An article from Norwegian SciTech News at SINTEF
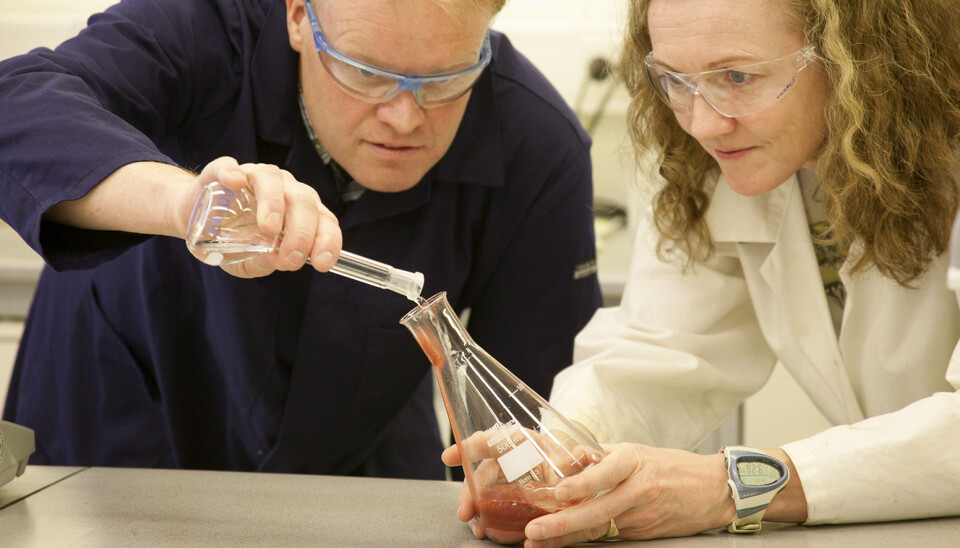
Recipe for more environmentally friendly batteries
Scientists want to develop greener and more vigorous batteries, using inexpensive raw materials that are plentiful in Norway.
Denne artikkelen er over ti år gammel og kan inneholde utdatert informasjon.
A new generation of rechargeable batteries has entered our everyday lives. Lithium-ion (Li-ion) batteries are found in our mobile phones, e-readers and laptops, and supply power to currently available electric cars.
The advantages of these batteries are that they are light weight, and that they can be charged both rapidly and many times, while they ensure that our mobile devices and electric vehicles can do a lot of work before they need to be recharged.
Li-ion batteries are found in millions of pieces of equipment. But several research programmes are simultaneously racing to develop them further. One of these races is about eliminating the expensive, toxic and environmentally hazardous elements cobalt and nickel from today’s batteries. A research group based in Trondheim has joined this race.
Battery principles for the layman
SINTEF’s Tommy Mokkelbost and Fride Vullum-Bruer of NTNU are part of the Trondheim team, and have long since learnt to communicate with the layman via imagery. They are well aware that many people remember little from physics class about how batteries work.
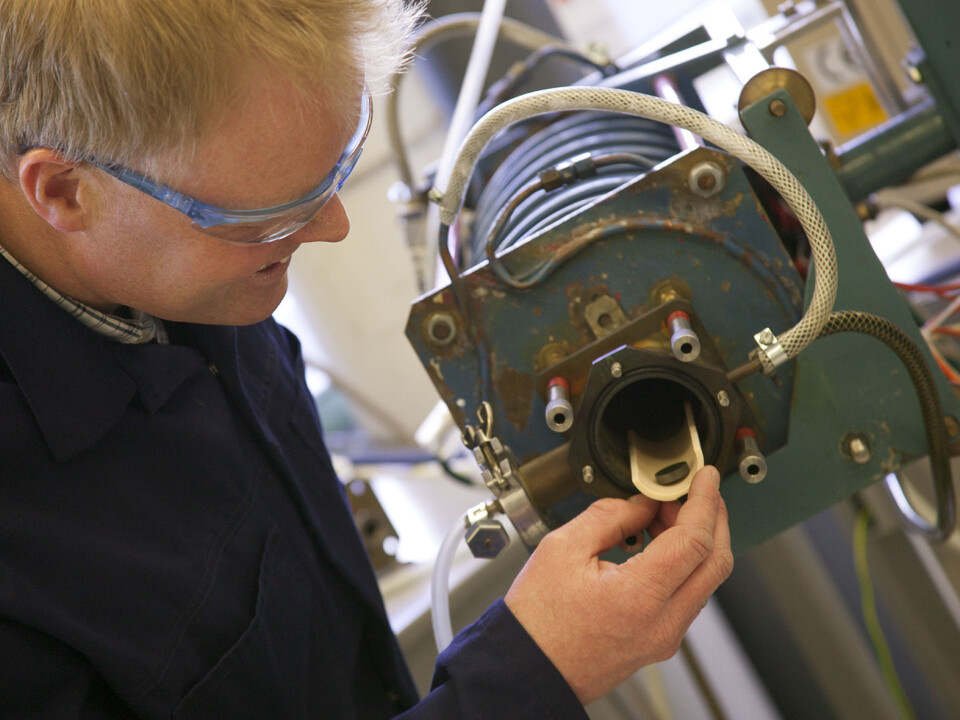
The two scientists recommend us to visualise a battery’s electrodes (the anode and cathode) as two buckets of water, with one of them placed on the floor. This is the cathode. The other, the anode, is placed on a table.
