An article from Norwegian SciTech News at SINTEF
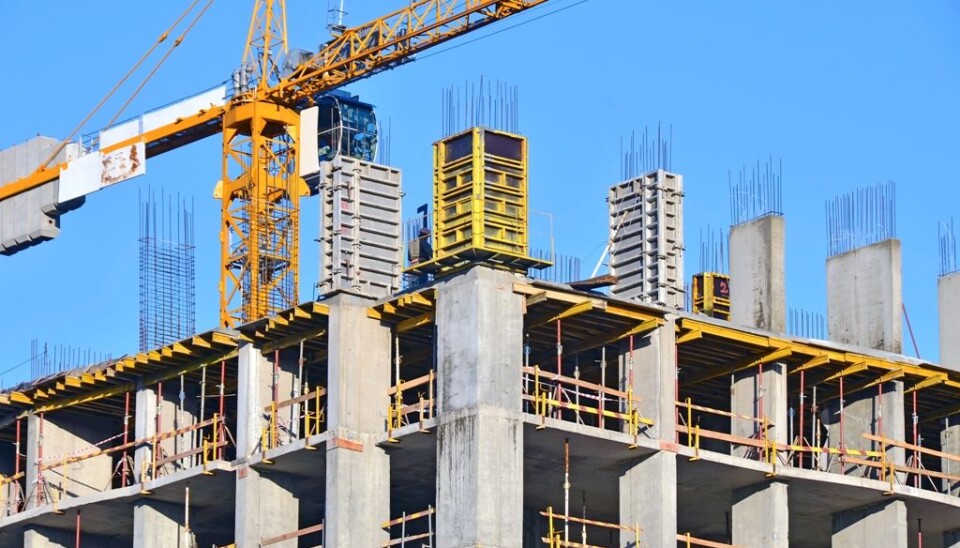
Eco-cement from Norwegian clay
Blue clay from Norway is emerging as a climate-friendly alternative to cements used to make concrete – turning a waste material into a resource.
Since the lime cement industry alone is responsible for between five and eight per cent of annual global CO2 emissions, the search is always on to find suitable substitutes.
In recent years we have found out that burnt clay can replace up to 50 per cent of the cement mixed into concrete used for construction.
“Clay is simply a major unexploited resource that may help to improve the global environmental picture”, says SINTEF researcher Harald Justnes.
“We’ve known for a while now that pure kaolin clays, which are abundant in warmer climes, are suitable as concrete ingredients. But now we’ve discovered that even impure clays, such as those we have here in Norway, can also fit the bill”, he says.
Eco-cement using burnt clay
The manufacture of cement involves subjecting limestone to heat treatments in excess of 1450 degrees. This causes the rock to release CO2 which alone makes up about 60 per cent of the total emissions. The rest is derived from the fuel used to drive the process.
Burnt clay is more eco-friendly because it doesn’t give off CO2 during heat treatment, other than those emissions resulting from the heating process. However, the volumes are much lower because the clay doesn’t need to be heated to more than between 600 and 800 degrees. Moreover, it’s possible to use bio-fuels, which reduce CO2 emissions even further.
A new life in concrete
Norwegian blue clay consists of a mixture of the clay minerals kaolin, illite and smectite, together with crystalline quartz. Many people have previously dismissed such clays as cement substitutes, not least because of their illite content. This mineral is very slow to react, and many believe that smectite is only marginally reactive.
Most people thought that using blue clay was impossible, but SINTEF researchers have now discovered how such clays can have a new life in concrete.
Just as it comes
Justnes tells Gemini that a major benefit of Norwegian clay is that it requires no refinement before use. It is much less expensive to produce and, in contrast to kaolin clays, currently has no competing applications.
“We can simply dig it out of the ground and heat treat it just as it comes”, says Justnes. “We’re talking about the everyday blue clay that is found pretty much all over Norway. It’s peculiar how it works so well considering that it contains so many contaminants”, he says.
As far as consistency goes it will be possible to replace 50 percent of lime cement with clay. However, in order to protect the concrete’s reinforcement against corrosion, by which he means fracturing resulting from rust formation, Justnes believes the clay fraction should be limited to 35 per cent until more is known.
“We need a lot more evidence before we can come to a conclusion about this”, he says. “And since each clay type behaves a little differently, we also need more research in order to optimise the heat treatment process and find out how the clay responds both in the short and long term”, says Justnes.
Focusing on clay
This year a major new international conference series was launched to address the use of burnt clay in mixing cements and as a cement substitute in concrete.
“This tells us something about how the research community currently regards clay in terms of a resource”, says Justnes.
Research has also been carried out into other cement substitutes, but right now clay is the future”, he says.
“Rice husk ash and fly ash from coal-fired power stations are examples of other substitutes which have been shown to work. However, there is too little rice available to make a decisive difference except at a local scale, and fly ash of the required quality is starting to become scarce. Besides, it has to be imported”, says Justnes.
“It’s also likely that, due to global warming considerations, coal-fired power stations will be phased out in the long term because of the large volumes of CO2 emissions they produce. But clay is found all over the world”, he says.