THIS ARTICLE/PRESS RELEASE IS PAID FOR AND PRESENTED BY NTNU Norwegian University of Science and Technology - read more
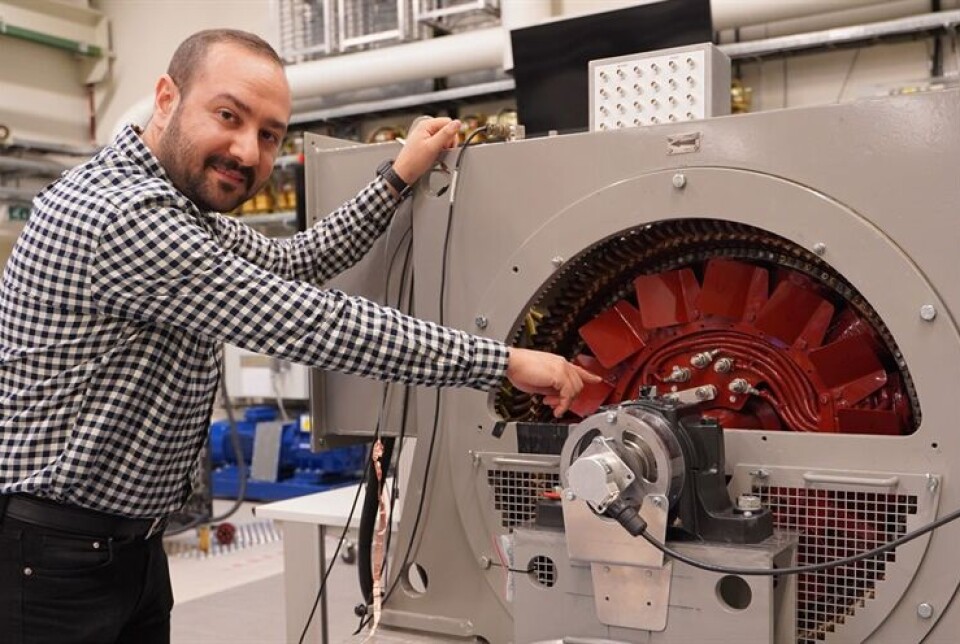
Miniscule signals from electric motors can prevent major accidents
Listening to electric machines' magnetic fields can detect faults in the electric cars in time.
“What we do can be compared to what a doctor does, where the electric motor is our patient. In the same way as a doctor performs an EKG examination of the patient’s heart, we collect signals from the machine and analyse them,” Hossein Ehya, a researcher at HydroCen and NTNU, says.
Electrical failure can cause a crash
Imagine that you are driving on the motorway in your Tesla, perhaps at 100 to 110 kilometres per hour. Suddenly your car starts to accelerate, the speed increases and you are no longer able to control the car. Then you crash into a rock face.
The dramatic consequences of an electric motor failing are easy to imagine.
“Several accidents like this have happened since 2010. Imagine what could happen if you had this kind of fault in an electric passenger plane. Politicians are pushing for all-electric planes, and Norway is one of the leading countries in electrification. If an engine in an electrically powered plane suddenly stops, in a worst-case scenario the plane could crash,” Ehya says.
Studying generators in hydropower plants
Ehya has a master’s degree from the University of Tehran but chose Norway and NTNU to do further research on monitoring and diagnosing electric motors. The doctoral work that Ehya has carried out at HydroCen, a Centre for Environmentally Friendly Research, has the potential to create new technology workplaces linked to electrification and the green shift.
“What we need is equipment that is affordable, easy to use and that can pre-emptively detect faults,” he says.
So far, the large generators at Norwegian hydropower plants have been the focus of research on machine learning and troubleshooting using magnetic field measurements.
Faults and damage inside plant generators can result in large expenses for Norwegian hydropower plants, when they are forced to interrupt production to look for faults and repair them.
