This article was produced and financed by The Research Council of Norway
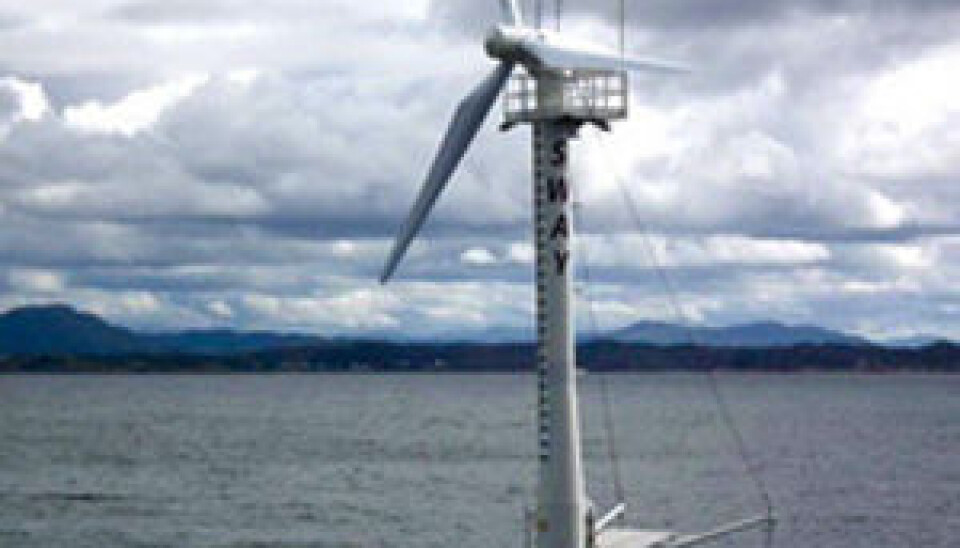
Sound solutions for offshore power plants
Building wind turbines that withstand salty storms at sea is relatively straightforward – but doing it on a large scale while keeping costs in check is far less simple. Now new solutions are on the way.
Denne artikkelen er over ti år gammel og kan inneholde utdatert informasjon.
Norwegian researchers and engineers are joining forces to develop cheaper, lighter and more efficient solutions.
Many technological challenges need to be overcome for offshore wind power to compete pricewise with other new forms of power production. Maintenance and installation are just two obstacles in a harsh, salty environment where tremendous forces act on the equipment. Several pieces of the puzzle must come together to produce cheap, light and efficient wind turbines.
Maximising power
Wind farms can get the most out of nature’s forces when the turbines are optimally aligned relative to each other. To achieve this, designers must be able to simulate the effects of wind and waves on turbines and their foundations.
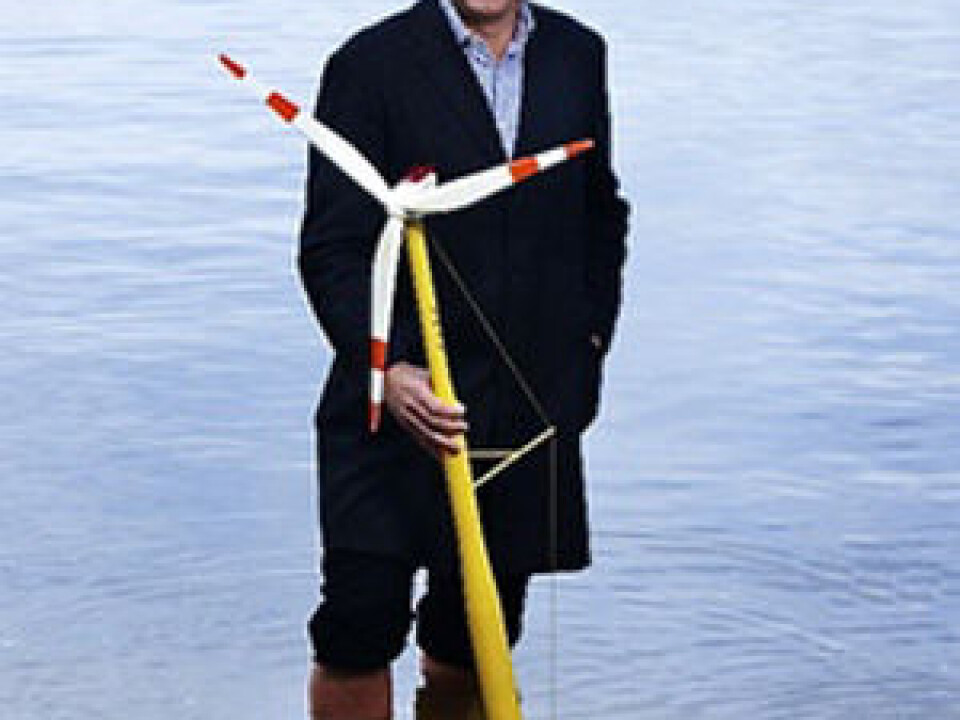
Until now no tools have been available for calculating how wind turbines and their foundations react as a unit to the forces of wind and waves. New solutions have been developed through a collaboration of Norwegian research groups and industry players, according to project manager John Olav Tande of SINTEF Energy Research.
