This article is produced and financed by NTNU Norwegian University of Science and Technology - read more
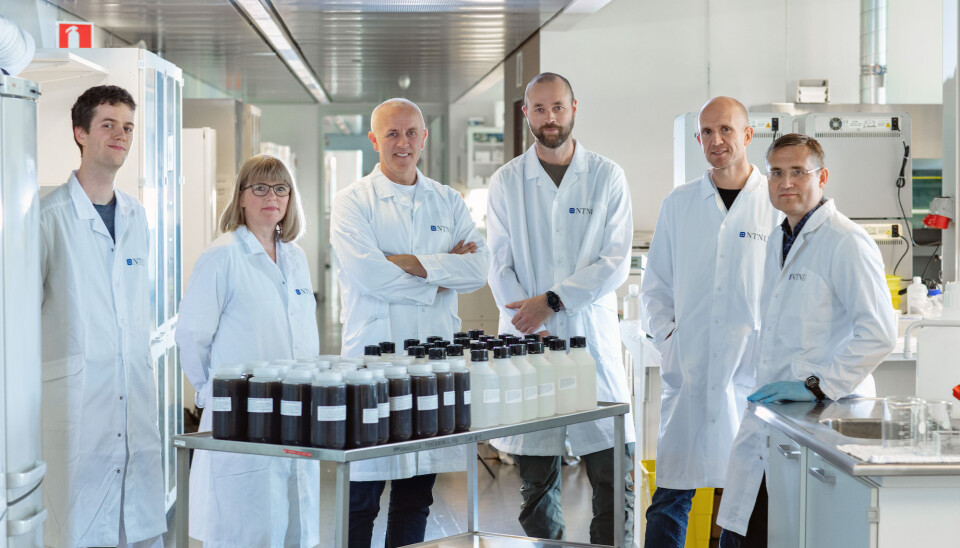
Norwegian COVID-19 test to be used in India and Denmark
The highly sensitive test relies on magnetic nanoparticles to extract viral RNA.
The Norwegian University of Science and Technology (NTNU) has signed agreements to deliver as many as one million COVID-19 test kits to DTU, the Technical University of Denmark, and APS LABS, an Indian biotech company.
The highly sensitive test, developed by NTNU researchers, relies on magnetic nanoparticles to extract viral RNA. More than 5 million NTNU COVID-19 tests have already been supplied to the Norwegian health authorities.
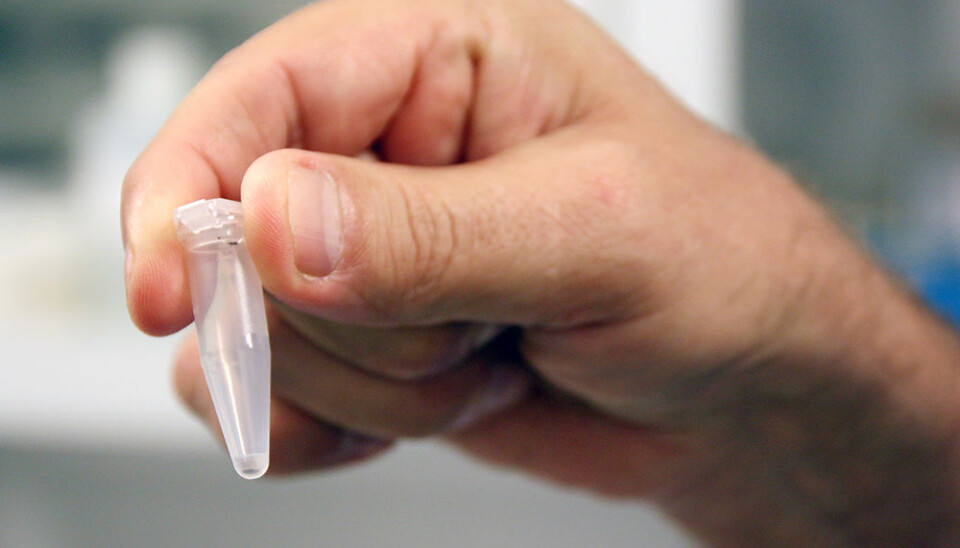
“Testing and tracing infections is absolutely essential to maintaining control of the infection situation. The fact that NTNU has developed a new test method for detecting the coronavirus means that more people can be tested and that patients can get answers faster. It is very positive that this technology can now also be useful internationally,” says Bent Høie, Norway’s Minister of Health and Care Services.
