This article was produced and financed by The Research Council of Norway
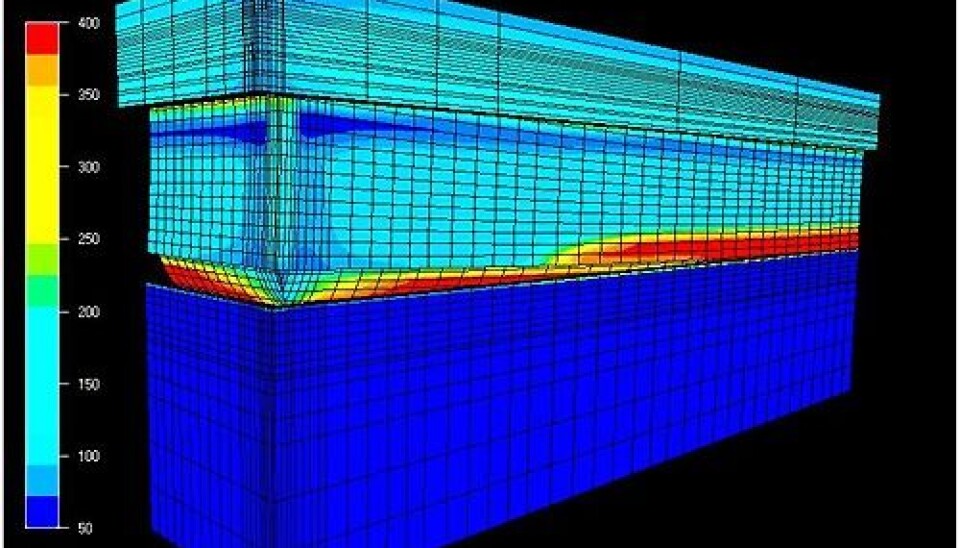
Modelling modules lead to higher-quality aluminium
New modelling tools that show the impact of even minute adjustments to the casting process on casthouse products will give the aluminium industry a significant competitive advantage.
Denne artikkelen er over ti år gammel og kan inneholde utdatert informasjon.
The aluminium industry is facing three challenges in particular: increasingly complex products, demanding customers and ever more stringent recirculation and recycling requirements.
This means that the industry is in need of a predictable and reliable casting process that is not based on trial and error.
The research being carried out in the "Modelling-assisted Innovation for the Aluminium DC Casting Process" (MINAC) is of interest both for the quality-focused automotive industry, which is striving to develop cars that are lighter and more environment-friendly, and for the construction industry, where the products used must also satisfy stringent requirements.
World leaders in casting models
“The key factor behind the project’s success has been the expertise of the Institute of Energy Technology (IFE) and SINTEF Materials and Chemistry," says Hydro Aluminium’s Ole Runar Myhr, project manager of the MINAC project.
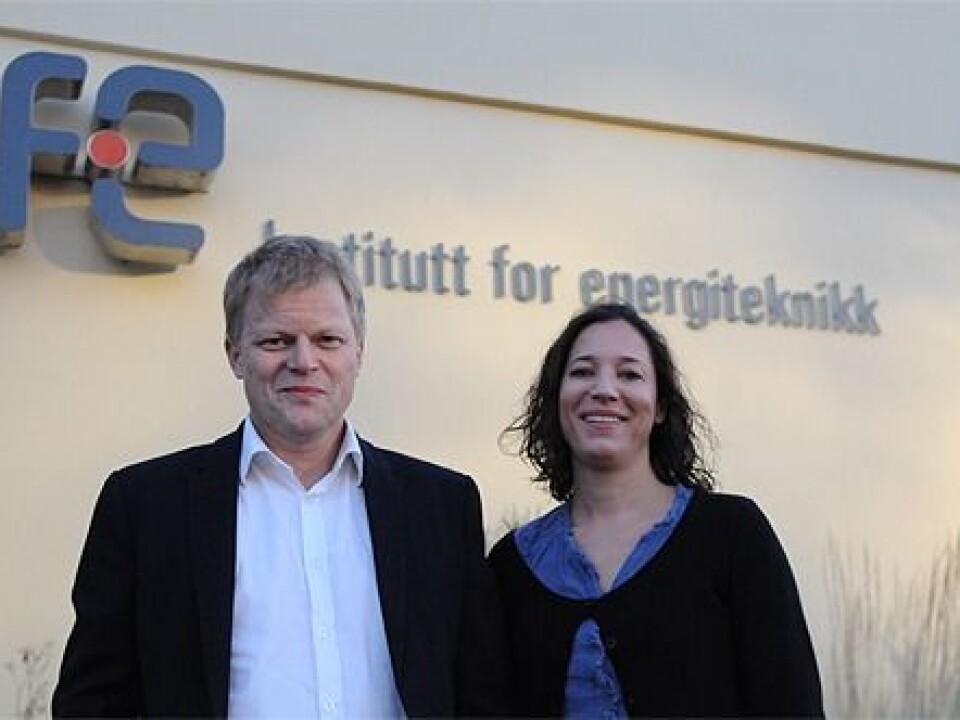
"These groups are world leaders in the development of casting models for the aluminium industry.”
Aluminium is one of Norway’s largest export products. The automotive and construction industries are both large consumers of Norwegian aluminium. Most of the aluminium exported is primary aluminium, an alloy produced via an electrolytic reduction process.
But the industry is changing and the emerging trend is to use more recycled materials in cars as well as in construction.
