An article from Norwegian SciTech News at SINTEF
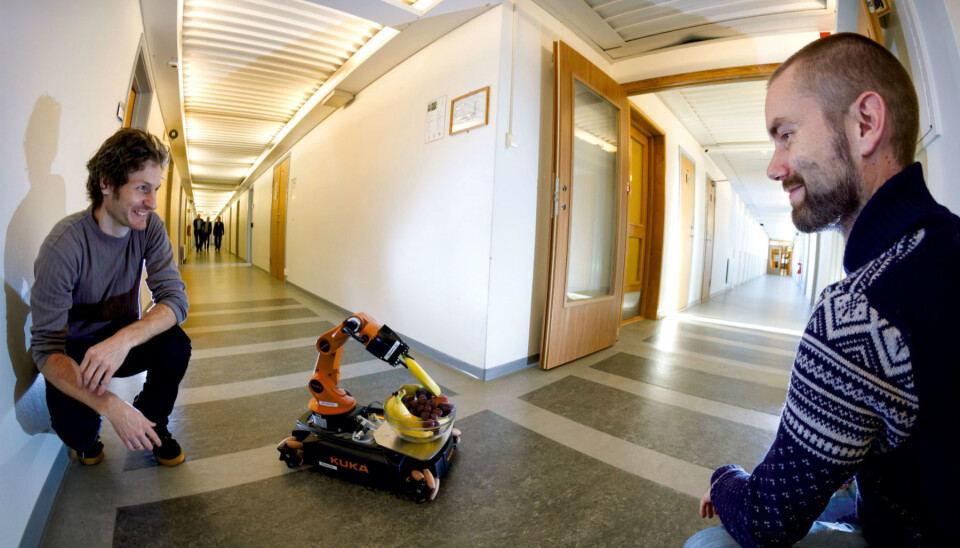
Making robots work out where they are and where they’re going
Most people can quite easily find their way outdoors or inside a building – a robot has no idea.
Denne artikkelen er over ti år gammel og kan inneholde utdatert informasjon.
A small, saucer-shaped vacuum cleaner hums gently as it rolls around the floor. It started in the middle of the floor and has now worked its way outward in an ever-expanding spiral. Every time it bumps into something, it reverses a little and sets off again.
To our eyes, this might seem like a random process – as if the tubby little cleaner was thinking ‘If I keep going for long enough, I’ll probably get it all done in the end’.
No simple or inexpensive solutions
This isn’t so far from the truth, according to SINTEF researchers Sigurd Fjerdingen and Johannes Tjønnås. Indoor service robots find it difficult to work out where they are and where they’re going.
The researchers are finding that both entrepreneurs and small companies want robots to carry out tasks such as large area tiling or to function as automatic drilling systems in buildings. The same applies to companies developing welfare technologies to assist the elderly. Most current solutions are too expensive. This is why Tjønnås and Fjerdingen want to look into the possibility of finding simpler alternatives.
