THIS ARTICLE/PRESS RELEASE IS PAID FOR AND PRESENTED BY University of Oslo - read more
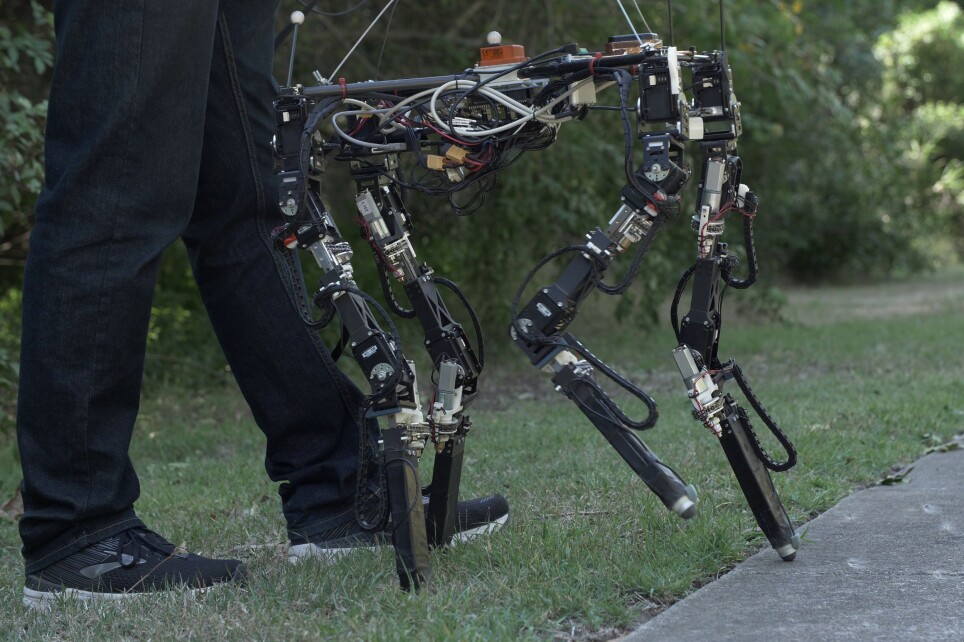
This robot adjusts the length of its legs when stepping from grass to concrete
This is the first quadruped robot that is able to automatically adapt its morphology to different conditions in unstructured outdoor environments.
The four-legged robot Dyret can adjust the length of its legs to adapt the body to the surface. Along the way, it learns what works best. This way it is better equipped the next time it encounters an unknown environment.
The name Dyret (Norwegian for “The Animal”) is an acronym for Dynamic Robot for Embodied Testing.
“We have shown the benefits of allowing a robot to continuously adapt its body shape. Our physical robot also proves that this can easily be done with today's technology”, says senior lecturer Tønnes Nygaard at UiO's Department of Informatics.
In the case of Dyret, changing the body shape means that it adjusts the length of the legs.
“We have seen that a mechanism to adapt the body shape is useful for our robot, and we believe this could apply to other robot designs too”, says associate professor Kyrre Glette.
Previously, they have shown that the robot can adapt to different environments in controlled conditions indoors. Then Nygaard spent half a year with other robot researchers at The Commonwealth Scientific and Industrial Research Organisation (CSIRO) in Australia, where they specialize in testing self-learning robots outdoors.
Tønnes Nygaard in Australia preparing Dyret to walk on its own in nature. Photo: Jack Collins
“This was previously considered too hard to achieve in the real world. Through the robot and our experiments, we've definitely shown that it’s possible”, Nygaard says to Titan.uio.no.
The results are published today in the journal Nature Machine Intelligence.
By changing the length of its legs it can automatically transition to different body shapes. Morphologically adaptive robots can operate in unpredictable environments and solve new tasks without having to be redesigned or rebuilt every time they face something unexpected.
One giant leap for a robot
For us humans, it may be hard to imagine how difficult it is for a robot to walk from, for example, concrete to grass. Just remember that you have years of experience and quite a few senses compared to a robot.
“The robot uses a camera to see how rough the terrain is, and it uses sensors in the legs to feel how hard the walking surface is”, Nygaard explains.
“The robot continuously learns about the environment it's walking on and, combined with the knowledge it gained indoors in the controlled environment, uses this to adapt its body.”
When Dyret was asked to walk on grass, it had never seen grass before. It had trained on only gravel, sand and concrete. Still, it quickly learned how to walk on the Australian grass and what was the ideal leg length.
“Shorter legs give better stability, while longer legs allow for a higher walking speed if the ground is sufficiently predictable”, Glette says.
A flat lawn may not be the biggest of challenges, but grass in nature is full of tufts and holes that can trap a long-legged robot, so Dyret will shorten its legs. On concrete, it can stretch the legs and "run" away.
The robot is also able to adapt if it gets damaged when facing unforeseen obstacles.
“Using our technology, the robot is able to adapt to one of its legs becoming weaker or breaking. It can learn how to recover, whether through limping or decreasing the length of the other three legs”, Nygaard says.
