An article from Norwegian SciTech News at SINTEF
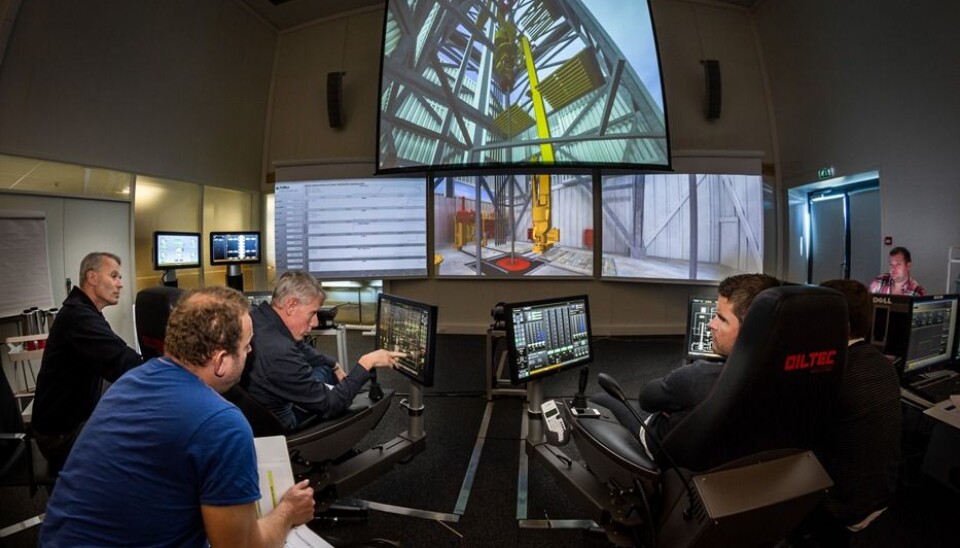
Driller thriller
Drilling an oil well is not what it used to be. The job needs its own special tools, the dexterity of a pilot, and bundles of experience.
Denne artikkelen er over ti år gammel og kan inneholde utdatert informasjon.
At Forus just outside Stavanger, Norway, seven men and two women sit in what looks very like a dimly lit cinema auditorium. They are in the premises of the simulator company Oiltec Solutions. Expressions like “kick”, “mud” and “tool pusher” float around the room, and on an enormous screen a yellow industrial robot is raising part of a drill-string.
At the front sit two men in futuristic stressless chairs, each of them moving a set of joysticks, while they carefully monitor figures and graphs on a row of computer screens. These are the “driller” and the “assistant driller” who are controlling the enormous tool on the big screen, as it efficiently seeks its way forward, thousands of metres below the seabed – and into the petroleum reservoir.
“Just remember that the last set of course participants were 'thumbs up' all the time, but suddenly, everything went wrong for them,” says instructor and former driller Just Sverre Wessel.
No more easy oil
The Forus simulator is regarded as one of the world’s most advanced training fields for offshore drilling. Just now, the group is practising drilling the last few metres of one of the wells on the Kvitebjørn field, and concentration lies like a heavy lid on the group.
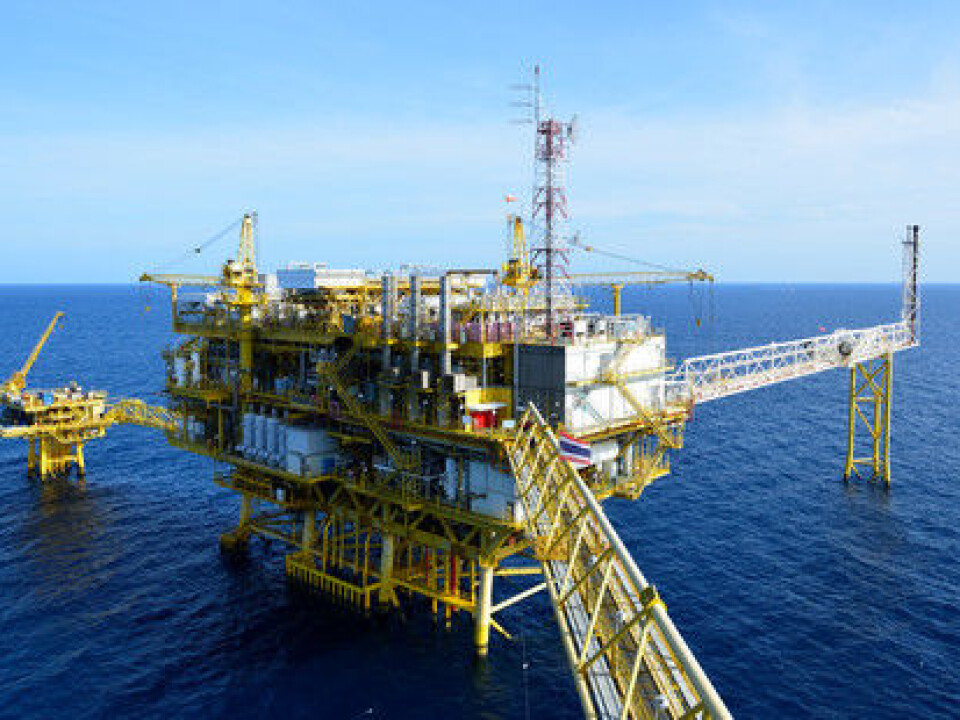
“What we are simulating just now is a Managed Pressure Drilling (MPD) operation,” whispers chief scientist Thor Ole Gulsrud of SINTEF, who leads the Department of Drilling and Well Construction at SINTEF Petroleum Research, which has developed the mathematical model that lies at the heart of the simulator.
