THIS ARTICLE/PRESS RELEASE IS PAID FOR AND PRESENTED BY NTNU Norwegian University of Science and Technology - read more
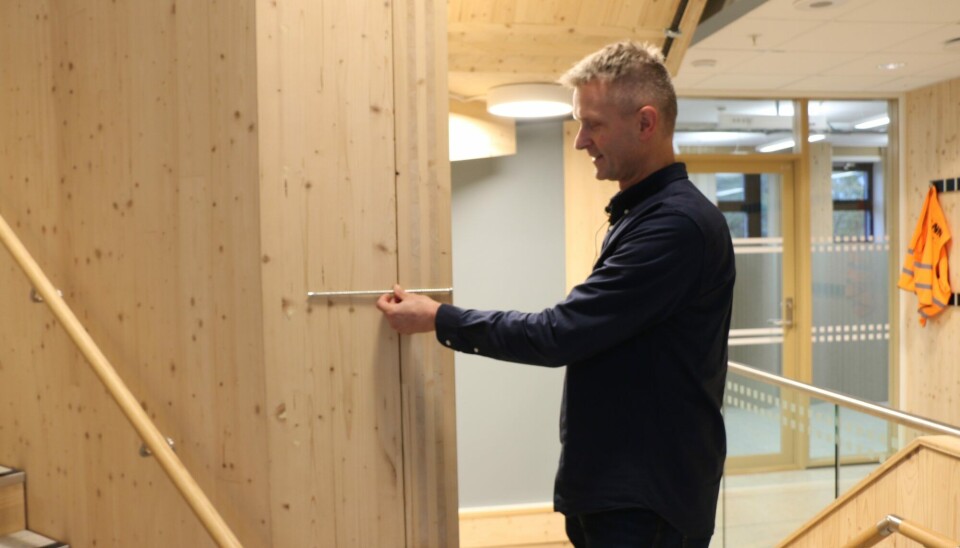
Wax, wood and CO2 — tools that can combat climate change
PODCAST: How scientists and engineers across the globe are harnessing unlikely materials to cut greenhouse gas emissions.
Three tonnes of wax. A 4-story office building made almost entirely of wood. And putting CO2 to work instead of letting it heat up the planet.
The Intergovernmental Panel on Climate Change (IPCC) says we need all the tools we have in our toolbox if we are going to have any hope of keeping global warming to the 1.5°C or 2°C level.
The Zero Emission Building Laboratory, operated cooperatively by NTNU and SINTEF, Scandinavia’s largest independent research institute, is specifically designed to develop those kinds of tools.
Constructed 500 km south of the Arctic Circle, the lab combines integrated solar panels, heat pumps and a huge vat of wax to heat and power the structure, with enough left over to sell.
Another area where NTNU researchers are developing new tools to tackle the climate is in building highly efficient heat pumps — using CO2 as the stuff inside that makes it work.
These heat pumps are spreading worldwide, and can be found everywhere from inside your Volkswagen ID electric car to the Large Hadron Collider. And also at a hotel in Hell, Norway, where the owners cut their electricity use by 70 per cent.
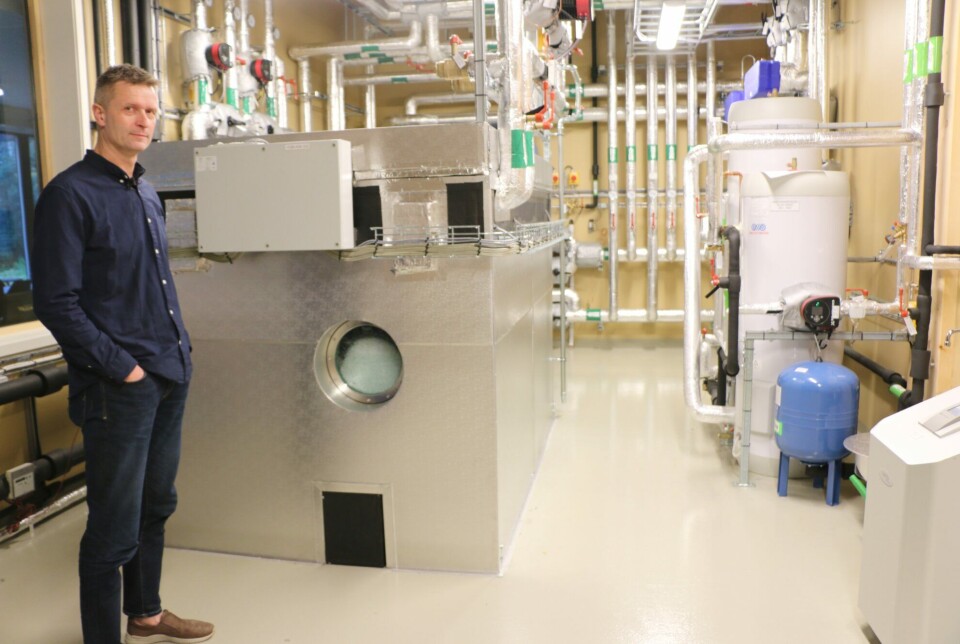
Vegetable oil to the rescue
Tore Kvande, a NTNU professor who is the ZEB Lab building manager, explains some of the different approaches being tested and used in the lab. One of the biggest innovations involves three tonnes of wax.
The wax, developed by SINTEF, melts at 37°C, which makes it an ideal substance that can be used to store heat energy. In this case, the heat energy comes from the solar panels that has been integrated into the building’s facade.