“Producing aluminium the first time around is a relatively expensive and energy-intensive process. After the initial production, however, aluminium can be re-melted and recycled countless times,” Myhr explains.
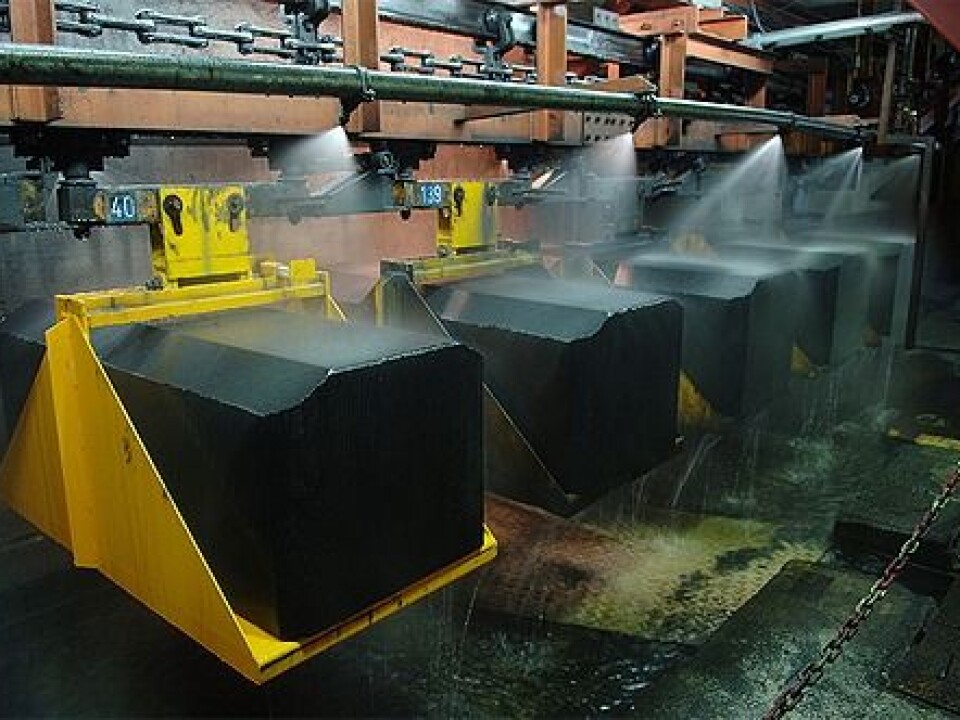
“The recycling process we are working on is far less costly than the initial production process, largely because the total amount of energy needed for recycling is only five percent of what was used originally. These savings, combined with more environmentally sustainable processes, make it far more attractive to use recycled aluminium,” he points out.
Simulating outcomes
The aluminium casting process entails multiple challenges, caused among other things by impurities and variations in chemical composition in the material to be cast. Both factors can compromise the final product through the formation of cracks, uneven surface quality and more.
For example, if intrusions or overly large particles arise during the casting process, the resulting sheet ingots that are later rolled into aluminium foil may contain weaknesses and tear easily, and the final product may prove defective.
Launched in 2009, the MINAC project builds on researcher-driven expertise from as far back as the early 1970s. The objective has been to create and further refine modelling tools that the aluminium industry can use to simulate the outcomes of choosing certain alloys and casting parameters, thereby increasing processability. Greater predictability in the casting process reduces the occurrence of casting defects which otherwise result in large additional costs.
Another increasingly important area of application for the simulation tools developed under the MINAC project include the certification of new alloys for high-demand customers in the transport and construction sectors.
No more trial and error
Ellingsen and Myhr are both enthusiastic about the potential of these models to enhance the competitiveness of the Norwegian aluminium industry.
In the global market, companies such as Hydro Aluminium and Alcoa are often competing against producers of aluminium in countries where the material can be produced at a much lower cost. Myhr explains that none of Hydro Aluminium’s rivals have such advanced models at their disposal.
“It is simply amazing to be able to know ahead of time how fast the casting process can be carried out without any defects arising, or that it is possible to predict that adding a certain amount of a different element to an alloy can increase its strength by, for example, ten percent,” says Myhr.
“We can also render a product with a sounder sub-surface structure by adjusting the casting parameters or chemical composition. Even if the method can not predict an outcome with complete accuracy, the models provide a very reliable indication of how casting defects arise and how to avoid them. In other words, this is a tremendous advance over learning by trial and error,” he adds.
Promise in combining models
Once the aluminium industry has improved the casting process so that aluminium parts can be produced faster, in the correct shape, with fewer defects and thus more uniformly, the results will be of great significance to the array of increasingly discerning customers.
Developing alloys for new products also boosts competitiveness significantly. Even minor improvements in the casting process can have an enormous impact. For one, the use of modelling tools makes it possible to reduce the amount of time needed to certify new alloys for use in the automotive industry.
Another important objective of the MINAC project has been to make the models as user-friendly as possible. Ellingsen from SINTEF Materials and Chemistry explains that the models in question are very data-intensive and that it previously took up to several days to carry out a new calculation. Not only has the process become quicker, it is also possible to carry out more complicated calculations.
“This is an area that requires further work, both to improve the models in terms of computational speed and to enable them to deal with a more complex range of metallurgy and physics problems. The potential for combining these models with other models further down in the value chain is very promising,” Ellingsen concludes.
Translated by: Glenn Wells/Carol B. Eckman