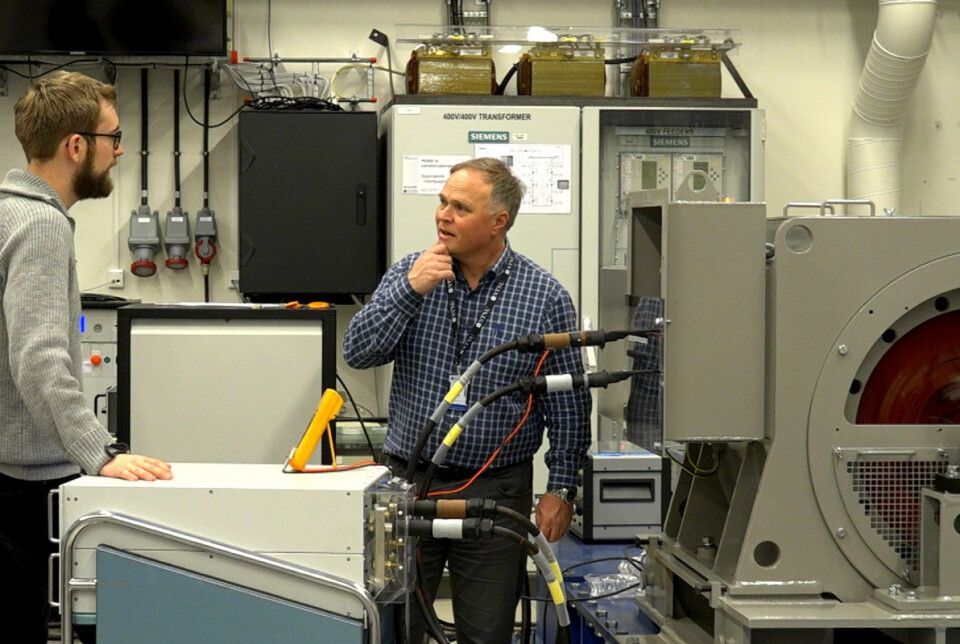
Like a medical check for electric motors
Hydropower plant generators were often installed several decades ago with little understanding of the machine’s zero state – that is, how it should work before any errors occur. This makes troubleshooting with today’s diagnostic tools difficult, says Ehya.
“A lot of methods for finding faults in generators require knowing how they behave when they’re ‘healthy.’ But often such precise analyses aren’t carried out before the generators are put into use. For example, we can measure vibrations in the generator and in that way determine that something’s wrong, but we can’t say exactly what is wrong,” he says.
Any number of things can go wrong inside an electric motor.
You can get a short circuit in the stator, the stationary part of the motor where the coils are, or in the rotor itself, the moving part that together with the stator creates the magnetic field in the motor. The rotor can become skewed, or other vital components can suffer mechanical damage.
“An electric motor doesn’t give us any sign of failure – until it breaks down. That’s why periodic inspections have to be carried out. The machine has to be stopped to check for faults and to carry out maintenance, but if the fault can’t be found during the inspection, the machine breaks down,” Ehya says.
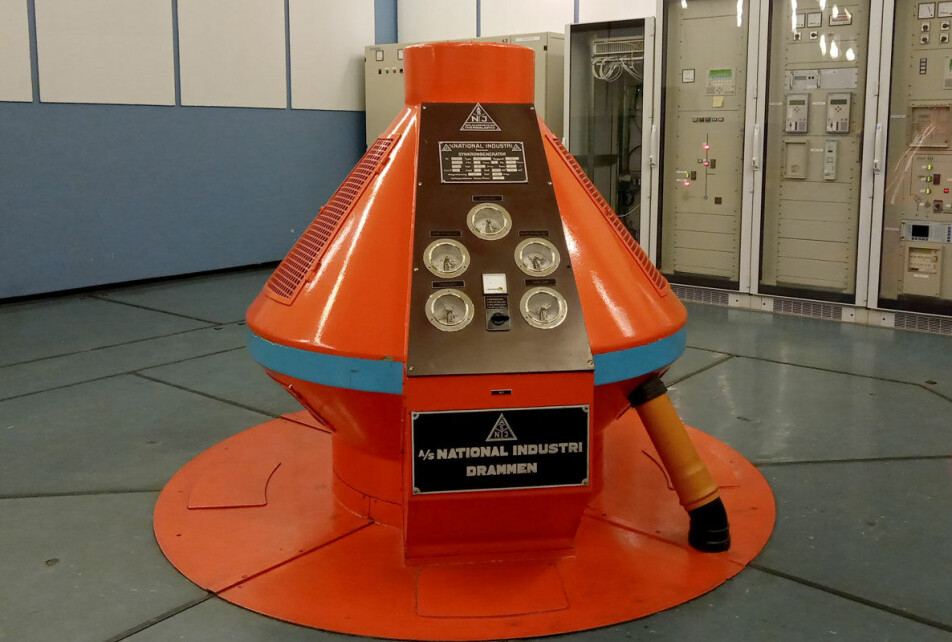
Saves time and money
With current methods, the machine has to either be dismantled to install an internal sensor or inspected using external measuring equipment.