Disaster areas and mines
Currently, Dyret is not ready to take on major tasks. The purpose of Nygaard's doctoral degree has been to develop the technology and find suitable materials, and to prove that it is possible. Still, he can see several possible uses in the future.
“This is beneficial in environments where the robot might face many unexpected challenges. This includes search and rescue operations, but also agriculture where there is a wide range of challenging surfaces and weather conditions”, Nygaard says.
He also mentions exploration of mines where it is difficult for people to get to.
“One could also imagine robots at different scales, for example small pipe inspection robots, being able to benefit from such technology in the future”, Glette says.
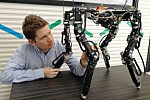
“We hope this idea, that one can change the body shape, will sound convincing to other researchers and that it may be incorporated into other types of robots.
Maybe even a trip to Mars or some other missions in space.
“I think that space robots in principle could easily have had this technology because they often will face unforeseen tasks. If they had the opportunity to change or repair themselves, it would have been good”, Glette says.
This will of course take a while. The space industry does not apply new technology overnight. After all, they must be absolutely sure that everything works after landing.
“If you send a robot to Mars, it better work”, Nygaard says.
Benefits of self-learning
Each time Dyret manages to adapt to a new surface, it will be even better equipped to meet additional new surfaces. That is the great advantage of self-learning.
If scientists were to program it to work on different surfaces, it is not certain that they would actually choose what is ideal for the robot.
“We considered gravel, for instance, to be a hard surface, but the robot did not experience it like that, which is something it was able to learn on its own”, Nygaard says.
“When learning through its own experiences, it is able to break free from the assumptions and traditions that we humans make, often erroneously.”
This means that it must be allowed to fail from time to time. Like a child learning to walk.
“You have to allow the robot to try some bad solutions first”, Nygaard says.
He brought a suitcase with spare parts to the outdoor testing in Australia.
“But luckily I didn't have to use more than a few.”
Available to everyone
Nygaard now works at the Norwegian Defence Research Establishment with other and fully developed robots. Maybe they can benefit from adapting their body? He will also continue to work with Dyret at the Department of Informatics.
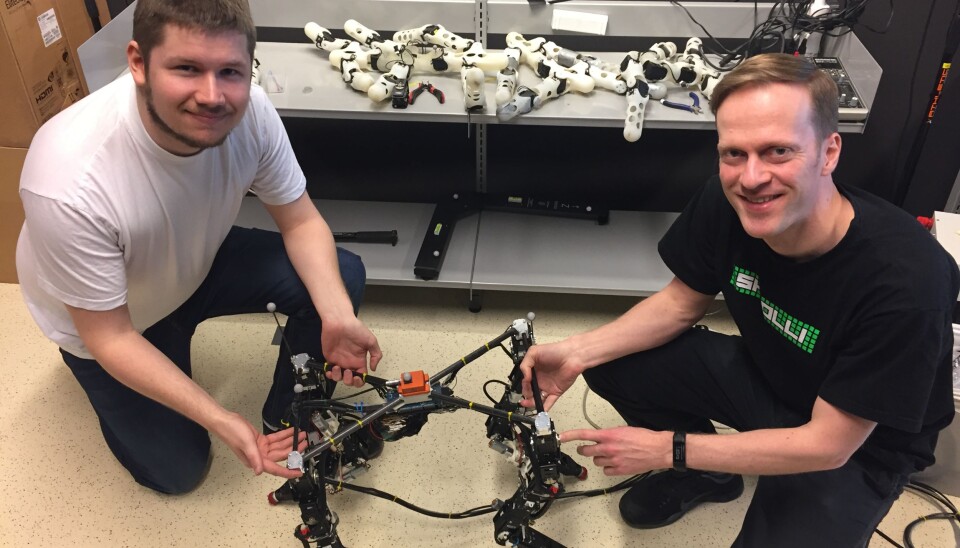
“I am now working with master students to explore other ways for the robot to learn using new and exotic methods I didn't have the time to pursue myself”, he says.
Anyone can take advantage of the new technology.
“We have released all parts of the project as open-source. Anyone can take what we've made and use it for whatever purpose they want. They can, of course, download the robot design and build their own, but I think most people will be more inclined to use parts of our solutions as inspiration in their own work”, Nygaard says.
Nygaard, Glette and their colleagues have at least reached their first goal.
“We have now tested the robot in unseen outdoor terrains, and we have equipped it with a machine learning algorithm collecting data and adapting the body to the new terrains”, Glette says.
“Bring on the unknown environments! The robot is ready”, Nygaard says.
You can also read this article in Norwegian.
References:
Tønnes Nygaard, Charles P. Martin, Jim Tørresen, Kyrre Glette and David Howard: Real-world Embodied AI Through a Morphologically Adaptive Quadruped Robot, Nature Machine Intelligence, March 2020
See more content from the University of Oslo:
-
Which surgery works best to expose impacted canines in children?
-
Glaciers are shrinking, but stricter climate policies could save twice as much ice
-
This molecule may be the key to slowing early ageing
-
Promising news for patients with Crohn's disease
-
This is how Ukrainians live with the sound of war
-
Researchers have found a link between mono and the liver disease PSC