An article from University of Oslo
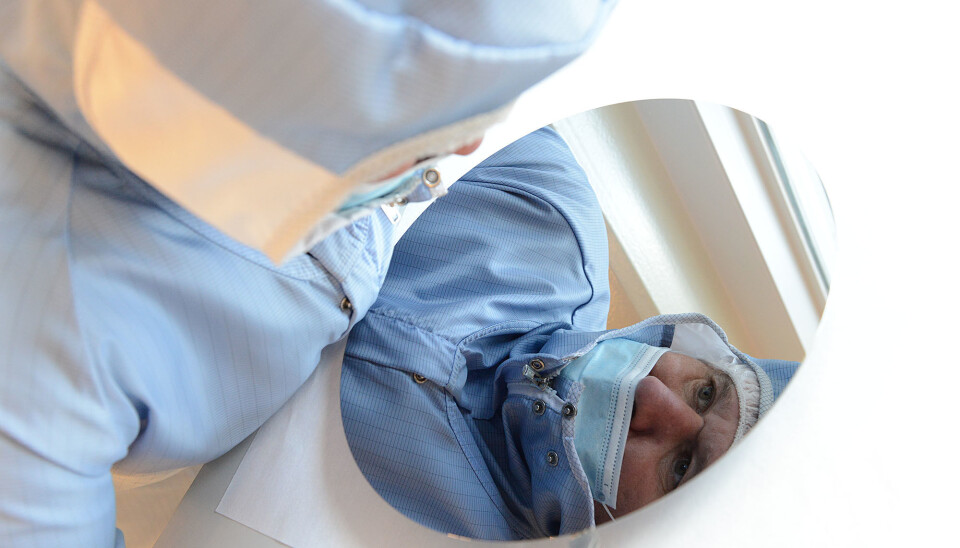
A smarter power grid with new materials
Increased renewable energy production is a burden on the power grid. A new EU project will increase the efficiency of energy consumption.
Have you ever wondered how our power grid works? If it isn't part of your job, you probably haven't. Right now, a revolution is taking place in the way we produce, transport and, not least, use power.
We are charging laptops, phones and electric bicycles; we are connecting Teslas, TGVs and induction hobs; and we are installing solar panels and wind turbines at a furious rate.
Modern power grid
"Increased renewable energy production is a burden on the power grid, as it is relatively unpredictable and highly variable," says Ole Jakob Sørdalen at the Norwegian company Eltek.
Renewable electricity production is also often distributed, which means that the direction of current in the network occasionally goes the opposite way than in traditional centralized production.
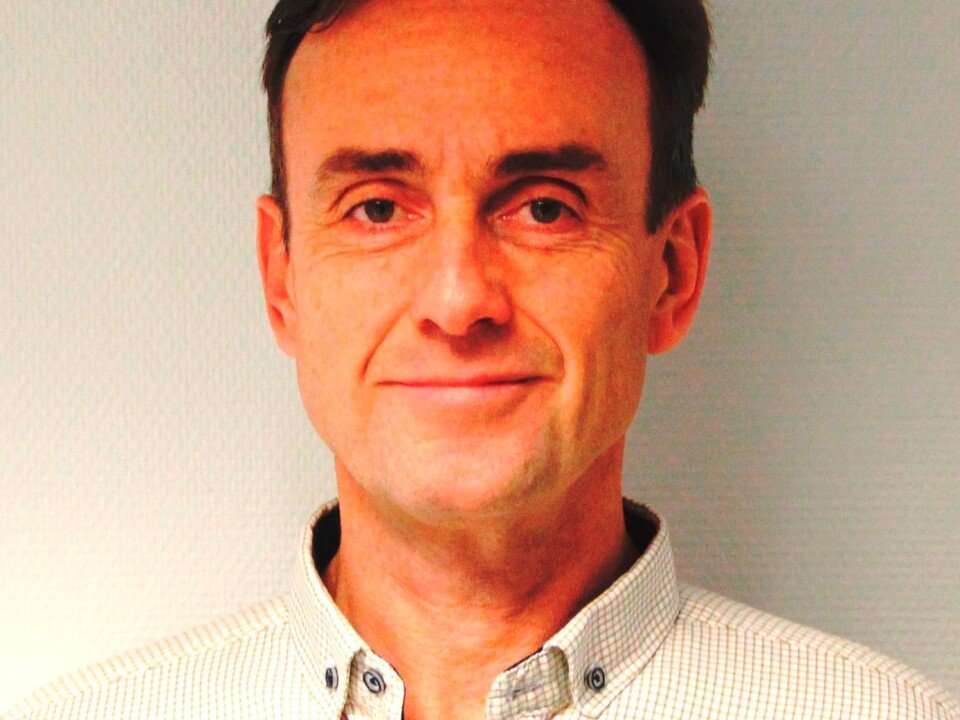
Loads with high output peaks, such as induction hobs and quick chargers for electric cars, also draw a great deal of power from the grid.
