This article was produced and financed by The Research Council of Norway
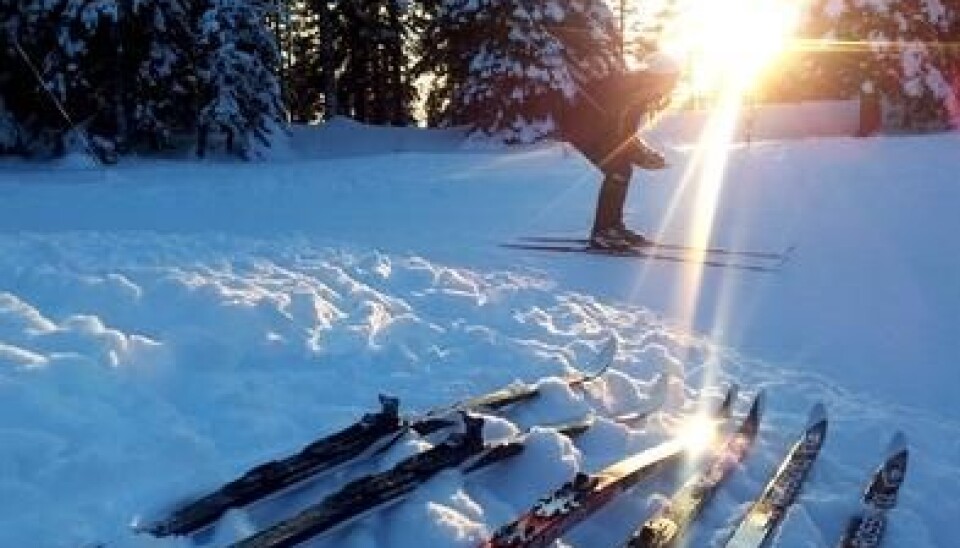
On the ski trail of success or failure
The glide of a pair of skis is not something to be taken lightly when going for World Championship or Olympic gold. The physical structure on the base of skis is tailored to each venue.
Denne artikkelen er over ti år gammel og kan inneholde utdatert informasjon.
When members of Norway’s national cross-country ski team are poised to start a race, neither they nor the spectators give much thought to the fact that the base of their skis has been developed with the same research methods and equipment used for oil platforms and hip prostheses.
The Norwegian Olympic Committee, which is responsible for developing elite sports in Norway, and the Norwegian national team are leaving nothing to chance.
In search of the championship glide
At the Norwegian University of Science and Technology (NTNU) in Trondheim, researchers are investigating how to prepare the base of skis in order to get a championship glide.
Felix Breitschädel, a doctoral fellow at the Centre for Sport Facilities and Technology (SIAT), has studied a myriad of combinations involving ski bases and waxes. Using a 3D microscope, he analyses the ski base structure at the nano level and, with the aid of a spectroscope, he sees which materials make up the composition of the surface layer.