MPD needs a special team that controls the well pressure Norway by adjusting the fluid flow every single second of the drilling operation. The aim is to keep the pressure at the bottom of the well completely stable.
“There is no more easy oil, you realise,” says the chief scientist.
“The easy formations will soon be exhausted, which means that this simulator has been given very good reception by the oil companies.”
Demanding depths
The advanced MPD method is becoming ever more widely adopted, because the petroleum that is being produced nowadays lies under great ocean depths and difficult pressure conditions.
“We say that the 'pressure window' is narrow. When we are drilling, it is important to keep the pressure within a narrow range: if it is too high, we risk fracturing the formation and losing drilling fluid. If it is too low, formation fluids may flow into the well. Either of these conditions can lead to loss of control of the well,” explains Gulsrud.
That is why two MPD experts sit beside the “drillers” and adjust the pressure in the deep with the aid of a “choke”; everything they do has to fit like hand in glove. For the operation to be successful, graphs and figures that describe the situation are not enough. The dialogue between the teams – today they are from Statoil, KCA Deutag and Halliburton – must also be perfect. There is no room here for ambiguous warnings or mistakes in the interpretation of signals.
“In just over a week, this group will go out to the platform and do just the same thing in reality. Here, in the simulator, they sit in the same room, but out on Kvitebjørn the MPD experts will be in a different room from the “drillers”. Just now they are gaining invaluable experience of this complex operation. They are getting to know one another as a team and can compare strengths and weaknesses on the dialogue side,” explains Gulsrud.
“There is no other way of getting experience of this sort.”
Millions of calculations
Scenario that is being played out in the auditorium is remarkably realistic. But how is it possible to simulate something as advanced as drilling for oil, where everything from pipe-flows to reservoir properties and the strength of the equipment involved plays a role - and where just about anything could happen?
The answer lies in an enormous number of equations, and with a handful of SINTEF research scientists who are extremely interested in fluid dynamics and mathematical modelling.
The petroleum scientists of the Department of Drilling and Well Construction have been working for several years on the development of a library of mathematical models that describe what takes place during well operations, and that are used as decision-support tools for the operators out on the shelf.
“The challenges involved in creating the “brain” of such a simulator have been to sew these models together, and no less important, to draw on and add to the mathematical equations that we needed to create an overall scenario,” says SINTEF senior scientist Knut Steinar Bjørkevoll, a physicist.
Because a great deal can happen down in an oil-well; it can collapse for lack of pressure, it may start to leak, or the drill-string might jam - just to mention a few of the possibilities.
After more than two years of development, the simulator has recently been approved by Statoil, the project sponsor. The flow model, which is the heart of the simulator, comprises some 100,000 lines of code. The software is fully integrated with the graphic presentation of what actually happens during drilling, both on the platform and at the bottom of the well.
Ahead of a course, the simulator can be loaded with all the available data from the well that is about to be drilled, so that the drilling team can drill the well in the simulator before they go offshore. However, the simulator can also be used to carry out a post hoc evaluation of an operation. What went wrong, and how can we do things better next time?
“The Deepwater Horizon disaster in the Gulf of Mexico is an example of how badly things can turn out, and how important it is to train and to follow good procedures,” says Thor Ole Gulsrud.
Demand for simulators of this sort is expected to rise in the future, and Statoil has already ordered two new modules.
From full control to null control
In the Forus auditorium, the temperature has risen a couple of degrees. The situation at Kvitebjørn has turned from being under full control to “null control”.
Instructor Just Sverre Wessel’s warning about the mistake of the previous course has suddenly become highly relevant: if the team is unable to prevent the pressure from rising down in the 6000 metre-deep well, it will “kick”. This means that the formation will fracture, and any hope of it being usable in the future will disappear.
“We need to exit the well. All we can do is get out, and we have to get out as quickly as possible,” says one of the men operating the joysticks.
“Correct!”, shouts instructor Wessel, obviously pleased. “Very good. You are only the second team of all those I have had who have come to that conclusion. Here we have to save whatever we can. And just so you know; I set up this well in such a way that you would have been stuck, no matter what you did,” he adds.
In the land of oil they call a spade a spade. Luckily, this is just a simulation. And it has given the team experience that in real life could have cost millions.