THIS ARTICLE/PRESS RELEASE IS PAID FOR AND PRESENTED BY NTNU Norwegian University of Science and Technology - read more
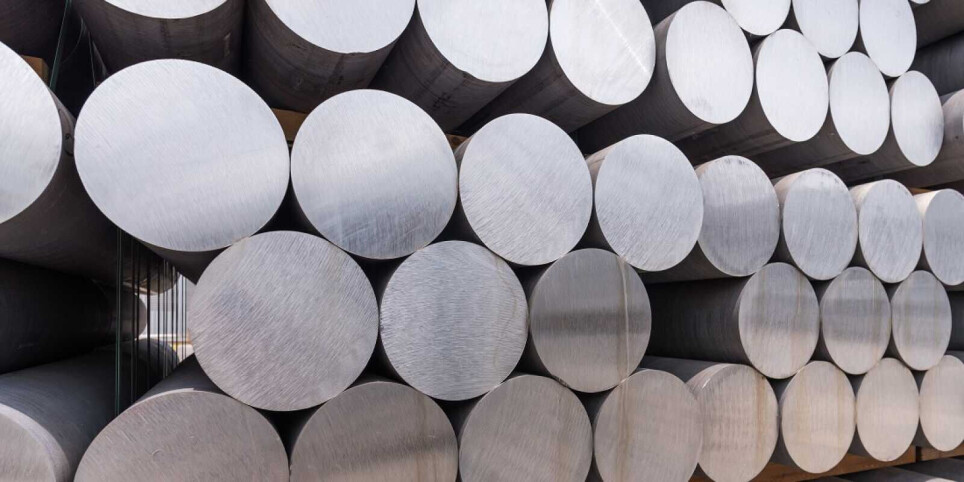
Researchers are working on an atomic level to make stronger aluminium
The new alloys retain their strength at high temperatures are useful in engines and for other applications where the components get hot.
Humans have been mixing metals to create more useful materials for thousands of years. The Bronze Age, which started around 3300 BC, was characterised by the use of bronze, an alloy of copper and tin which is stronger than either metal alone.
Researchers at NTNU have now discovered a counterintuitive way to make a much more recent invention – nanograined alloys, featuring nano-sized grains of the alloying element – even stronger.
Aluminium is a metal that is widely used to make components in the aerospace, transport, and construction industries, in part because it is lightweight yet durable. Alloys of aluminium retain these qualities but are stronger than aluminium alone.
“If it was a pure aluminium, of course, it’s not strong enough,” Yanjun Li says.
He is a professor of Physical Metallurgy in the Department of Materials Science and Engineering at NTNU.
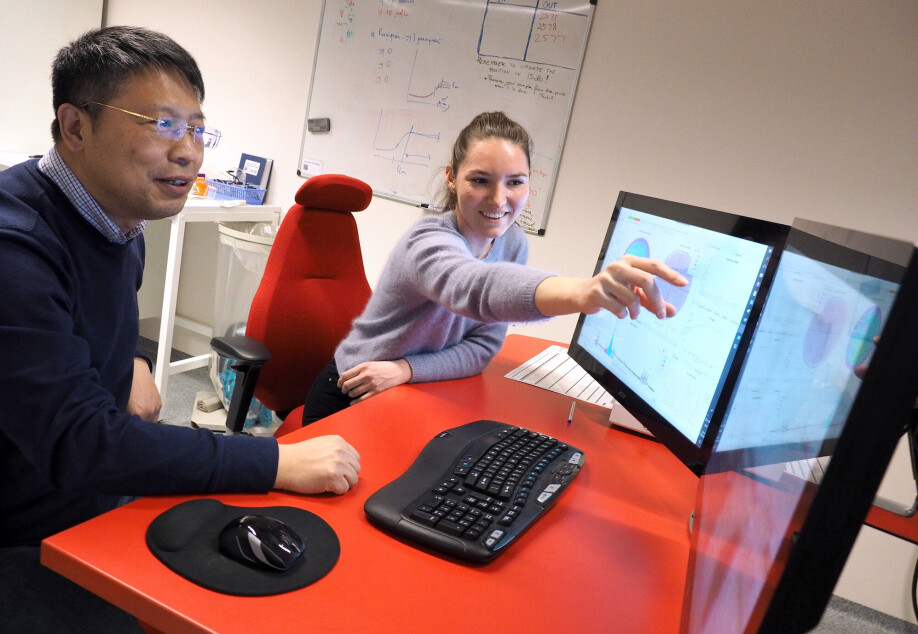
Large particles decrease strength
But in recent years, researchers attempting to make nanograined alloys of aluminium containing copper have run into a proble. The copper atoms have a tendency to clump together, forming coarse particles with aluminium inside the material, especially at temperatures higher than 100°C.