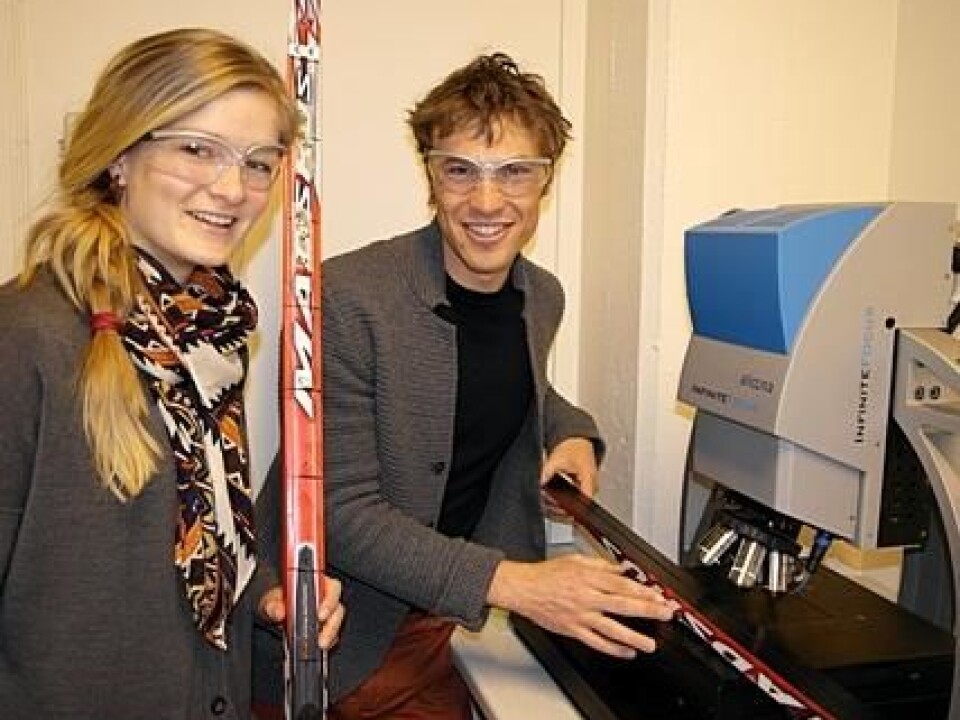
“Minor subtleties in the structure of a ski base and the additives applied may have a significant effect on ski friction and thus ski glide,” states Breitschädel. The margins are small. A slight change in friction can make the difference between victory and an undistinguished finish.
SIAT is collaborating with the TribologyLab at the Department of Engineering Design and Materials at NTNU. Tribology is the science of friction, lubrication and wear. The lab houses an array of advanced equipment that can be used to secure more cross-country gold medals.
Good ski glide based on science
The Norwegian Olympic Committee has been engaging researchers at NTNU for over a decade in order to achieve the best glide on different types of snow. While other countries conduct countless tests of skis on the trails, the Norwegian Olympic Committee has turned to science to find the best waxing solutions.
The researchers in Trondheim are now hard at work in preparation for the 2014 Winter Olympics in Sochi, using methods that are more advanced than ever. In the past two years, the ski researchers have had access to equipment procured for the TribologyLab. The laboratory has been built up under NODE ART, a project examining friction and corrosion in petroleum drilling equipment and which has received funding from the Research Council of Norway.
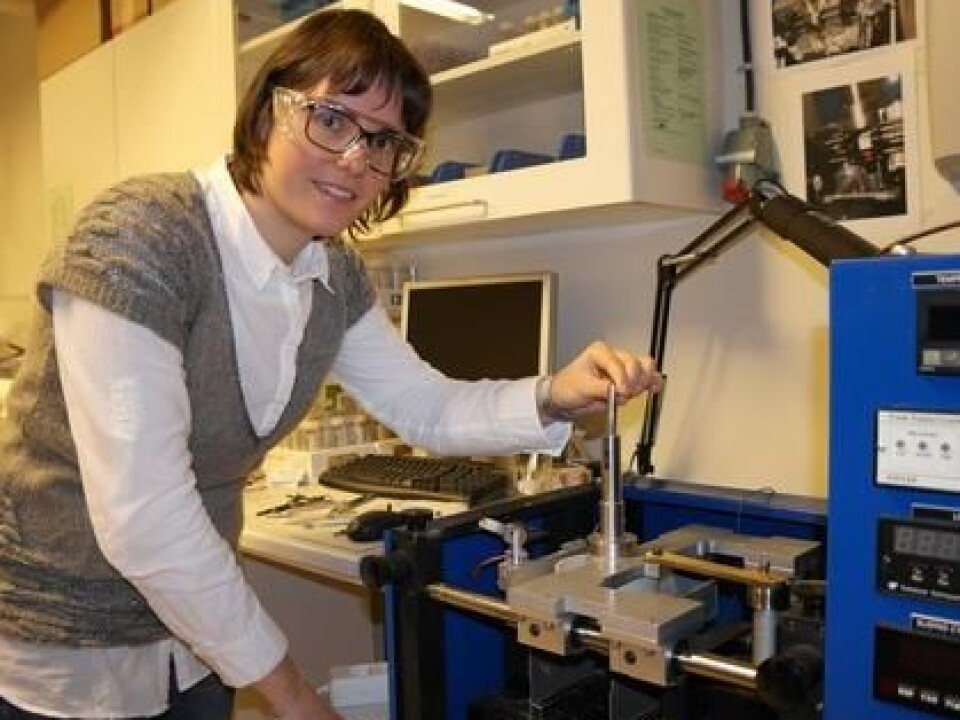
Ski manufacturers are continually experimenting with new additives to improve the gliding properties of their products. The plastic on the base of skis is normally comprised of a high molecular weight polyethylene to which materials such as molybdenum disulphide and Teflon are added. These same materials are used in the petroleum industry, in hip prostheses and in wind turbine blades.
