This article is produced and financed by NTNU Norwegian University of Science and Technology - read more
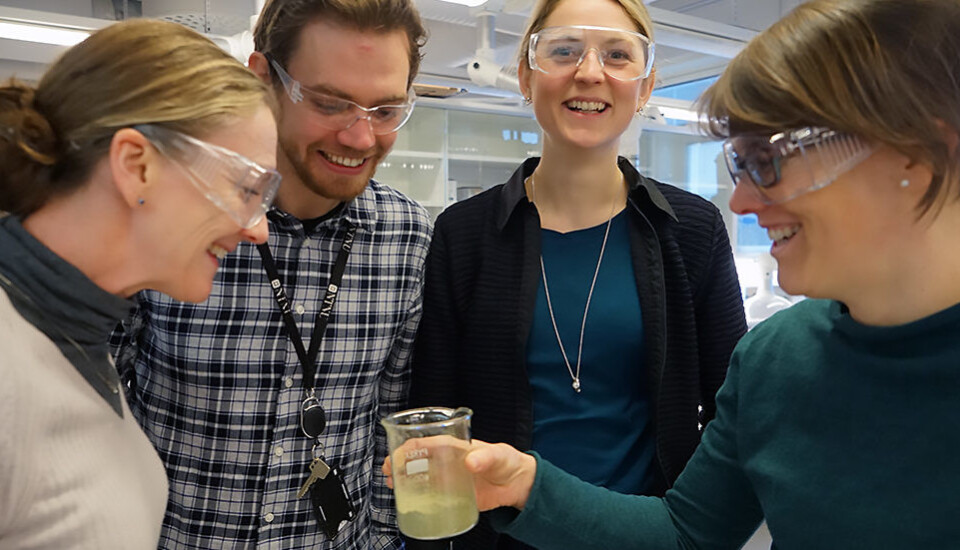
Energy from algae coming your way
We need batteries that can store more energy. Algae may be a solution.
Andreas Nicolai Norberg, a researcher at NTNU’s Department of Materials Science and Engineering, holds up three small jars in the battery lab.
“Here you can see the algae that comes into the lab,” he says.
One is filled with liquid green algae. Another is filled with algae that have been cleaned and dried. The third is filled with pure silica from the cellulose of algae. NTNU researchers are hoping that the jars’ contents will become the future of green battery for Norway.
“This could be the starting point for a new, circular economy. CO2 from Norwegian industry can be captured and used to grow algae, which in turn can be used to create environmentally friendly batteries and contribute to the green revolution,” says Norberg.
Great need for new technology
A battery consists of two electrodes – a cathode and an anode – and an electrolyte that separates them.
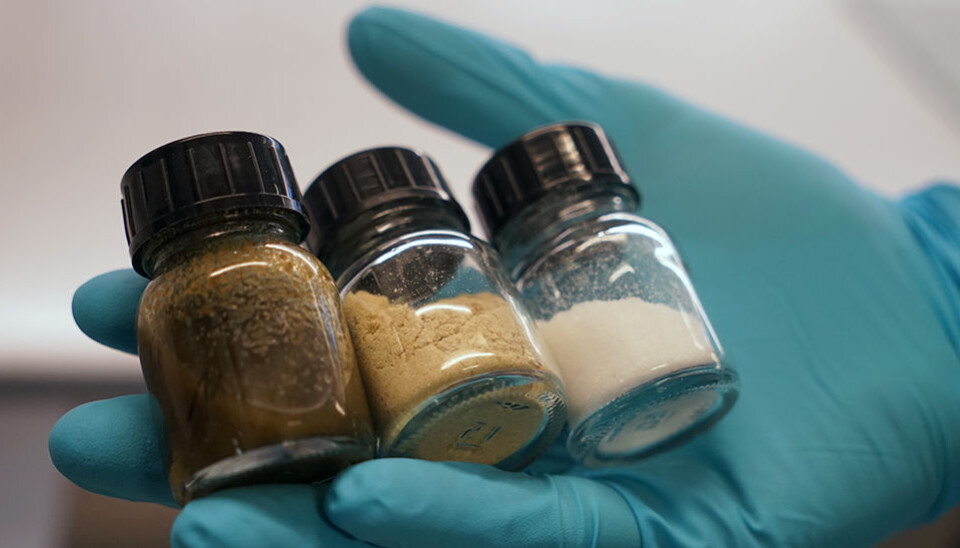
“Graphite is the material that has been used in the anode since the 1990s, and the industry has managed to push the performance of this technology as far as it can go. So there’s a huge need for new technology. What we’re doing is replacing graphite with pure silicon oxide from the algae shell,” says Associate Professor Fride Vullum-Bruer at NTNU’s Department of Materials Science and Engineering.
Perfect for batteries
It’s been five years since Vullum-Bruer had the idea of testing algal membranes for use in batteries.
