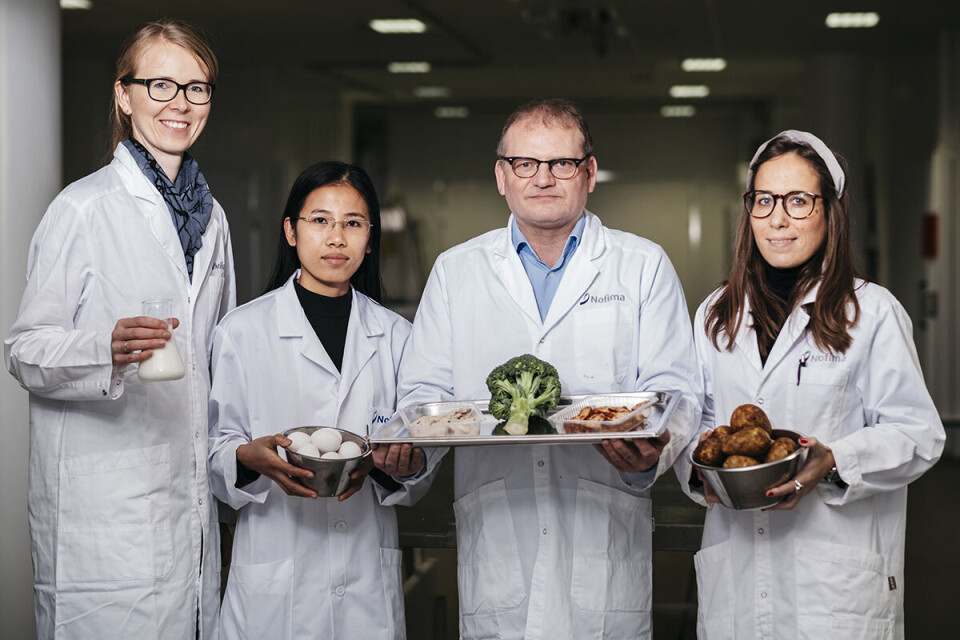
The extent to which consumers accept food that has been made in new ways, or brand new products, is another possible obstacle that stands in the way of adopting new technologies. It is not uncommon to be sceptical of something you know little about.
Nofima has therefore conducted extensive consumer studies that have resulted in a practical tool for marketing communication. It enables manufacturers to see what kind of information is most beneficial to use when the product is made using the various processing technologies.
“The extensive studies we have conducted in this project show that new technologies have great potential to contribute to more sustainable food production,” Rode says. “That is why we continue to work on new projects. A lot of development and documentation remains, but there are many different possibilities that lie in these technologies. We hope Norwegian food manufacturers will use the information we have posted online, and get in touch if they want to test the technologies. We food scientists would very much like to contribute to ensuring that food production takes place in partnership with both people and the environment."
Knowledge about processing technologies available online
The strong wish for the research results to be used is the reason why the scientists in this project have put a lot of effort into an online tool specially designed for Norwegian food manufacturers. Useful information and documentation from the project are gathered in one place.
“In order to make more safe, healthy and sustainable food, food manufacturers are dependant on production methods being efficient, profitable and sustainable. In addition, the products must maintain at least the same high quality as today’s products. We want to help them assess new technologies, and have therefore made the information and documentation from the research readily available,” Rode says.
The website provides the food industry with knowledge about the six new processing technologies, how they work, what possibilities lie in them, and examples of the types of products they are suitable for.
The information can be found in both Norwegian and English, and simple animated films have been made that explain what happens when food undergoes treatment using the different technologies.
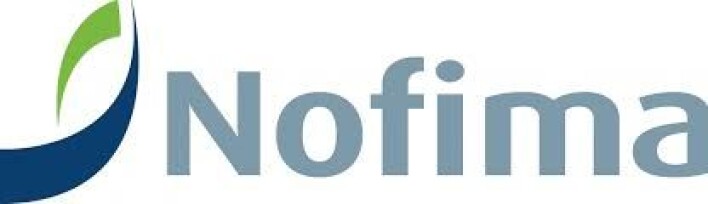
This article/press release is paid for and presented by Nofima The Norwegian Institute of Food, Fisheries and Aquaculture Research
This content is created by Nofima's communication staff, who use this platform to communicate science and share results from research with the public. Nofima is one of more than 80 owners of ScienceNorway.no. Read more here.
See more content from Nofima:
-
Researchers make healthy salmon feed from polluting CO₂
-
Researchers have found the cause of kidney stones in rainbow trout
-
Salmon have 48 hours to defeat sea lice
-
Consumers are less likely to recycle if they need to separate the packaging materials
-
This is what stress does to the colour of salmon
-
This could make it easier to produce safe and juicy fish cakes