Installing a sensor is an extensive job that power plant owners often aren’t too eager to do. External inspections measure vibrations or variations in voltage, which can tell us whether something is wrong or not, but the equipment is not very sensitive and is often used when it is already too late.
“With our method, we use a very affordable sensor that can be mounted in a few minutes on the outside of the machine. The sensor measures the machine’s magnetic field and analyses it. The researchers can then determine whether the machine is healthy or has failure symptoms. They can also identify what the problem is,” Ehya says.
According to the researchers at HydroCen, the new technology can save power producers large sums of money. The costs of stopping and dismantling a generator can quickly add up to many tens of thousands of Euros, while also running the risk of losing income when production stops.
With Ehya’s sensors, the machine can instead be monitored and the data analysed in the cloud using artificial intelligence.
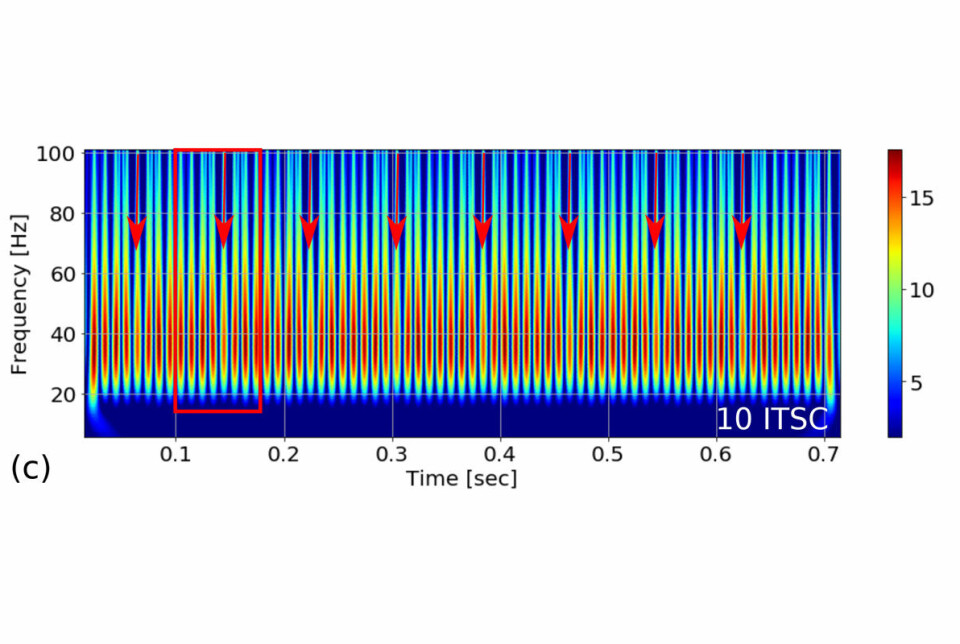
Norwegian production
So far, the new method has been tested on generators at two Norwegian hydropower plants, but Ehya and his colleagues envision that it will be useful in the automobile and transport industry, on Norwegian oil platforms and for wind power as well.
The project is now in a commercialisation phase where the research team is collaborating with Rolls Royce, IKM, Statkraft and Captiva. And Ehya has no plans to take the patents out of Norway.
“The Research Council of Norway has contributed EUR 500,000 to enable us to continue our work. This is Norwegian oil money, and money that Norwegian taxpayers have contributed. If my work here can lead to us being able to create jobs and income in Norway, I will do it. It’s my way of being able to give back a little for the support I’ve received here,” says Ehya.
Read more content from NTNU:
-
Sunlight and oil solve a dirty problem
-
Voting from your sofa is secure enough. But will it be allowed?
-
It's entirely possible to make housing construction more environmentally friendly
-
Lipoedema: Sunniva had tried every diet – but with little success
-
New laser can improve self-driving cars and the internet
-
Unlocking the secrets of Viking and medieval walrus tusk trade