Can help with testing shortages worldwide
“We have been contacted by health ministries and private companies from countries in Asia, Africa, North and South America and Europe,” said Tonje Steigedal, from NTNU Technology Transfer, who is part of the NTNU test team and responsible for the commercialization of the technology.
“We are delighted to announce that DTU and APS LABS are the first outside of Norway to benefit from the NTNU technology.”
Helene Larsen, Head of Development at DTU’s Centre for Diagnostics in Denmark, said she had just received her first shipments of test kits and was looking forward to getting the testing up and running. She said DTU is doing tests for a number of Danish hospitals and hopes to increase the lab’s capacity to do as many as 10 000 tests a day.
“What we like about the NTNU system is that it can be used with our open robot system,” she said, which means that robot systems can be used with reagents from different vendors, including NTNU’s.
Another big advantage is that the kits are readily available, she said. “The market is still very competitive out there, and the fact that it is possible to get a kit component so readily is sensational.”
Dr. Paritosh Shekhar, director of APS LABS, said his organization had evaluated the NTNU test kits and “found them extraordinary.”
“The performance was at par with top leading brands,” he said. A“Quality was the factor for why we chose NTNU. Another reason was to support a research university rather than a commercial company. We strongly feel this association will be complementary for both of us.”
Developed out of necessity
In late March, huge international demand for the reagents used for COVID-19 testing meant that Norway, like other countries, was having a hard time getting enough tests to track the disease among its population.
In response, Magnar Bjørås, a medical researcher from NTNU’s Department of Clinical and Molecular Medicine, offered colleagues from St. Olavs Hospital help with a made-in-Norway COVID-19 test.
The offer of help was accepted and Bjørås and his network got to work. By mid-April, the NTNU/St. Olavs Hospital team had developed a highly sensitive test. Validation results showed that the NTNU test was at least as good as conventional tests. It was then approved for use by Norwegian health authorities.
Multidisciplinary research – a key to many challenges
Bjarne Foss, Pro-Rector for Research at NTNU, says Norwegian society has high expectations for NTNU as Norway’s largest university.
“We are a multi-disciplinary university with a strong profile in science and technology,” he said. “Multi-disciplinary solutions provide the answer to many societal challenges, and the NTNU COVID-19 test is a perfect example of the strength of this approach. Two strong research groups at NTNU’s faculties for Medicine and Health Sciences and Natural Sciences, respectively, developed this test method together, which by construction depends on a multi-disciplinary approach.”
“At NTNU we are proud of this contribution to fight the COVID-19 pandemic. We will continue to encourage our researchers to pursue research across disciplines both within NTNU and in cooperation with research groups at other institutions,” Foss said.
Easily upscaled
One key aspect of the NTNU test is a specific combination of polar solvents, buffers, salts and other chemicals that do not damage the viral RNA molecule itself. The solution contains substances that crack the virus open so that its genetic material can be extracted.
NTNU has also developed iron oxide magnetic nanoparticles that strongly bind RNA. Once the magnetic nanoparticles are coated with the viral RNA, they can be removed from the solution using a magnet. PCR technology can then identify the genetic code from the RNA and compare it to the coronavirus.
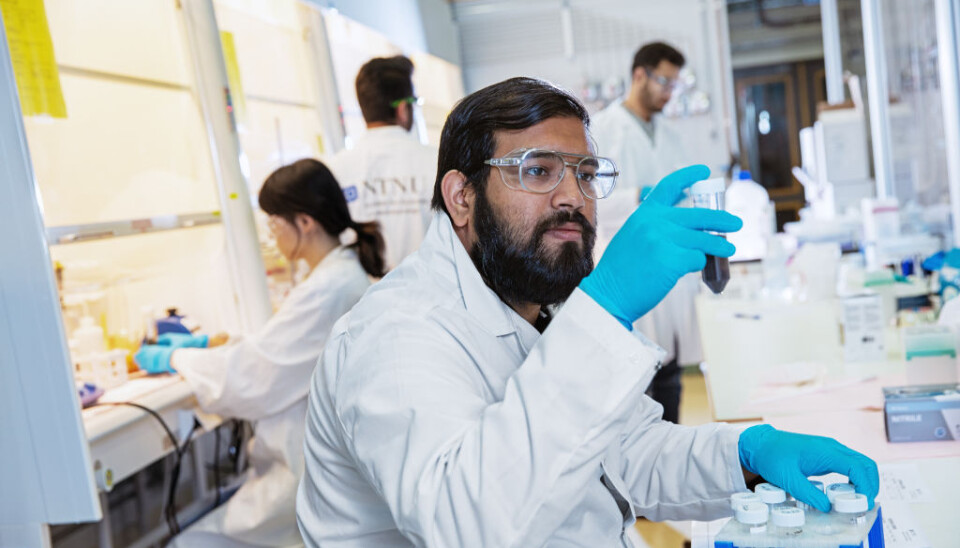
The newly developed manufacturing process has proved to be very upscalable, which has enabled the NTNU labs to produce these high-quality and high-performance magnetic nanoparticles in very high volumes. Three laboratories at the Department of Chemical Engineering are currently manufacturing the magnetic nanoparticles, while another laboratory at the Department of Clinical and Molecular Medicine is making the solvents and buffers. The process allows the production of up to 1.2 million test kits per week.