Together with energy storage, smarter current transducers will offer the flexibility needed in modern power grids.
"However, it is important that the transducers are inexpensive and efficient," stresses Sørdalen.
"Even though Eltek has led the way in the development of highly-efficient power transducers for the telecom industry, there is still room for further improvement of the efficiency. With the strong growth of telecom and computer centres as power consumers, highly-efficient current transducers will be crucial to increasing energy efficiency in society," says Sørdalen.
GaN on Si
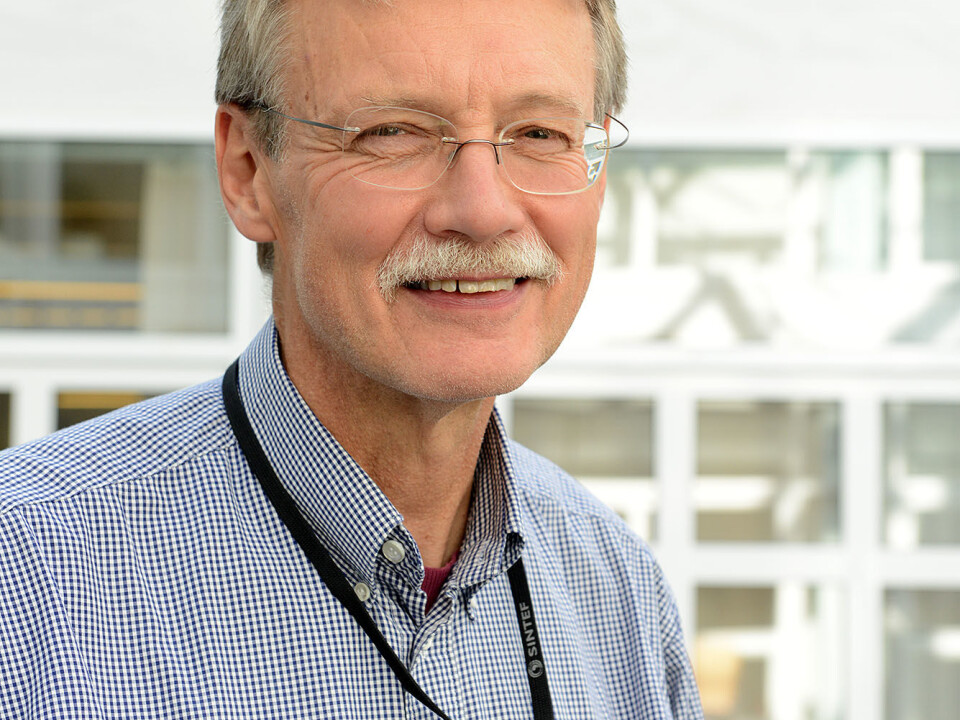
"Our goal is to reduce losses by 80–90 per cent," says Bengt G. Svensson, a professor at the University of Oslo. This corresponds to a 10–15 per cent reduction in electricity production.”
The University of Oslo is collaborating with Eltek on the giant PowerBase project – a 3-year European project managed by Infineon, with a budget of 94 Million Euros.
PowerBase will create electronic components based on gallium nitride-coated silicon – GaN. Or GaN on Si.
The new material has basic qualities that makes it more suitable. Svensson provides an example: "Take a 1 centimetre piece of silicon. You can run 100 000 volts through it before it collapses. A corresponding piece of the material GaN on Si can withstand 2-3 million volts. The new electronics will not be more expensive than we are using just now, despite being more energy-efficient and requiring less cooling."
Record large silicon wafers
In order to keep costs down, PowerBase will use unusually large silicon wafers with a diameter of 30 centimetres. Svensson does not think that anyone has ever tried to use such large wafers in power electronics before.
The University of Oslo will study defects in the silicon wafers and examine in particular whether any silicon atoms are missing from the crystal structure. If atoms are missing, the 'holes' must be filled.
Power electronics is subject to strict standards of quality: 100 times fewer defects are allowed compared with solar cell silicon.
Unique competence offered by the University of Oslo
PowerBase has 39 partners from 9 different countries. The reason that so many actors are involved is that the project will cover the entire value chain, from silicon to finished component.
The University of Oslo was chosen because it offers unique competence:
"Few institutions in Europe possess basic knowledge about point defects in silicon," says Svensson, who tells us that the section was subject to a two-day inspection by project managers Infineon before the University of Oslo was approved as a partner.
When the University is finished with the silicon wafers, it will send them elsewhere in order to be coated with a layer of gallium nitride, before the materials are used to create components.
This is where Eltek comes into the picture. Ole Jakob Sørdal explains: "Eltek's role will be that of an advanced user of components based on the new materials technology. We will develop and test new current transducers and try to exploit the positive qualities of GaN on Si."
-------------------------------------
Read the Norwegian version of this article at forskning.no