“Our solutions help to make sure the turbine and foundation are properly dimensioned and constructed for their actual operating conditions. Important other objectives are to ensure durability and minimise expenses,” says Tande.
Optimal use of winds
The project also studied how the wind farm as a whole – not simply each individual turbine – could best utilise wind resources.
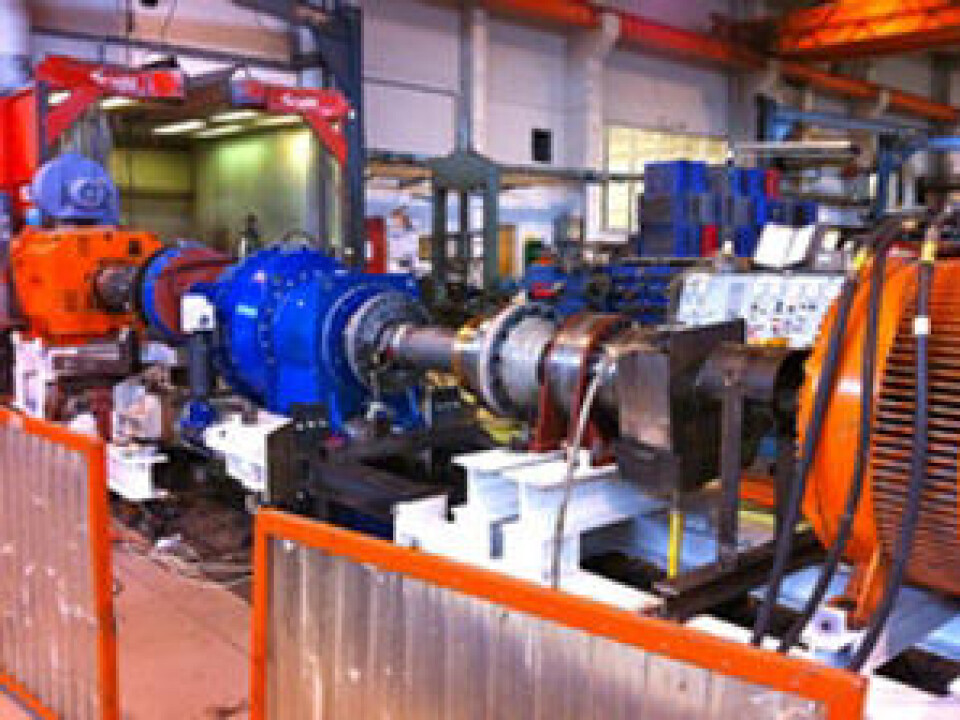
The researchers showed how overall power generation can be increased through coordinated regulation of a wind farm’s many turbines. For instance, by partially reducing the output of the first upwind turbine, the downwind turbines receive more wind – so that on the whole the wind farm produces more electricity. The researchers used wind tunnel trials as well as mathematical calculations to study these complex interactions.
Lighter weight cuts costs
Based on their experiences with a smaller-scale prototype, the renewable energy company Sway plans to construct a full-scale, 5-MW floating wind turbine to be tested off Norway’s southwest coast.
The 5-MW turbine structure will be a giant, its tower projecting 96 m above the surface and 110 m below, with a rotor diameter of 130 m. Turbines of this scale are suitable for deployment 10 to 60 km offshore and anchored at depths of 80–400 m.