“The key behind our success has been the cooperation across departments and with NTNU Technology Transfer and the hospital,” Bjørås said. He said increases in production capacity will allow the groups to produce up to 5 million test kits a week.
At the same time, the test kits are subject to rigorous quality control and validation before shipping to customers. The magnetic nanobeads and buffers, and then the entire test kits are verified against a known COVID-19 positive patient sample.
Efficient production
The process was developed by the teams around Bjørås and Sulalit Bandyopadhyay, a postdoc at the university’s Department of Chemical Engineering, along with Anuvansh Sharma from the university’s Department of Materials Science and Technology and their colleagues.
In the process of gearing up to produce tests for Norway, the researchers improved the efficiency of the production system to the point where the lab is able to make more than enough tests for use in Norway.
Bandyopadhyay, who had previously been studying how a version of the particle can be used to study river water chemistry, has been eager to help ease the test shortages that continue to plague other countries.
“The need out there is very great, and we have the kits that can help with the shortage,” he said.
“Our mission is to provide the NTNU COVID-19 test to health care services across the globe,” Steigedal and her NTNU Technology Transfer colleague Eivind Andersen said.
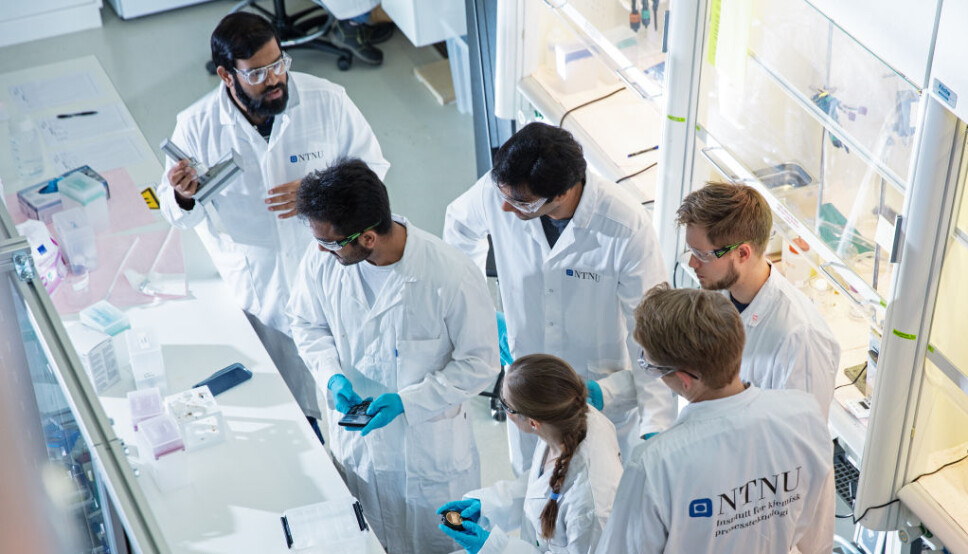
Patents maintain control of intellectual rights
NTNU Technology Transfer has filed patent applications on the methods and products related to the NTNU COVID-19 test. The motivation is to secure control of the intellectual rights and provide access to the new test in an ethical and justifiable manner.
At the same time, the university hopes to expand the number of countries to which the test will be exported.
“We need to find the right partners in each region/country. In some cases that could be national health authorities, or it could be hospitals or other health care services, Steigedal said. “It could also be life-science companies that have a relevant position in the value chain for test equipment for virus detection.”