About half of the 701 panels are on the building’s roof — slanted at 42 degrees to make the most of the sun — while the rest make up the siding on the trapezoidal-shaped building. The panels on the sides of the building can take advantage of the low-angle sun during the winter, spring and autumn. The structure also includes heat pumps.
In its liquid form, the wax can take advantage of the extra energy generated by the system, because it takes heat energy to melt the wax. But when the wax solidifies, it releases the heat it stored when it was melted.
Cutting peak demand
So during the early mornings, when the building needs to be warmed up, cold water is piped through a big silver box containing the wax. The wax loses its heat to the cold water, and gradually solidifies. The water that has been heated by the wax is piped to radiators and the ventilation system, heating the building.
“I usually start early in the morning, and then it’s always liquid stuff in there. And between seven and eight o’clock, it starts to take out the extra energy and it went from liquid to solid,” Kvande says.
It’s a useful technology that acts like a battery for the extra energy generated during the day, but it’s also useful because the energy can be used when the demand is at its peak — in the morning.
Wood as carbon storage
Another way the ZEB Laboratory is pushing boundaries is in its actual construction, using massive wood and laminated timber to limit the amount of steel needed to hold the structure together.
“If we are building with wood, that’s CO2 inside the building materials, and we are not releasing it to the environment,” Kvande says.
One way the architects and building engineers made this possible was to change the way the cross beams and support columns are connected. Instead of using steel plates to attach the beams to each other, the design uses a wider-than-usual support column to which the cross beams are attached. The beams are then secured using 30-centimetre long screws.
“It’s more like in the old days, when they didn’t have steel,” Kvande says. “So just by taking away the [connecting] steel plates in most of the connections, we saved one-and-a-half tonnes of steel — that’s more than one-and-a-half tonnes of CO2.”
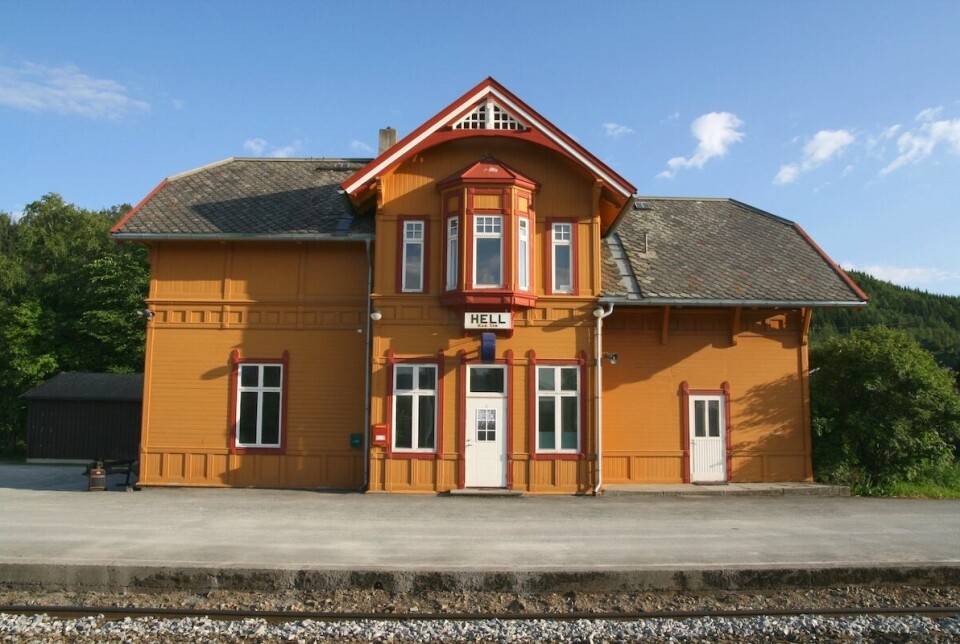
CO2 in Hell
Armin Hafner, a professor in NTNU’s Department of Energy and Process Engineering, has devoted his entire academic career to building highly efficient heat pumps using CO2 as the stuff inside that makes it work.
He was inspired by NTNU professor Gustav Lorentzen, who rediscovered and patented the use of CO2 for heat pumps. Once Lorentzen and others figured out how to make CO2 work in a heat pump, the idea began to gain momentum.
20 years ago, Hafner’s PhD dissertation focused on developing a mobile reversible heat pump that could be used to both heat or cool small spaces — like the interior of a car. Now this technology is found in many electric cars, but specifically in the Volkswagen ID series.
“The challenge with an electric car, if you have just an electric heater, more than half of your battery just goes for the heating. So you will never reach your destination. So the challenge is really how to save energy and to do this heating in an efficient way,” he says. “And that’s why more and more car manufacturers go for CO2 heat pumps. The CO2 system is nice, tiny, more compact, which is very important in mobile applications. Because space and weight is a big constraint. So that’s why you see more and more of these systems.”
Hotels are also taking advantage of the kinds of heat pumps that Hafner works with, because of their high efficiency and the fact that they can deliver both heating for the building, hot water, and refrigeration.
And you can even find a heat pump in Hell — Hell, Norway, that is.
“And they have reduced the electric power consumption by more than 70 per cent since they have converted the whole hotel from being entirely electric heated to a CO2 heat pump,” Hafner says. “So that’s a very nice story, to have a CO2 heat pump, even in Hell.”
Read more content from NTNU:
-
Voting from your sofa is secure enough. But will it be allowed?
-
It's entirely possible to make housing construction more environmentally friendly
-
Lipoedema: Sunniva had tried every diet – but with little success
-
New laser can improve self-driving cars and the internet
-
Unlocking the secrets of Viking and medieval walrus tusk trade
-
Why are migraine symptoms worse in patients who get little sleep?