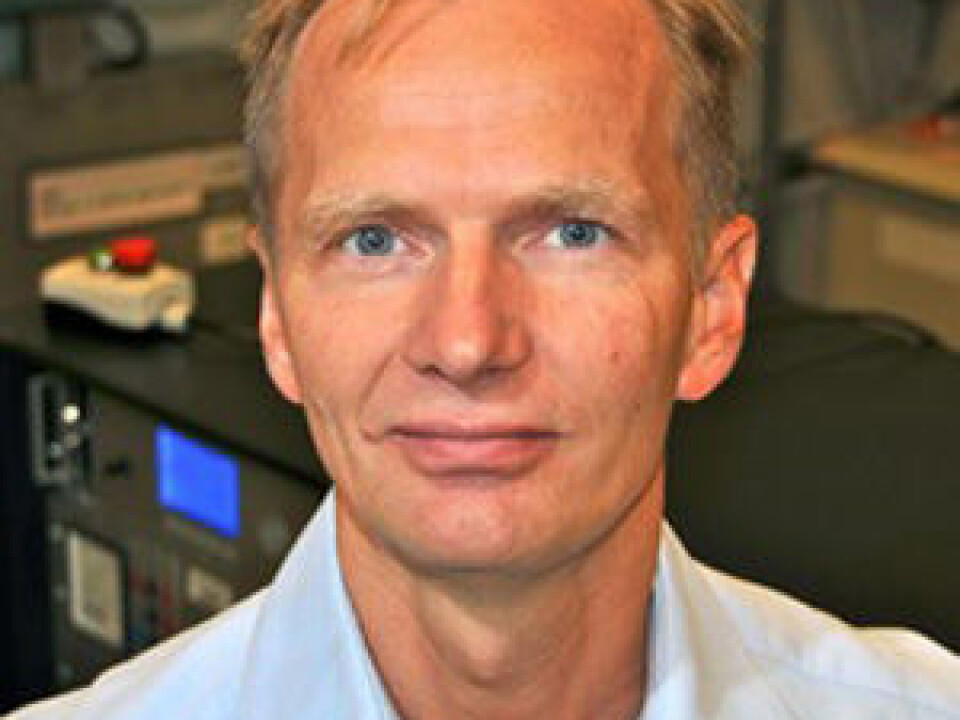
“Our foundation is just one-third the weight of other wind turbine solutions for deployment offshore,” explains Sway CEO Michal Forland, “which entails substantial savings.”
Sway’s floating wind turbines are expected to cost less to produce than bottom-fixed installations for depths of 25 m or more.
“Our target is to have our floating wind turbines ready to sell within three to four years,” continues Mr Forland.
Gearing up for cheaper wind power
Another example of substantially cutting the costs is provided by Norwegian company Angle Wind and its partners. They have developed a new type of eccentric gear configuration, extending the product’s life span and saving big money.
Gears account for roughly 14 per cent of a wind turbine’s cost; only the tower and rotor blades cost more to construct.
Fewer parts, lighter weight
Angle Wind’s eccentric gear design features integrated bearings and consists of roughly 40 per cent fewer moving parts than a comparable planetary gear configuration. This makes the gearbox lighter yet sturdier, extending its life by at least 30 per cent.
“Our solution is far more reliable and cost-effective than what is available now,” asserts Anders Dirdal, CEO of Angle Wind.
Energy producers have high hopes.
“We see the potential for Angle Wind’s new solutions for wind power, both on land and offshore,” confirms Mette Kristine Kanestrøm, head of business development for the major Norwegian energy supplier and project partner Lyse Produksjon.
According to plan, the gear configuration will be market-ready in four years’ time.
Windpowered petroleum installations
Offshore wind power plants can provide a critical source of electricity for oil and gas installations.
Norwegian offshore installations currently consume 20–25 TWh per year, virtually all of which is produced by natural gas-fired turbines located at the installations.
“If instead we could feed that consumption with clean, renewable energy such as wind power,” explains John Olav Tande, “it would be an effective measure for reducing CO2 emissions substantially. At a price of roughly 0,1 Euro per kilowatt produced by offshore gas turbines, and with natural gas prices expected to rise, offshore wind power is not far from being competitive in price.”