This article was produced and financed by NIBIO - Norwegian Institute of Bioeconomy Research - read more
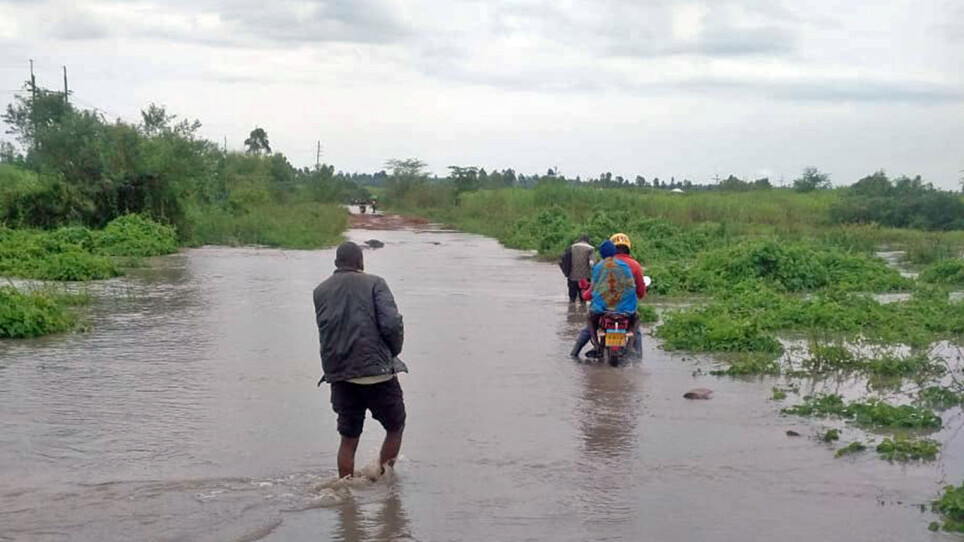
Coping with challenges in a Kenyan biofuel project: First flooding, then COVID-19
A Kenyan research and development project that aims to produce carbonized biomass briquettes from agricultural residues, has faced unexpected risks this year. First a major flood, followed by Covid-19 putting local communities in a highly vulnerable state.
2020 has been a tough year for the project partners and local employees in the project Biofuel4Kenya. From October 2019 till March 2020, local communities in Ndhiwa Sub-County on the East side of Lake Victoria were severely hit by a continuous and unusually heavy rain that caused flooding, and Lake Victoria to swell.
The devastating effect of the long-lasting and heavy rains and floods in the region led to significant problems on access roads leading to project sites. An already bad road to the main production site was severly damaged.
This made it difficult to transport supplies of sugarcane bagasse to the production site, as well as exporting biomass briquettes to the local markets. Due to heavy rain, there has also been a lot of trouble with electricity supply and frequent power outages.
Towards the end of the flooding period in March, COVID-19 arrived. With it came travel bans, limited public gatherings, social distancing and strict infection control measures. The pandemic has drastically challenged the way the project was running, particularly in regard to monitoring and implementation of key project activities.
Partners had to adapt to fluid circumstances to continue project implementation. To cope with some of the challenges, the project had to amend the damaged road, change the project management model, and implement daily video reports from the project in a WhatsApp-group.
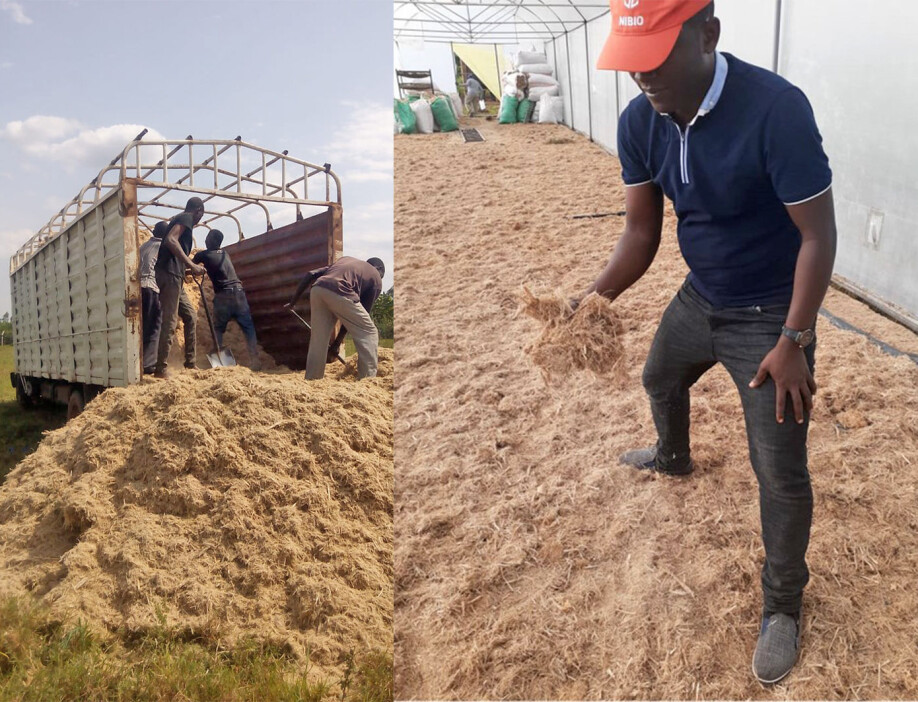
Amendment of road to reopen supply chain and access to the villages
Even before the COVID-19 travel ban struck, the flooding in itself led to a naturally caused travel ban as far as field visits were concerned.