Obtaining skis from a manufacturer, however, is only the initial step in developing a championship ski. For years, Norwegian ski preparation specialists have improved the performance of skis by etching micro rills into the base of the skis and experimenting with various types of wax before testing the skis on the trails. The researchers at NTNU are digging even deeper. They are examining the very structure of the ski base in order to provide ski waxing teams with new knowledge on what works best.
“The usual method of testing skis involves comparing the glide of different pairs of skis. We, however, are able to take precise measurements of different structures and waxes and analyse wear,” says Mr Breitschädel, who holds a master’s degree in sports equipment technology and is pursuing a doctoral degree in technical improvement of cross-country skis.
From the laboratory to the trails and Sochi
Working together with Felix Breitschädel is Associate Professor Nuria Espallargas, head of the TribologyLab, and master’s student Nora Holst Haaland, who is researching nano ski waxes. Ms Haaland is examining how much nano ski wax the base of the ski can absorb, how the wax reacts to water and how much of it wears off during a race.
The researchers are measuring ski friction in the laboratory in conditions as cold as -20 degrees Celsius. A portion of the ski base glides back and forth over a surface made of ice or snow, providing accurate measurements of friction.
Afterwards, the skis are taken into the forest to be tested on proper trails.
“If the results we observe on the ski trails are the same as those in the TribologyLab, we can avoid further testing and save time,” Haaland explains.
This knowledge will be then transferred to the ski preparation specialists for the Norwegian national cross-country team. Felix Breitschädel has already visited Sochi in order to test skis. Local snow conditions there are completely different from those in Norway and skis will have to be prepared in an entirely different way.
Icebergs must glide past oil platforms
Breitschädel is working part-time for the Norwegian Olympic Committee and part-time on his doctoral thesis at NTNU, allowing Norwegian cross-country skiers to benefit from tribology knowledge for the oil and gas industry acquired in Trondheim.
Conversely, the research on ski glide is of benefit to the petroleum industry.
“As petroleum activities move closer to the Arctic, platforms and ships will have to be able to withstand ice and icebergs. We are studying surface coatings to determine which prevent ice adhesion and allow drift ice to glide past the hull of a ship or an oil platform,” Espallargas says.
The research carried out in Trondheim has already saved the petroleum industry millions of Norwegian kroner in maintenance and repair of hydraulic equipment on drilling platforms.
Hydraulic cylinders are used to keep the drill string steady as the platform moves up and down with the waves. The cylinders must be replaced often due to wear and tear from friction and corrosion. The researchers have developed a durable, non-corrosive, friction-reducing coating that extends the lifetime of the equipment.
Other researchers have made use of the TribologyLab to develop better surface coatings for ball and socket joints in hip prostheses. The laboratory has a 3D microscope that reveals the structure of different surfaces while other instruments show the wear and corrosion occurring over time.
Translated by: Glenn Wells/Victoria Coleman