No problems outdoors
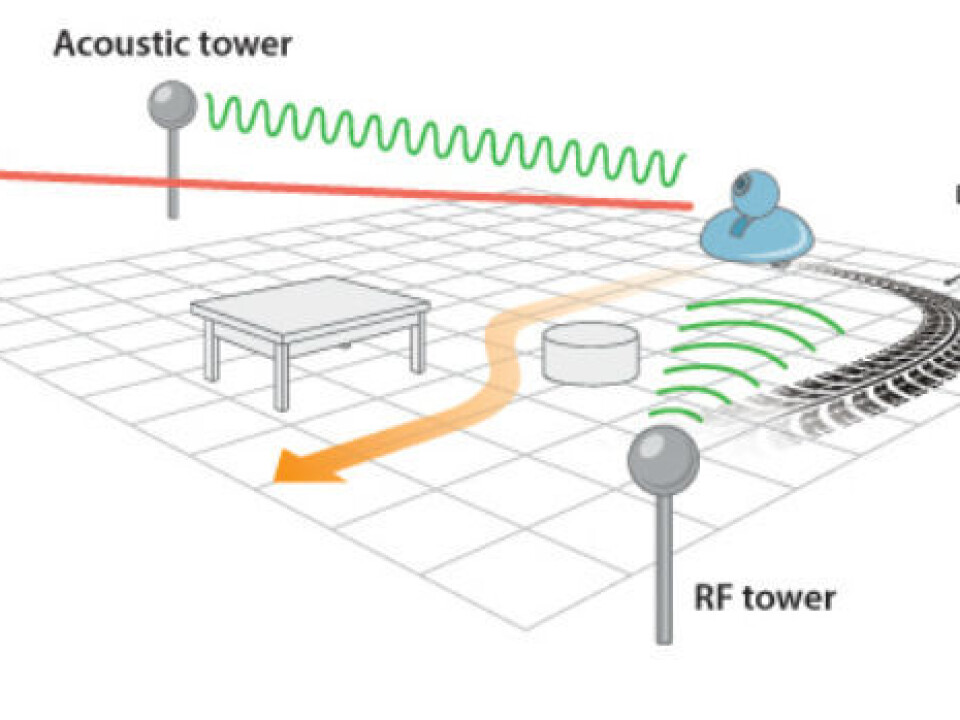
Researchers call it “positioning” – the method by which an object’s location is identified on a map.
Ships, aircraft and lawnmowers cannot reason, but they can find their way about with the help of GPS technology. The GPS is made up of 24 satellites which circle the Earth in six different types of orbit.
“The principle is based on measuring the distance from a given point with a known position”, explains Fjerdingen.
To get an accurate location, the receiver has to obtain signals from 3 satellites. In narrow city streets, part of the sky is obscured, so accuracy is poorer. However, if a lawnmower robot relying on GPS finds itself in the shadow of a house, it will run into difficulties.
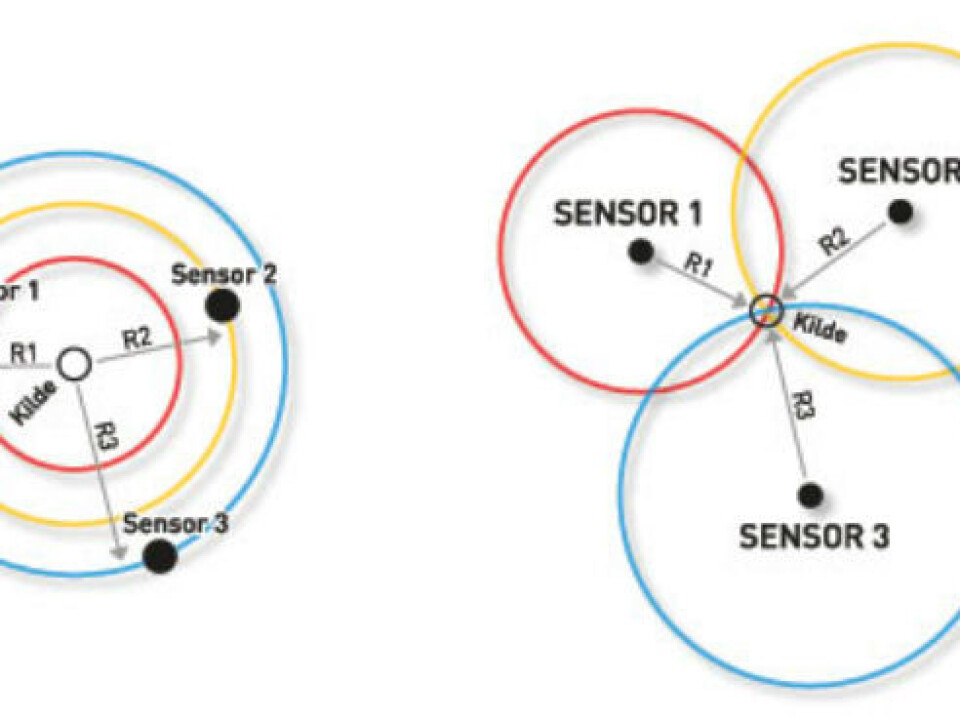
“The lawn would end up looking as if it had been mowed by a drunkard, although usually such robots also carry sensors and other systems to help them out”, says Fjerdingen.