“Buckets of water can be regarded as energy storage sites, just like batteries, so the comparison is valid,” say the two scientists.
More “water” on the table
When our mobile phone or electric car is connected to the charger, “water” is lifted from the lower bucket to the elevated one. (See illustration)
When you make a call or start the car the process is reversed. Imagine that the water streams out of a hole in the bucket on the table and turns a turbine – which provides the phone or car with electric power – before it ends up back in the bucket on the floor.
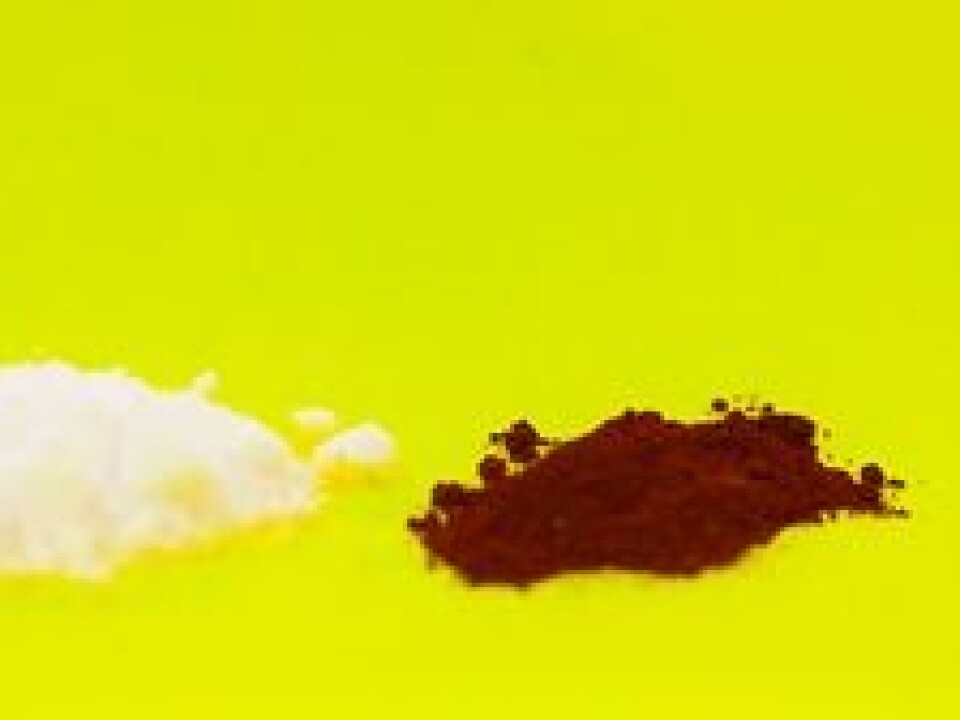
The more water the upper bucket holds, the greater is the equivalent capacity of the battery. And the higher the battery capacity under otherwise identical conditions, the more work the battery can do between each charge.
“Several of the industrial and research groups that are trying to improve the state of Li-ion batteries are concentrating on creating more room in the upper bucket,” explains Mokkelbost. Meanwhile, he and the rest of his research group are focusing on the other end of the process.
“We are trying instead to get more water out of the lower bucket. This is also important, because if no-one manages to do this, battery capacity will always be more or less the same as it is now.
