THIS ARTICLE/PRESS RELEASE IS PAID FOR AND PRESENTED BY SINTEF - read more
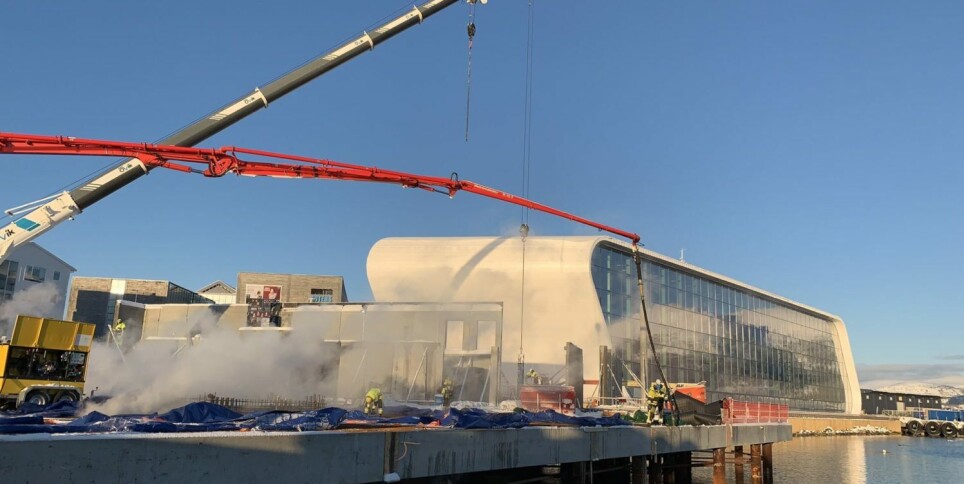
Now construction projects can heat themselves
What if a concrete building could heat itself – while being built? Research scientists are about to make this dream a reality.
A new product based on concrete slab elements with built-in, liquid-filled heating pipes makes construction projects able to heat themselves. The source of the heat is fossil-fuel free energy, making this a green concept.
This means that heat is also supplied during the building process, which turns out to be a positive side effect. They replace other temporary heating systems and can function throughout the lifetime of the building.
The product has been developed in collaboration between research scientists from SINTEF and the Norwegian contractor Betong & Entreprenør AS.
No fossil fuel
Originally, the energy for the heating pipes was to be supplied by high-efficiency, diesel-powered industrial heating systems. However, new national regulations in force from January 2022 ban fossil-fuel based fuel systems in buildings under construction.
“We have assessed green heat sources and found that the system can potentially be combined with heating systems powered by biodiesel, hydrogen and ammonia, as well as electric systems such as heat pumps, and district heating,” says Betong & Entreprenor’s project manager, Tommy Holan.
HeatWork in Narvik, a supplier of high-efficiency diesel-powered heating, has taken this seriously. They’ve developed a substation for district heating systems. The project is now ready to be tested when an opportunity arises. The same applies to their electric mobile heating plant, which will be ready for launching in the autumn of 2022.
All that remains is for the project owner to arrange supplies of electricity and district heat to the site from the outset.
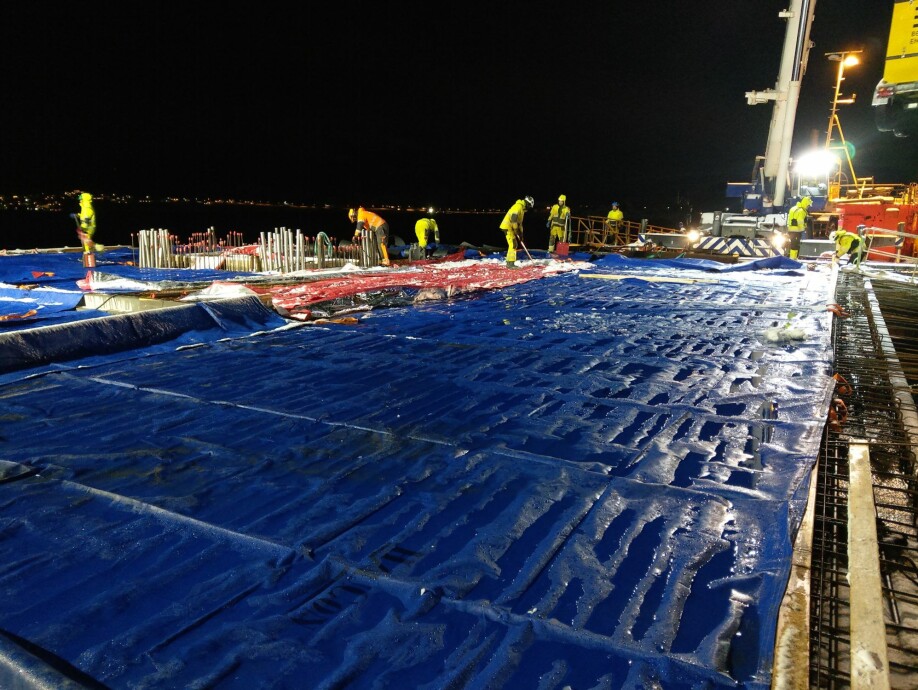
Improving the quality of concrete
Used as intended, the new system raises the quality of concrete and reduces curing time. Studying and using this concept makes progress towards a sustainable future for concrete casting in Arctic climates more straightforward.