"Back in February and early March, it was difficult to visit the project sites due to the floods. Although we arrived with difficulty, it didn’t feel right to bring up the project with people who were struggling to cope with a flood," says Dr Belachew Gizachew, researcher from NIBIO and Biofuel4Kenya coordinator.
Long-lasting and heavy rains and floods in the project region from October 2019 till March 2020 has caused major problems on access roads leading to project sites. An already bad road to Biofuel4Kenya’s main production site was severly damaged. This made it difficult to transport supplies of sugarcane bagasse to the production site, as well as exporting biomass briquettes to the local markets. (Video: Adam O'Toole)
He explains that in such a situation, priorities change, and some basic restrictions need to be dealt with first.
“The road and culverts were completely gone. There was no way we could get to where we wanted without the roads,” says Dr Gizachew.
To begin with, the project allocated money for a tractor that could drive off-piste. The tractor carried supplies to the briquette factory and made deliveries to the market. The flood cost the project an extra 200 000 Norwegian Kroner, to partially cover the expenses of amending the damaged road. This was done in cooperation with a local sugar factory, Sukari industries Ltd.
“The amendment of the road is still ongoing. We introduced the Norwegian concept of dugnad, as in that members of the community agree to contribute with free labour to the road repair and provide free lunch every day for the machine workers and assistants,” explains Gizachew.
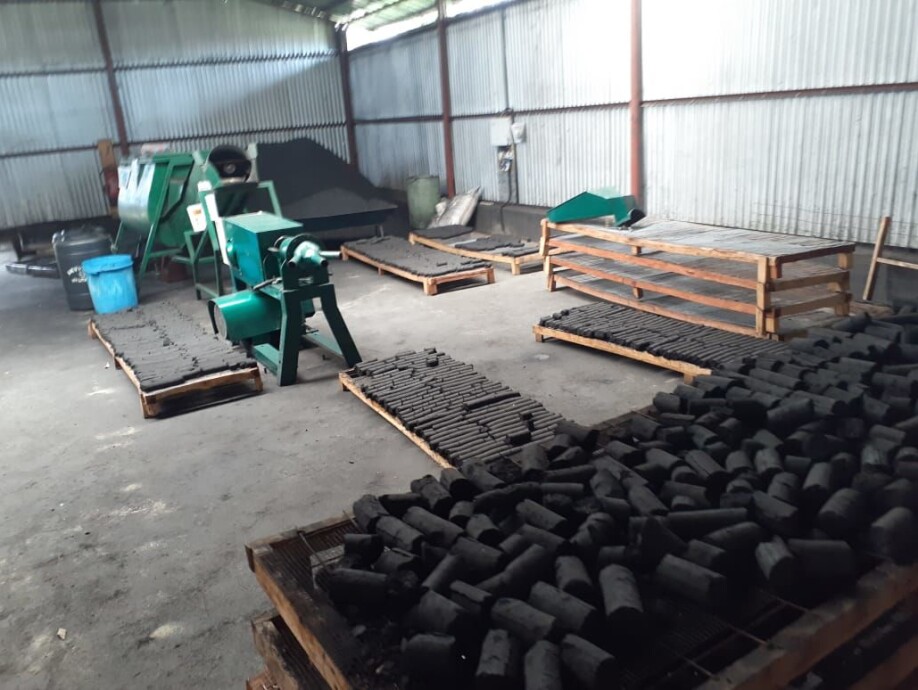
After flooding came COVID-19

In March when Covid-19 really entered the global agenda, and reached Kenya, the project faced even more challenges.
“Kenyan guidelines for COVID-19 infection control were strict. The work force was reduced to a maximum of four people and people had to work shifts and wear masks,” says Gizachew.