We need an indoor coordinate system
However, most people in our part of the world spend much of the day indoors, where GPS is of little use.
“Household robots not carrying out random tasks such as washing and vacuum cleaning, or assisting and encouraging the elderly in their social training, have to be told where to go and what to do”, says Tjønnas. “If not, they won’t move at all”, he says.
So how do you get them to work?
According to the researchers, a robot can carry out its tasks as long as it can navigate within a coordinate system.
“Instead of using satellites, we have to employ a design utilising systems involving a variety of optical, radio-based and acoustic technologies”, explains Fjerdingen.
One option is to place artificial satellites indoors. If the robot is equipped with sensors, it can use these to calculate where it is and find its way around.
Measuring movement variations
Another solution involves so-called “dead reckoning” which, according to the researchers, is traditionally used by ships at sea in poor visibility. A compass is used to determine the vessel’s course, and distance is calculated using the speed of the vessel. The calculations are based on continuous measurements of the vessel’s movements and its speed.
Navigation can also be carried out using several inertia sensors which measure acceleration and rotation velocity. Such systems are currently used by modern vessels, aircraft and spaceships. Measuring movement allows the system to work out the position.
A robot’s wheel revolutions can also be used to help calculate its position. For example, if the left wheel is revolving faster than the right, the robot has completed a turn.
Combining approaches
Tjønnas explains that all these methods are well established and adequate for purpose, but if we have to rely on only one of them, while at the same time demanding high levels of accuracy, systems costs rise dramatically.
Achieving very precise and effective solutions requires a combination of sensor systems with complementary capabilities. For example, we can put together a robot with “inexpensive inertia systems” combined with “inexpensive distance measurement systems” and produce an integrated system which is less expensive, more accurate, and more robust in the face of changes in its surroundings.
Same map
Back to the robot vacuum cleaner. Designed to roll across a given floor area, it doesn’t matter if it can’t tell the difference between a chair and a table, as long as it avoids bumping into them. It is distances alone that are important to such a robot, not the context of its surroundings.
“However, context is vital to a service robot interacting with people”, says Fjerdingen.
In situations where health care workers want robots to carry out routine tasks such as fetching the laundry, they might use commands such as; ‘Fetch the clothes from the washing room and take them to the chute!’
“Constructing its own map doesn’t help the robot here, because it has to have the same view of the world as you do”, the researcher says.
View of the world
“When we say ‘pick up the cup’ or ‘put the cup here’, we are using a map developed in our brains”, says Fjerdingen. If the robot is to do what we tell it, it has to have an identical map in its ‘brain’.
“It isn’t easy! And if we want to get the robot to grasp the cup, things get even more difficult”, he says.
But what about industrial robots? They can grip things and move them about, can’t they?
“Absolutely. But they are fixed in a pre-determined position, and the objects they have to grasp are also lying in positions which are easy to calculate”, says Fjerdingen.
Modules make it cheaper
Tjønnås and Fjerdingen have received funding to carry out an in-house study into localisation, and are now working on discovering less expensive solutions. They believe that building a new robot from scratch with its main focus on localisation will involve a major investment in time and resources – a major engineering project with high development costs.
“On the other hand, it would help if we had an already established platform which could be adapted according to the desired application”, says Fjerdingen.
“We envisage combining modules which can be plugged in and connected according to requirements. But first we have to construct a demonstration model and establish a platform from which we can develop the concept. Then we’ll see. If we can avoid repeating the same development process each time, we may be able to produce something which can be useful to many people.”