This spring, Norwegian company PEAB Bjørn Bygg AS demonstrated the concept at a quay construction project belonging to Hotel Richard With in Stokmarknes.
“We are very pleased with the process and the result after completing the construction of the quay’s deck. The method has demonstrated clear gains with regard to quality control and the progress of the project. The potential of this method for winter work on concrete structures is clearly enormous,” says Tore H. Strand, Production Manager at PEAB Bjørn Bygg.
“The fact that the precast pipes can be used as a basis for heating and drying in the subsequent building process is a clear time-saver and results in a tidier building site with less need for such things as cables and heaters. A large part of the rigging work will also be completed in an early phase of the project,” says Strand.
The system, named ‘VIP’, which stands for ‘Væskebåren varme i prefabrikkerte betongelement’ (liquid-borne heat in prefabricated concrete elements), can also be useful in regions where high temperatures are a problem, since it can also transport cool liquid.
Large-scale production test led to important discoveries
The first large-scale production test was carried out in co-operation with PEAB Bjørn Bygg in Stokmarknes in January, with the successful casting of a quay and base slab at Hotel Richard With.
The constructed pipe circuits were stretched to the limit and the conditions were windy. The temperature was around 0 °C, and there was about five centimetres of snowfall the night before casting.
The test resulted in several very positive experiences:
- The system thawed out snow and ice and ensured effective preheating of the elements before fresh concrete was cast.
- The liquid-borne heat, in combination with traditional good work skills, contributed to effective curing of the concrete. This resulted in a crack-free surface and rapid strength development, enabling walking on the surface the following morning.
- Large amounts of data were collected by logging liquid and curing temperatures, diesel consumption, climatic conditions and flow and pressure in the pipe circuits. This was analysed in detail and will result in recommendations for improvement in future designs.
- It was confirmed that the system needed to be improved to enable individual flow control in all circuits, thereby allowing circuits of different lengths in the same system. Thus the number of pipes can be reduced while achieving optimal use of the heat source.
- The test of the VIP elements confirmed that the system is twice as efficient as when a corresponding amount of liquid-borne heating is located on the surface, which is currently by far the best solution the industry has at its disposal.
Potential for development
VIP elements can result in energy-efficient temperature control during the casting of concrete elements. The system is not limited to particular heat sources, the liquid can therefore be heated using available green fuel systems.
“Our objective is clearly to be in the forefront of the green transition, and VIP elements are a very potent tool when we and our clients need to use low-carbon concrete at building sites in the future. Low-carbon concrete, also known as low-heat concrete, is particularly sensitive to our low-temperature conditions,” says Trygve Nilsen, Managing Director of Norwegian company Betong & Entreprenør AS.
“What other system can supply energy-efficient heat to this environmentally friendly concrete?” he asks, rhetorically.
The use of VIP elements at the Hotel Richard With quay resulted in high-quality concrete castings. They had a short curing time considering the climatic conditions, and showed no signs of cracks.
“In the future there will also be potential for development of the system, using prefabricated walls and beams, among other things,” says Isak Langås, a SINTEF research scientist.
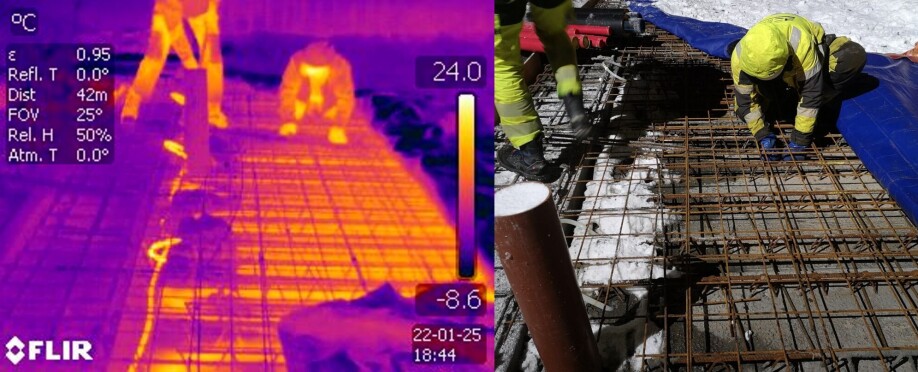
‘Contact us’
The project was initiated when Betong & Entreprenør recognised a need connected with the green transition. They contacted SINTEF via Betongklyngen CIC to get help in organising, financing, implementing, and completing the project.
“We encourage readers who have ideas or needs to contact us for a chat. We wish to contribute to more projects in the building and construction sector that are motivated by the green transition,” says Langås.
See more content from SINTEF:
-
Testing a giant ship: May take five kilometres to stop
-
A robot is helping researchers hunt for the best cancer warriors
-
Locomotives that run on diesel can be electrified
-
Where kelp is being turned into lab-grown meat
-
Immediate action is a key factor for successful restoration of marine habitats
-
Dynamic cables – the umbilical cord of ocean installations