Migrating particles
As the name suggests, lithium plays a central role in Li-ion batteries. It is part of the cathode material, in which it is combined with several other elements. When the battery is charged, Li atoms are “kicked out of” the cathode, at the same time as each atom gives off a negative sub-atomic particle; an electron. What is left of the atom is a positively charged particle known as an ion.
The ions and the liberated electrons both head for the anode, each by a different route. The ions migrate to the anode via the electrolyte, while the released electrons are “pushed” through an external conductive wire or cable. The ions and electrons are re-united in the anode, where they are stored until we use the battery. This once again releases the electron, which moves back through the external wire, creating an electric current. Meanwhile, the lithium ions return via the battery.
This brings the lithium back to the starting point, where it remains, bound to the other components of the cathode, until the battery is re-charged. These materials include the expensive and environmentally toxic elements nickel and cobalt, which form the backdrop to the SINTEF/NTNU project.
Three things at once
The Trondheim-based research group will investigate how both new cathode materials and new ways of producing cathodes affect the properties of the battery.
“If we manage to do everything that we hope, the results will be like a Kinder Egg,” says NTNU associate professor Fride Vullum-Bruer
Like several other research groups elsewhere in the world, the project group will make cathodes in which the lithium ions are bound to a mixture of iron, manganese, silicon and oxygen to form silicates. The ambition of the project is to make progress in three areas simultaneously.
Firstly – greener batteries
- The make-up of the cathode material will be greener, in that cobalt and nickel will be replaced by more environmentally friendly elements.
- The Trondheim-based group also wishes to develop a more environmentally friendly production method for the cathode material, which they hope to do by using water-based solutions rather than the toxic and environmentally unfriendly solvents currently used.
Secondly – longer lasting batteries
- The group hopes that the new composition of the cathode material will allow more lithium ions to be liberated from the cathode.
- There is plenty of room in the anode for more of these ions.
- So if it is possible to transport more ions from the cathode to the anode, the capacity of the battery will increase.
Thirdly – use of cheaper raw materials
One of the main lines of the project is to make the cathode material from less expensive raw materials that are readily available in Norway. The plan includes the use of:
- Silica dust: a by-product that is “scrubbed” out of the exhaust gases of silicon and ferrosilicon plants. It is used as an additive in cement production.
- Iron (ferric) oxide: a product of the Norwegian mining industry. One of its uses is as a paint pigment.
Norwegian niche
Mokkelbost and Vullum-Bruer are well aware that scientists in several countries are attempting to develop cathode materials from exactly the same elements as they want to study.
While many of their competitors are counting on high-purity raw materials; i.e. expensive ingredients, the Trondheim-based research group has decided to investigate a different, more reasonably priced, alternative.
They intend to obtain partially purified raw materials from the industrial processes where they are created. But then, any contaminants will be transferred to the battery. “Won’t that affect battery performance?”
Mokkelbost: “It’s bound to have an effect, but we don’t yet know how serious it will be. What we are hoping to do is to develop reasonably priced raw materials that manage to give batteries a much higher performance level than current lithium-ion batteries.”
“But no-one manufactures batteries here in Norway. How will this country benefit if you succeed?”
“First and foremost, it will give us the possibility of becoming a supplier of materials for future batteries. We are talking about huge markets here, particularly with respect to the current developments in electric vehicles.”
Faster charging
The results that have already been obtained by research groups all over the world, not to mention in Trondheim, have also ignited a hope that it will be possible to charge future Li-ion batteries more rapidly than those currently available.
This is in spite of the fact that the new materials have poor conductivity, just like current cathode materials. Neither ions nor electrons are able to move rapidly in them.
Vullum-Bruer: “The challenge is just the same as when the public are leaving a packed football stadium. “If we push the ions in order to get them out faster, they just bump into each other.” The Norwegian research group and many of its partners and competitors have attacked this problem using nanotechnology.
“This has enabled us to divide the cathode material up into a large number of small football pitches instead, with the result that we can force the ions out much faster.”
Vullum-Bruer explains that the Trondheim-based group has obtained promising results on a laboratory scale in this area.
“However, it is one thing to succeed at the lab-bench. The next challenge will be to find methods that are also cost-effective on an industrial scale.”
------------------
Read the Norwegian version of this article at gemini.no