When the copper is no longer evenly distributed throughout the material, the alloy becomes weaker.
“They accumulate together, forming large particles. These large particles can actually decrease the strength,” Li says.
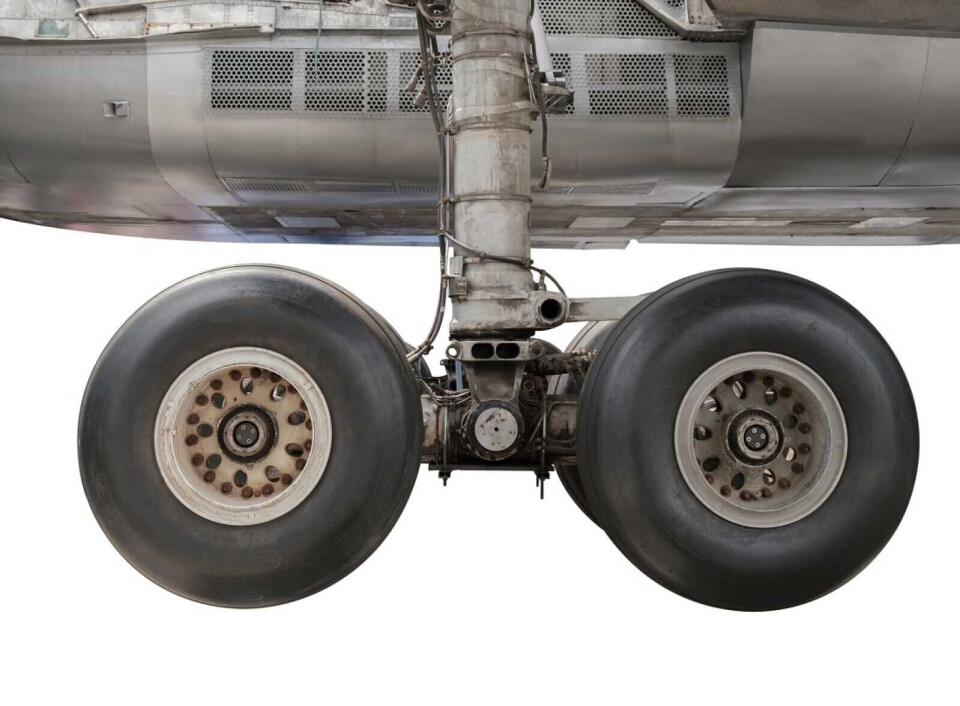
Adding vacancies for stability
Copper atoms can move through material if there is a so-called vacancy – a space not occupied by atoms – that they can move into.
So researchers have been trying to minimise the number of vacancies to reduce the ability of atoms to move.
“If there are no vacancies, of course no atoms could move,” Li says.
But now Li and his colleagues have found a way to increase the number of vacancies and at the same time increase the strength of the resulting alloy.
The researchers added scandium atoms as well as copper ones to aluminium, while also increasing the number of vacancies.
The scandium and copper atoms, together with the vacancies, formed structures that could not easily move through the material.
“Together they are very stable,” says Li. “It becomes more difficult for any of them to move.”
Thanks to the new scandium-copper structures, large aluminium-copper particles that would have previously formed were completely suppressed, even when the alloy was heated to 200°C for 24 hours.
This stability means the copper atoms stay evenly distributed throughout the material, and the alloy retains its added strength.