However, the salary expenditures are still the same as they were before.
“Most of the people we already had in employment depend on the project to make a living and have an up to three-year contract. Also, we could not reduce the work force because we must be ready to upscale again as soon as possible,” explains Gizachew.
To be able to follow up the project without travelling to the project site, all decisions are now taken in meetings with representatives from the local management in cooperation with partners from Norway.
The coordination office in Nairobi is in contact with project staff and partners on a daily basis, via telephone or WhatsApp, to oversee activities, motivate progress, and direct the next activities. A WhatsApp group has become a central part of the project management, in which local employees regularly post videos and pictures to document progress on activities. More frequent meetings on Skype and Teams have been instrumental for effective virtual partner consultation at project management level.
A WhatsApp group has become a central part of project management, in which local employees post daily videos and pictures to document progress on activities. This is one of the measures to keep the production going during COVID-19. Here, a demonstration of four of the 25 new kilns for biochar production which are now ready for use.
Coping with delays and budget expenditures
The pandemic has restricted travels between the project coordination office in Nairobi and project sites, in addition to restrictions in regard to public gatherings and meetings, particularly during the period of March to July 2020. Furthermore, travels between Norway and Kenya were all cancelled. This means that a lot of training and public demonstration events have been cancelled this year.
Dr Gizachew emphasizes that although the project has had a significant amount of extra expenditure, it has also saved a lot of money on cancelled travels and events. This money has been allocated to cover extra expenditure in the project.
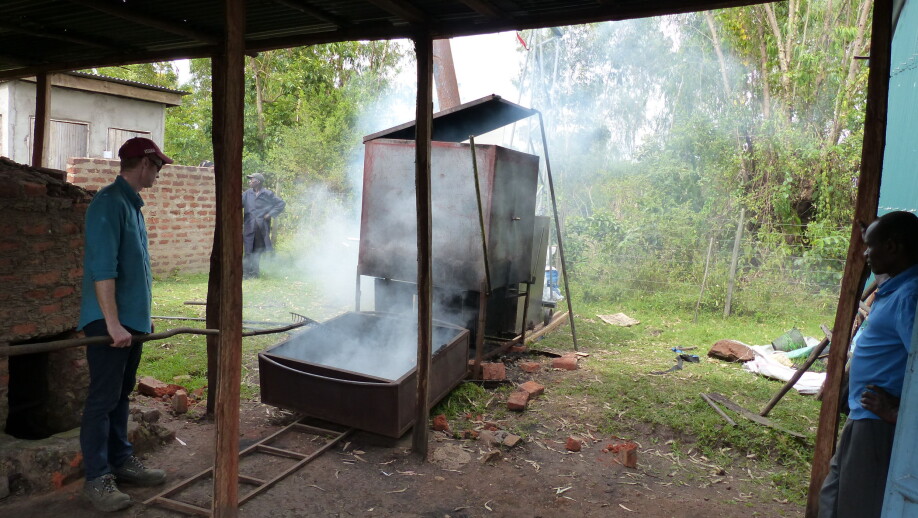
“At the same time, we are considering how to cut our expenses. For instance, by introducing reforms on priority of activities, looking into options for renting buildings for training on short term basis – instead of constructing buildings, and changing the roles of some of our sites based on cost effectiveness.”
The project management has also had a dialogue at an annual meeting with Norad, the project’s financing body, to discuss possibilities for a no-cost extension period.
This video shows wet sugarcane bagasse delivery. During the prolonged rainy season, drying bagasse in an open sun was challenging. A custom-made green house with wind driven ventilator solves part of the problem, while reducing bagasse drying from 3 days to one day. Bagasse is normally very wet because the sugar cane itself is wet and on top, water is added during sugarcane crushing into juicing. (Video: Adam O'Toole)
“The impact of the flooding and COVID-19 has been huge for us and the project, we are at least six months behind schedule. However, on the positive side, our activities in this project are not dependent on the season, like they would have been in an agricultural project. This means that even though we are behind schedule, we continued as soon as it was practically possible, as we learned how to cope up with Covid-19.”
The annual progress report shows that many activities were carried out despite disruptions by unusually long-lasting rain, floods and the COVID-19 pandemic. For instance, activities related to technical outcomes such as production of a new briquetting machine, carbonization kilns, skills development and pilot production continued, leading to test production during the project’s second year at two of three sites.
Reference:
Hilde Halland mfl.: Transnational cooperation to develop local barley to beer value chains, Open Agriculture, 2020.
From sugarcane bagasse to charcoal briquettes: Biofuel4Kenya contributes to the development of a sustainable alternative to wood charcoal in Kenya.