An article from Norwegian SciTech News at SINTEF
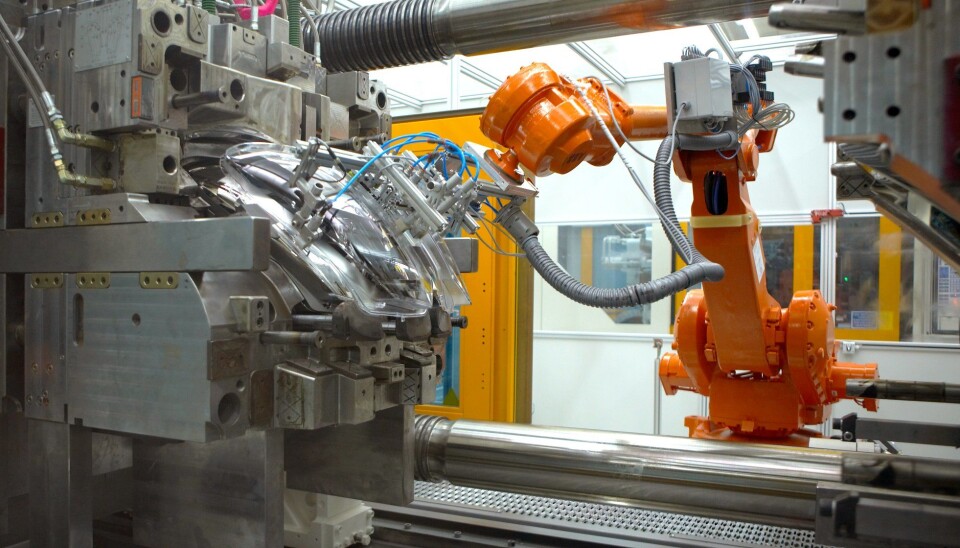
Smart firms detect their problems in advance
Sensors, data and analyses all help to give advance warning of critical situations developing on production lines. This can reduce downtime by 50 per cent.
"Firms today have to deal with strict statutory regulations, uncertainty and increasing pressure from globalisation", says Rimmert van der Kooij at SINTEF.
"This requires a new category of companies – those with the ability to be one step ahead. These are firms that must continuously be aware of what 'can happen', and thus be equipped to change the way they do things in order to achieve best practice."
As part of the EU project 'ProaSense', five research partners from six countries, together with the Slovenian company HELLA and MHWirth (formerly Aker Drilling), have joined forces with the aim of exploiting the potential benefits inherent in the huge volumes of data that the firms possess. Their aim is to promote proactive companies.
Sensors reveal trends
Sensors are incorporated into the majority of manufacturing processes to make continuous measurements and supply data. Machine operators are looking for immediate feedback about status developments, and software programmes ensure that interpretations of the data are communicated both to management and the operators.
For example, the sensors can monitor the status of all machinery on a production line. All manufacturing firms want to avoid things going wrong. They want to avoid downtime and they don't want to have to discard products due to machine failure.
If a company using drilling equipment supplied by MHWirth experiences gearbox failure in a drilling machine, its client will immediately incur significant costs as a result of downtime. If someone had predicted the failure in advance, a modification could have been made to prevent the problem arising.
"Operators want status reports and advance notification", says van der Kooij. "They're concerned about why the machine in question has stopped, and what they have to do to get it running again. It is possible from the massive flow of data to identify patterns of interest that can tell us something about how a machine's status will change in the future", he says.
The firm and its management are looking for other types of information. The data may show that in the course of a day the machines have recorded a given amount of uptime and a given amount of downtime. Is the trend going up or down? Which machine breaks down most often? Is there any pattern to the breakdowns? Why did everything go so well last month?
"Our aim is to obtain a better overview of machine status, and adopt a precautionary approach. The sensors pick up trends and tendencies", says van der Kooij.
Many variables
HELLA is one of the world's largest manufacturers of vehicle headlamps and fog lamps. In recent years, car headlamps have become larger. Lenses require greater curvature and are generally more complex than in the past. This can create difficulties during the manufacturing process, resulting in a high percentage of discarded products.
But what causes production to come to a halt? Is it pressure, air quality or dust particles? Has the temperature deviated from its standard value, or does the cause lie in human error on the part of the operator? If the data can provide any answers to these questions, then a lot will have been achieved.
The volume of information is staggering, but ultimately we're looking for a single answer to the question – 'Will the machines run tomorrow, or will some of them break down?'
"You can compare it to the forecasts provided by the Met Office", says van der Kooij. "We're also using sensors to help make predictions. Meteorologists refer to a multitude of variables in order to come to the single forecast they deliver to their clients, such as – 'tomorrow it will be 13 degrees and overcast'", he says.
So far, the main conclusion that the researchers have arrived at is that most of the sensors that the firms have installed on their machinery have provided only some of the answers they are looking for. In many cases the machines were designed many years ago and equipped with gauges that were well adapted when they were installed.
"If only we had been able to equip a production line with additional sensors, or to connect three or four sensors together, we might have been able to obtain all the data we need", says van der Kooij.
In spite of this the research group believes that they will succeed in reducing downtime at manufacturing firms such as HELLA by fifty per cent. However, they are uncertain about MHWirth because the complexity of the project is so great.