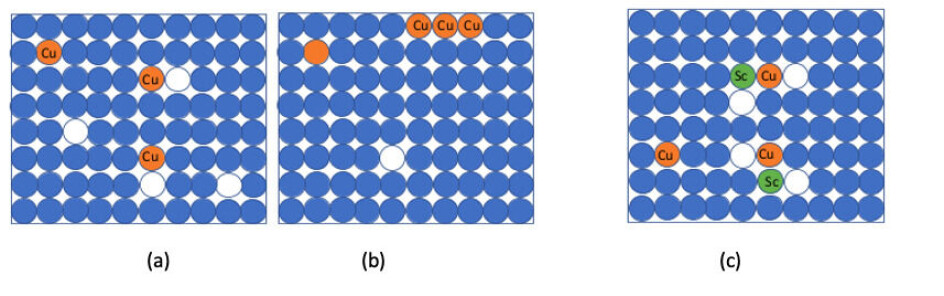
Atom probe tomography key
The team saw the copper-scandium-vacancy clusters using Atom Probe Tomography (APT), a technique which makes it possible to see what’s happening at the atomic level inside a material.
PhD student Hanne-Sofie Søreide prepared very thin needles – only 50 nm in diameter – of the alloy using NTNU Nanolab’s Focused Ion Beam.
She then used the atom probe to evaporate atoms, one by one, from the top of the needle, while a detector captured information about them.
“Different atoms can fly faster or slower,” Professor Li says.
Using this information, the researchers reconstructed a picture of where each atom originally was in the material. They saw that atoms of the two different alloying elements were joining together inside the aluminium.
“They are bonding together, we can detect this with copper and scandium,” he says.
The researchers confirmed their findings using transition electron microscopy.
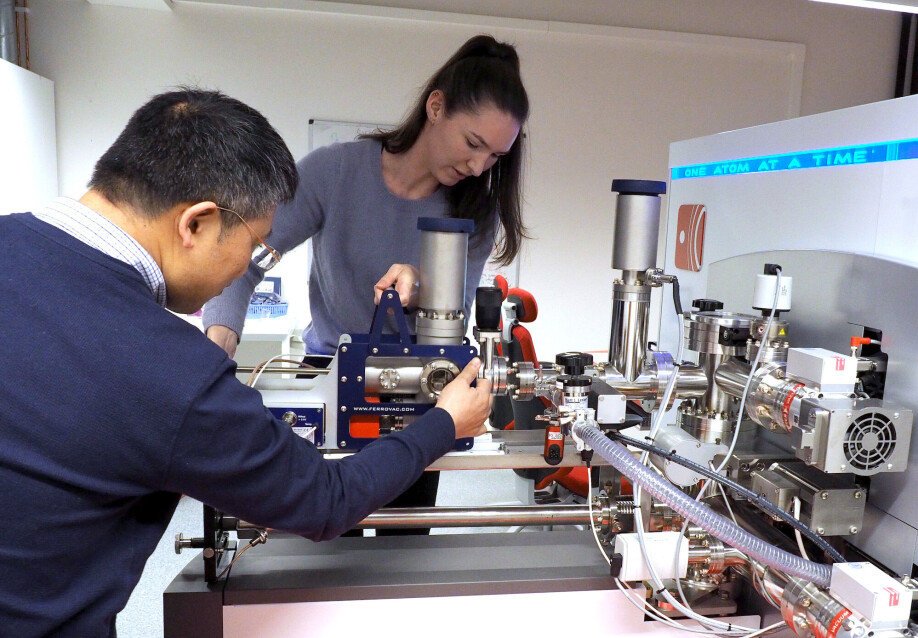
50 per cent stronger
Li says the team have already used these findings to make an aluminium alloy that is 50 per cent stronger than alloys containing the same amount of copper that are currently available commercially.
While the materials Li and colleagues are making in the lab are still far from ready for application in industry, alloys that retain their strength at high temperatures are useful in engines and for other applications where the components get hot.
NTNU’s atom probe lab is the first facility of its kind in Norway. Li and his colleagues hope that using APT will help them find other new materials with desirable properties.
“By really understanding the material in the atomic scale, it can help us to design new alloys, new materials with even higher strength. Without this kind of instrument, it’s almost impossible to understand these materials," he says.
Reference:
Wu et al. Freezing solute atoms in nanograined aluminum alloys via high-density vacancies, Nature Communications, vol. 13, 2022. DOI: 10.1038/s41467-022-31222-6
Read more content from NTNU:
-
New laser can improve self-driving cars and the internet
-
Unlocking the secrets of Viking and medieval walrus tusk trade
-
Why are migraine symptoms worse in patients who get little sleep?
-
Premature babies should also have early skin-to-skin contact with their mothers
-
Does being a good swimmer mean you are safe in the water?
-
Elderly with dementia are subjected to violence, abuse, and neglect in their own homes