“We harvested our first algae from the Trondheim Fjord. It was a green goo, but the results turned out to be far better than anyone had imagined,” says Vullum-Bruer. She says the algae’s construction is ideal for making energy-efficient batteries.
“The membranes of the algae have a special nanostructure that allows them to work well in batteries. We’ve tried other types of silica that don’t work as well. We don’t quite understand why the various algae types work differently, but it may have something to do with how the shell is constructed at the atomic level. We’re working on figuring it out,” says Vullum-Bruer.
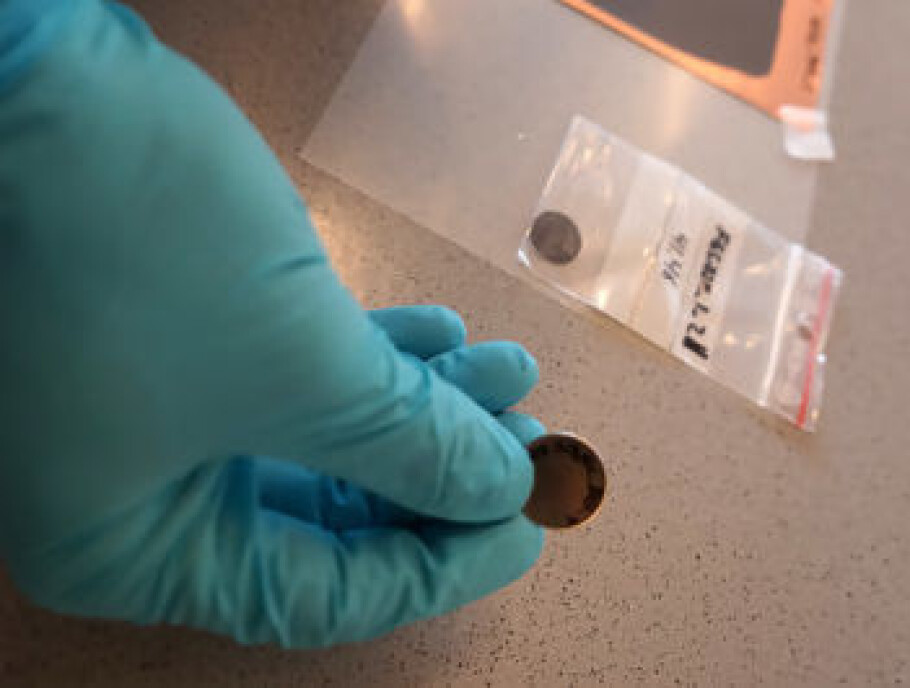
Essentially, the shell is used for diatoms (silicon oxide) which grow naturally in both saltwater and fresh water.
Triples battery capacity
Currently, the research team makes small button batteries by hand, and the testing is done on a small scale.
“In the lab we’ve managed to create anodes that have three times the capacity of today’s graphite anodes. Capacity is what determines how far you can drive an electric car before you have to charge it,” says Norberg.
As the battery evolves, the researchers foresee that the technology will be able to improve all kinds of rechargeable lithium-ion batteries. These are the batteries that can be found in today’s mobile phones, computers and vehicles.
Algae from Norwegian CO2
Next, the research team will be running tests on algae from the ferrosilicon producer Finnfjord AS in Troms county.
The smelter and the University of Tromsø are collaborating to grow algae from CO2 on a pre-industrial scale.
“A lot of heavy industry in Norway has the potential to produce algae for battery production. The algae from Finnfjord are a little different from what we’ve tested before, but they’re in the same family,” says Norberg.
Basic research and commercialization
Developing a new battery is a process that takes many years, and it’s a big leap from lab work to industrial use. NTNU has two projects that are working on developing algae batteries. One of them is Diatoma, a commercialization project under the auspices of NTNU Technology Transfer (TTO), which has received funding from the Research Council of Norway’s programme FORNY.
“Our goal is to create an algae battery prototype that meets industrial standards. We’re aiming to scale up from the lab and approach the industrial market,” says Susanne Jäschke, Innovation Manager and project manager of the Diatoma project.
With her on the team is Kristin Lønsethagen, Innovation Manager at NTNU TTO.
“We’re planning to work with both material manufacturers and cell producers and are now on the lookout for a larger commercial partner,” says Lønsethagen.
The second research project, Bio-degradable Li-ion battery anodes (BioBatt), is funded by the Research Council’s NANO2021 programme to further develop the anode part of batteries so they are composed of an environmentally friendly and biodegradable material.
“Through the NANO2021 project, which has a total budget of around NOK 10 million, we’re delving deep into the technology to find out how this really works at the most basic level of the material,” says Vullum-Bruer.
“It’s magical that nature has made this material for us,” says Lønsethagen.